The status quo isn’t sufficient. For businesses to stay lean and ahead of the curve, continuous improvement is key — both processes and policies must be regularly evaluated and upgraded to ensure companies can meet evolving customer expectations and keep pace with industry competitors.
But what does this look like in practice? How do companies identify the conditions necessary for continuous improvement, and how do they implement these processes at scale? It all starts with the first step: The gemba walk.
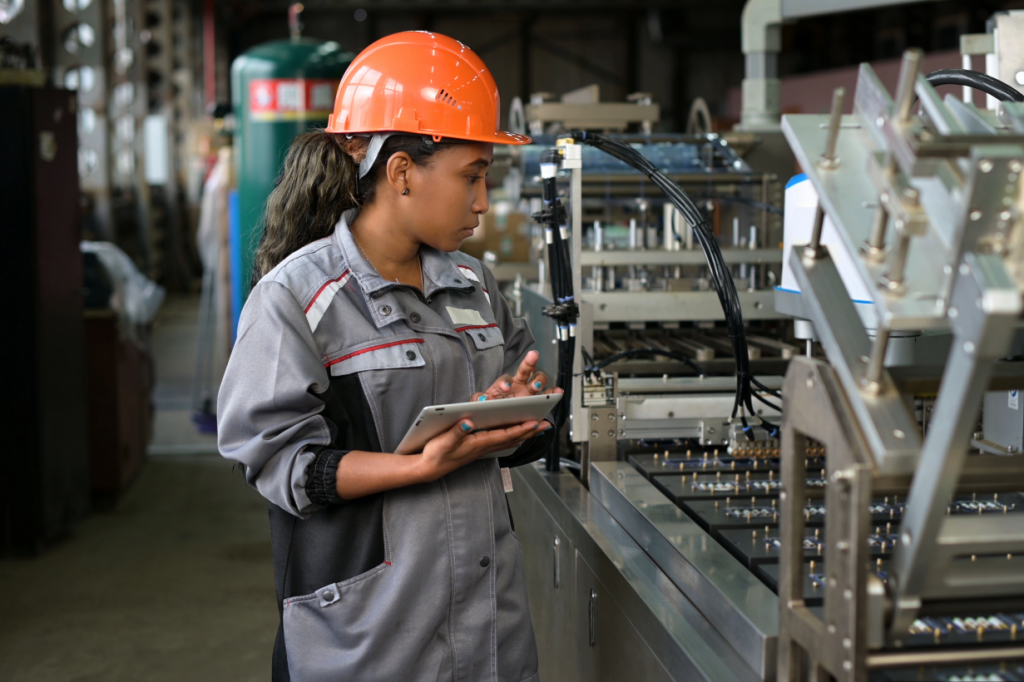
What is a Gemba Walk?
The concept of the Gemba walk started with Taciihi Ohno, who designed the Toyota Production System. This revolutionary approach embraced the Japanese term “kaizen”, which translates to “continuous improvement.” Instead of accepting inefficient processes as they were or attempting to work around them, Ohno sought to eliminate them by identifying key issues and making critical changes.
At the heart of this methodology was the Gemba walk. Gemba is a Japanese word that means “the actual place”, or “the real place”. In practice, a Gemba walk — also called a Gemba walk — sees managers and C-suite leaders leaving their offices to observe where and how work is done in person, in effect delivering management by walking around that aligns with six sigma goals for lean manufacturing processes. This allows them to see where processes are working, where improvements need to be made, and where current operations aren’t living up to expectations.
It also offers the opportunity for leadership team members to interact with employees on the shop floor or manufacturing line and discover how key operations are actually being completed. While standard processes exist to govern these operations, Gemba walks often reveal the disconnect between theory and practice — what sounds good in a board room may be unsustainable in a high-pressure, high-volume manufacturing environment. Gemba walks provide the information leaders need to implement effective processes that deliver continuous improvement.
What are the Primary Purposes of a Gemba Walk?
The two primary purposes of a Gemba walk are to observe current operations and engage employees. Let’s explore each in more detail.
Observing operations
When heading to the factory floor or production line for a Gemba walk, remember the goal is to observe processes as they stand. While potential deviations from policy — along with possible fixes — may be obvious, it’s best not to intervene in operations unless absolutely necessary. Here’s why: Staff completing tasks are already under stress to complete their work and will be doubly worried about executives making the rounds. By making it clear that your purpose is to observe, you can get a better sense of how operations actually occur day-to-day.
Engaging employees
It’s also critical to engage staff who are doing front-line work. Why? Because they’re the ones intimately familiar with how systems work and why things operate the way they do in real-time. Consider legacy technologies often used in manufacturing — these may be purpose-built production machines that are still in operation but whose inner workings are known only to a few experienced staff members. While the temptation here may be to remove and replace this dated machinery, front-line staff can give first-hand accounts of how these tools are connected with other operational elements — and what type of performance losses might occur if these machines are suddenly replaced.
Staff at their stations can also give a sense of overall employee morale — so long as leaders make it clear that they’re on fact-finding missions rather than looking to issue write-ups or warnings. What you’re looking for here are answers about what actually happens on your front lines, not the performative behavior that staff may put on if they’re worried about being penalized. Here, listening to staff concerns goes a long way to understanding why processes are the way they are — and how to start fixing them.
What are the Key Components of a Gemba Walk?
As noted above, the purposes of a Gemba walk are to observe and engage. The ultimate goal of a Gemba walk, however, is to underpin ongoing improvement in lean manufacturing. While observation and engagement set the stage, five components are critical to helping ensure the Gemba walks deliver on their performance potential.
1) Look, don’t correct
Spend a few minutes on the shop floor and you’ll probably spot at least a dozen things that need improvement. When it comes to a Gemba walk, however, it’s not about correcting and problem-solving but observing — creating a catalog of potential problems to remedy but also trying to understand the bigger picture: How well are business processes working together? Are there obvious gaps in policy or procedure that need to be addressed? Are there performance issues that need to be resolved?
2) Find additive value streams
Part of your Gemba walk is about identifying the potential for process improvement. Even those that don’t meet current specifications may have benefits that could be incorporated into new frameworks. For example, staff members at packing stations may have found a more efficient way to pack and process large order volumes that don’t align with current expectations. As a result, it’s worth considering the value of the process if it adds to overall productivity.
3) Identify subtractive concerns
An effective Gemba walk can also help you identify obvious concerns and wasteful activities that don’t align with lean management philosophy. For example, you may see repetitive or redundant processes that only serve to slow down overall processing, or may observe functional issues such as where items or resources are placed that get in the way of staff maximizing their productivity.
4) Seek understanding
Next, it’s important to seek out understanding, especially when it comes to processes that subtract from the overall value. While it may be tempting to perceive a lack of policy compliance as laziness or lack of care, it’s worth taking a look at the bigger picture. If processes aren’t adding up, ask why. Why are staff doing things in a specific order or in a certain way?
5) Consider innovations
Finally, take what you’ve learned and consider innovations that may help streamline work processes and set the stage for continuous improvement. For example, you might look to replace outdated tools or technology or rearrange shop floors to be more efficient. In some cases, specific employees may need to make behavioral changes but regardless of the specifics, the goal remains the same: To remove any impediments to the overall production.
How Long Should a Gemba Walk Take?
The length of time you spend on a Gemba walk depends on factors such as your current objective, the size of your business, and the nature of existing operational challenges.
For example, if your goal is to identify efficiency issues related to a specific process, you may only need an hour or so to speak with front-line staff and discover key concerns. If you’re looking to conduct an end-to-end Gemba walk, this could take a workday (or more) depending on the scope and size of your business. If you’re looking to solve larger-scale business challenges that may be impacted by more than one process acting in parallel, Gemba walks and necessary follow-ups could span weeks.
The takeaway here? When it comes to walking the walk, it’s not about time — it’s about impact. Short or long, if Gemba walks help deliver continuous improvement, they’re worth the effort.
How Often Should You Do a Gemba Walk?
It’s worth conducting regular Gemba walks once a week — or even on a daily basis — for 45 minutes to an hour to ensure that processes are working as intended. It’s also a good idea to conduct more in-depth Gemba walks once every quarter, and anytime a new process, procedure, or piece of technology is added to your workflow.
How Do You Implement Gemba Walk Results?
Implementing Gemba walk results starts with analyzing the data you’ve collected through observation and identifying areas for improvement. If you’ve noticed that initial production stages are working as planned but end-stage operations such as packaging and shipping lack efficiency, it’s worth putting your effort into streamlining these processes with new tools or technologies or by removing existing roadblocks such as redundant data entry or repetitive processes.
Using Gemba Walks to Improve Safety
Along with day-to-day processes, Gemba walks can also be used to improve safety. While safety concerns may not be as immediately obvious — especially if your accident record is relatively clean — it’s easy for leadership to get complacent by looking at the numbers instead of going to the source.
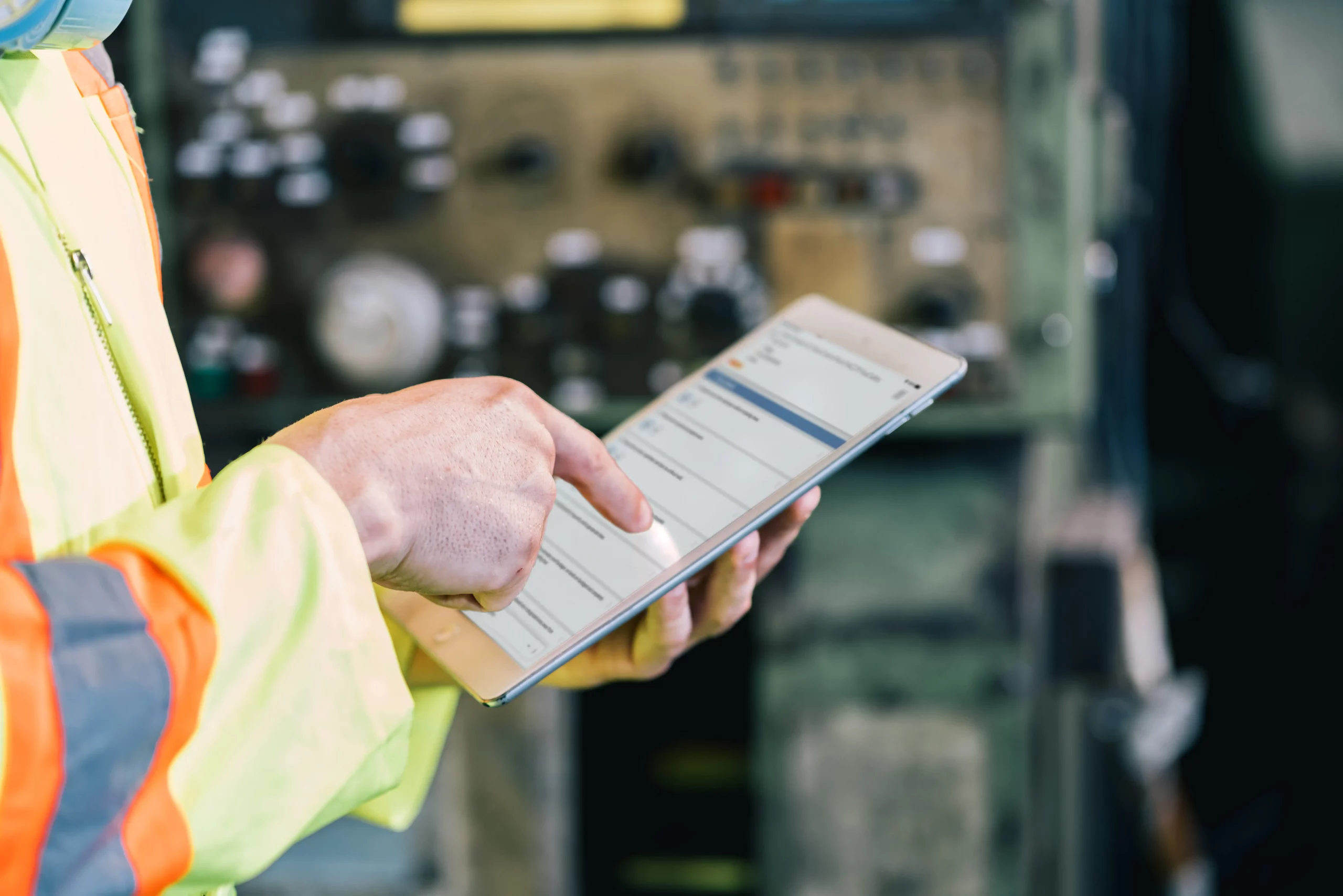
30+ Audit and inspection checklists free for download.
Once in “the actual place”, however, management teams can more easily spot potential issues. For example, staff may not be taking adequate safety precautions when it comes to checking equipment or wearing PPE, or there may be hazards on or around high-traffic routes that could prove dangerous to employees.
When it comes to Gemba safety walks, the goal is to search out potential harms that could be caused by missing safety protocols, or those that are in place but aren’t being followed. In the same way, as traditional Gemba walks, however, the goal isn’t to correct but observe; staff must be able to conduct business as usual while you gather data. Post-walk is the time for analysis, evaluation, and eventual policy decisions.
Leveraging Gemba Walk Checklists
So how do you get your Gemba to walk up and running? Start with a solid Gemba walk template. There are a host of free options available online that can be customized to meet your needs depending on your industry, current output, and overall goals. It’s also worth using Gemba walk checklists to help ensure you’ve covered all the bases when it comes to processes, policies, and safety concerns. Here, it’s worth leveraging different lists for different applications. For example, a job site safety inspection checklist might be used to evaluate overall site safety and identify potential deficiencies, while a lifting and lowering ergonomic assessment checklist is designed to address specific issues around the movement of heavy items safely around your facility.
By ensuring the template and list you use is tailored to your objectives, you can make the best use of time spent walking.
Going the Distance
Gemba walks offer a way for leadership to take responsibility discover what’s really happening on the front lines of their facilities and gain a greater understanding of what needs to change to deliver on the promise of continual innovation.
Ready to take the first step? Take a Gemba walk. Not sure how to get started? See how Certainty Software can help.
You may also be interested in:
Kaizen for Continuous Improvement