More efficient businesses are more profitable. If employees are not wasting time on redundant, cumbersome, or complex processes, they’re better able to perform their jobs and ensure production targets are met. The challenge? Creating efficient operations isn’t a one-and-done process. Instead, companies need a continuous improvement approach that prioritizes ongoing evaluation to drive sustained success. Thankfully, there’s no need to build this type of process from scratch. Instead, they can leverage the Kaizen for Continuous Improvement framework.
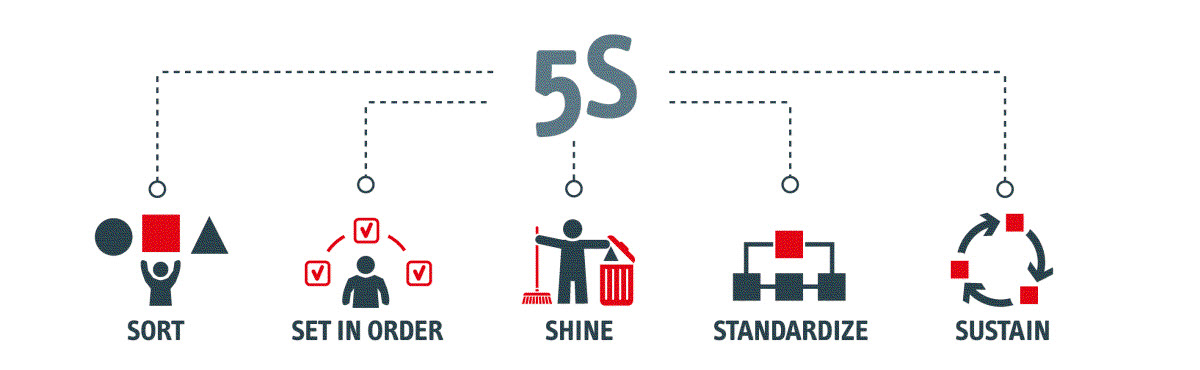
Here’s how it works.
What is the Kaizen for Continuous Improvement Model?
Kaizen is a Japanese word that combines the characters for “Change” (Kai) and “Good” (Zen), and is often translated to mean “Change is for Good.” First used in factories in both the US and Japan following World War II, Kaizen gained international recognition as part of the Toyota production system program, which saw the car manufacturer dramatically increase efficiency and output thanks to the application of Kaizen principles.
Also called “5S”, Kaizen defines five areas for continuous improvement:
Seiri
Seiri means to “sort out” and sees staff labeling items and tools as “necessary”, “important”, “not needed now” and “useless” — useless items should be immediately discarded.
Seition
Seition refers to organization — ensuring that necessary and important items are within reach and easy to access.
Seiso
Seiso means “shine”; clean and de-cluttered workspaces are both safer and more efficient.
Seiketsu-Seiketsu
This S is about standardization — creating a set of standardized work rules and policies for specific processes to ensure uniformity and increase quality.
Shitsuke
Finally, shitsuke is “self-discipline”, or the need for employees to respect policies, adhere to key processes and report any problems they encounter to help identify root causes.
A sixth “S”, safety has been added in recent years and gave rise to what’s known as Six Sigma or “6S Lean” methodology. Unlike the other five S’s, however, which are often performed separately, the safety component of lean manufacturing is designed to be all-encompassing as a way to reduce total risk.
Worth noting? Kaizen is all about small steps — incremental improvements that help team members better understand where issues exist to help improve the overall work environment and reduce total risk.
Why Does it Matter to Your Business?
The Kaizen approach to continuous improvement matters to your business because it provides a way to identify potential issues before they become larger problems.
Consider a critical workstation on your production line that hasn’t been performing up to par. Under a traditional approach to error correction, companies might simply look at output data and then take action — this might take the form of a staffing change, new metrics, or even an upgrade to current machinery. In some cases, the action works; in others, no improvement occurs.
Why? Because with this approach companies are effectively shooting in the dark. With 6S, meanwhile, it’s possible to pinpoint exactly where problems are occurring and then take steps that specifically address the problem. In our workstation example above, issues might be tied to the organization and cleanliness of the workspace combined with lacking standardization for performance. As a result, a few minor changes might be enough to address the issue and get production and business processes back on track.
The Kaizen process is also about more than simply changing specific operations — it’s about creating a company culture that focuses requires frontline staff buy-in to be effective over time. Ideally, the goal is to create a culture of continuous improvement that includes a focus on problem-solving, and quality control that uses small changes over time to deliver a substantive impact.
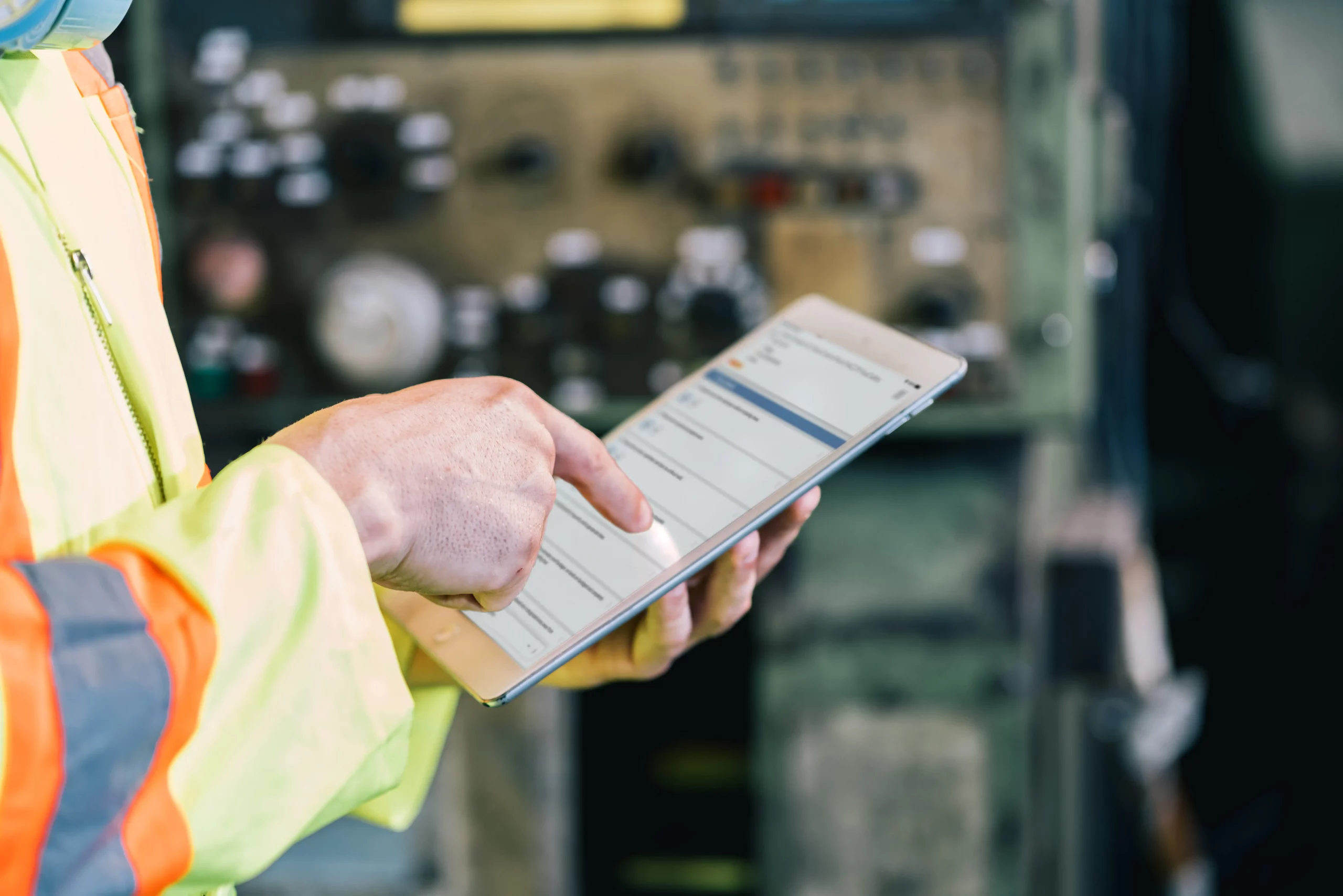
30+ Audit and inspection checklists free for download.
Where can Kaizen for Continuous Improvement Benefit Your Operations?
Kaizen for continuous improvement can benefit your operations in three key areas:
Reduced waste
Following the first three principles of Kaizen can help companies cut out unnecessary items at workstations and reduce the number of materials wasted during the production process, in turn helping to control overall spending.
Streamlined processes
Standardization of processes combined with clean workstations and easy access to necessary tools can streamline production line operations since staff can find what they need, when they need it, rather than searching for specific tools or sorting through the clutter to find key components.
Improved safety and morale
6S adoption creates a culture of shared safety that sees all employees looking out for each other to reduce total risk. And by working with employees to find and resolve key problems, staff morale increases — and they’re more likely to speak up about potential issues moving forward.
How do You Implement Kaizen for Continuous Improvement?
First up? The Gemba walk. Often called the “first step” of Kaizen, a Gemba walk sees managers and C-suite executives leaving their offices to see what happens on factory floors and production lines in person. The purpose of a Gemba walk isn’t to correct issues but rather to observe current operations and talk to the employees performing these operations. This helps establish a general sense of where things are working, where challenges exist, and where current processes simply can’t keep up. Using the data collected on a Gemba helps set the stage for broader Kaizen efforts and process improvements.
Successful implementation also requires in-depth audits and inspections of shop floors and production lines to identify areas of non-compliance and pinpoint safety issues. Robust quality assurance and inspection software can help streamline the process — tools that provide real-time visibility, consistent audit frameworks, and anytime, anywhere access makes it easier to get Kaizen efforts up and running.
When is the Right Time to Start with Kaizen for Continuous Improvement?
As soon as possible. While it’s often tempting to wait for the perfect time, there’s no such thing — you’ll inevitably encounter challenges with current operations, new projects, or other priorities that get in the way of Kaizen and 6S adoption.
Instead, consider Kaizen an addition to current processes rather than a replacement. While initial efforts require time and effort to get off the ground, once you’ve established solid frameworks you can leverage Kaizen components to both increase the efficiency of current operations and find new ways to boost performance.
Ready to embrace Kaizen for continuous improvement? Start with Certainty.
You may also be interested in:
The Gemba Walk: The First Step Toward Continuous Improvement