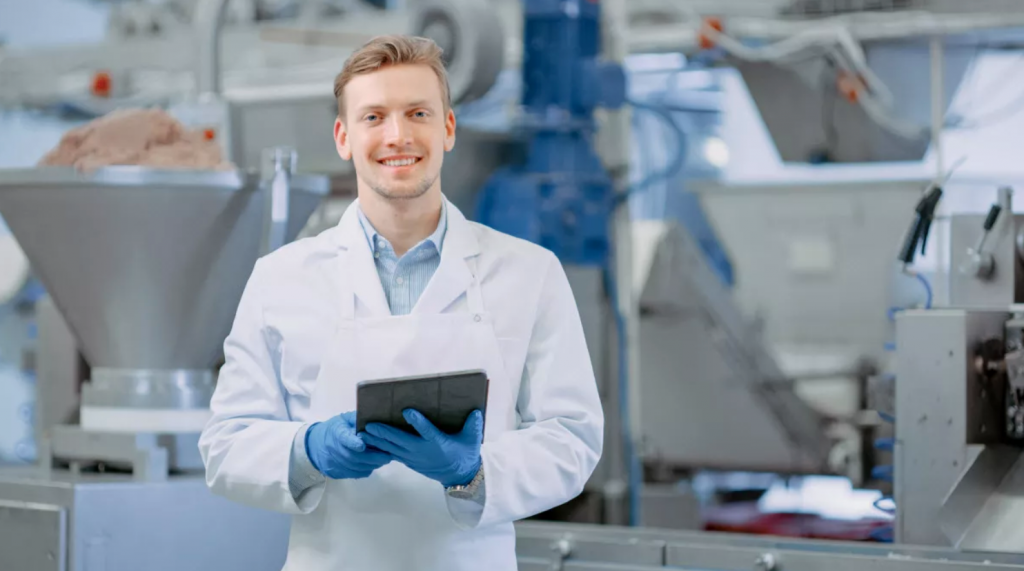
While price and positive experiences remain the leading factors in brands’ abilities to keep customers satisfied, quality also plays a critical role. According to research firm PWC, 52 percent of U.S. consumers would consider switching from one brand to another based on product quality. The result? It’s critical for companies to create policies and processes that allow them to effectively evaluate quality, identify potential problems and make meaningful changes — and it starts with quality assurance inspections.
Here’s what you need to know.
What is Quality Assurance?
Quality assurance (QA) refers to the set of policies and procedures that help manage and improve the development and production of a service or product. QA methodologies are implemented by businesses to ensure current processes are working as intended and identify areas where improvements are required.
Why do QA Inspections Matter?
Quality Assurance Inspections provide a way for companies to pinpoint issues in current processes that negatively impact product quality, in turn making it possible to address and eliminate these issues. These inspections have a significant overlap with 6S efforts that look to streamline operations by ensuring production line machinery is safely accessible from workstations and these workstations are clean and tidy.
Take the example of a workstation that lacks direct access to specific parts necessary for production. If staff must regularly leave their station to obtain these parts, this may lead to a gap in observability that in turn leads to failed QC checks. If this problem is identified during a QA inspection, however, it can be addressed and remediated at the point of origin.
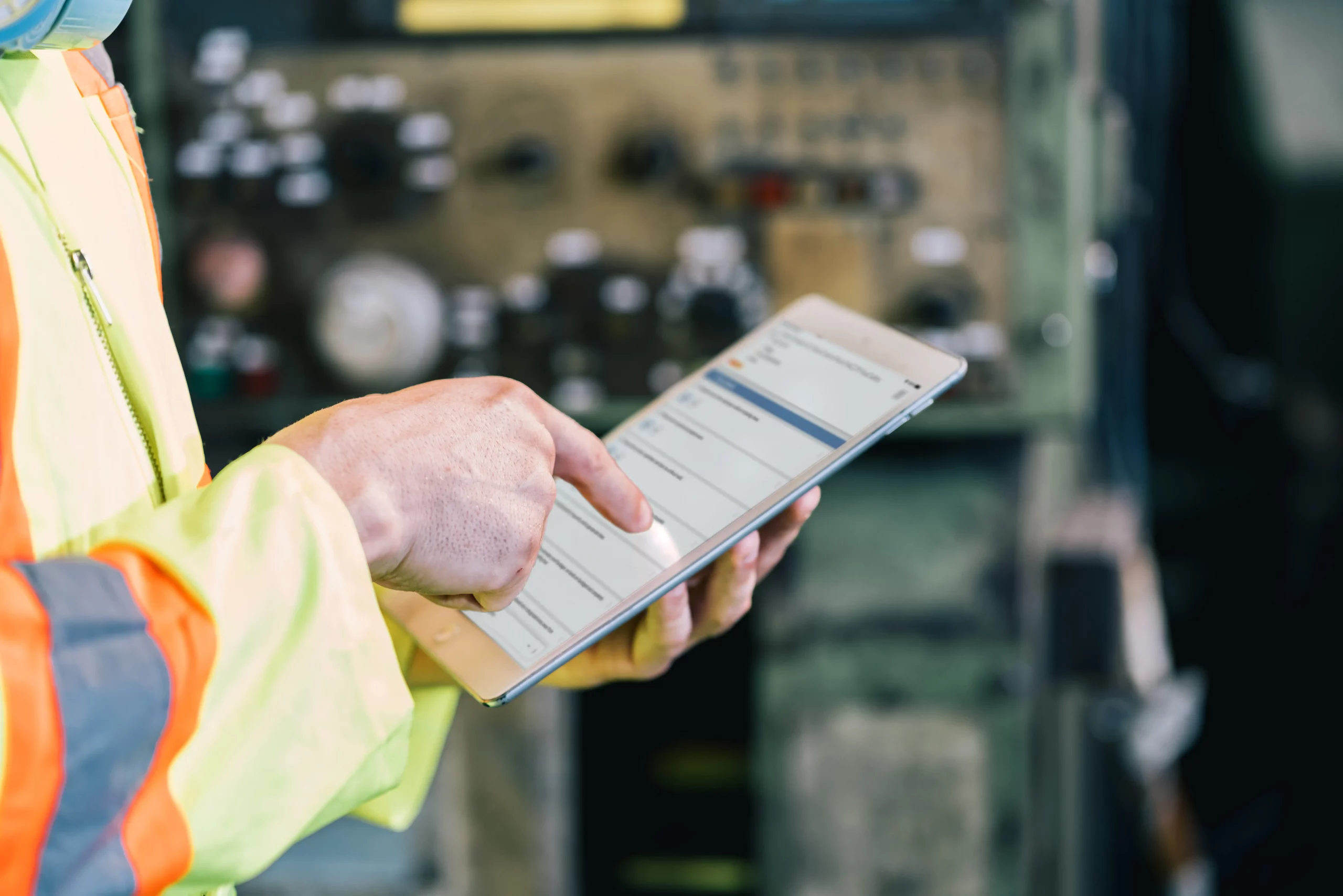
30+ Audit and inspection checklists free for download.
How-to: Conducting a Quality Assurance Inspection
So how do you conduct a quality assurance inspection? Three components are critical:
- Clear objectives
First, companies must define clear objectives for QA inspections: What manufacturing processes are inspectors evaluating, and what is the goal of these inspections? Are there standard operating procedures (SOPs) that apply to these processes?
- Stated specifications
Next, businesses must determine how they will measure the impact and efficacy of current processes: What metrics will be used to determine success or failure? Here, it’s often useful to create ideal quality standards that speak to how processes should perform and then compare observed data to these samples.
- Actionable results
Finally, organizations must identify actionable results for QA data. What corrective actions will be taken to avoid QA issues moving forward, and how will this impact be measured? It’s also important to conduct regular follow-ups after quality audits to ensure that any changes made have had the desired effect.
Armed with objectives, specifications, and results, QA inspectors can effectively evaluate processes, determine their impact on production, and (if necessary) make adjustments to improve overall output. Also worth noting? Documentation is key for all aspects of effective QA. By leveraging quality management systems (QMS) that include Quality Assurance Inspections checklists and templates and making it possible to centralize QA inspection reports and findings, businesses can better apply new policies at scale and reduce the risk of duplicate data that leads to additional time, effort, and cost.
You may also be interested in:
Kaizen For Continuous Improvement: How It Works
Improving Operational Quality: The Role Of Qualitative Risk Assessment