Table of contents
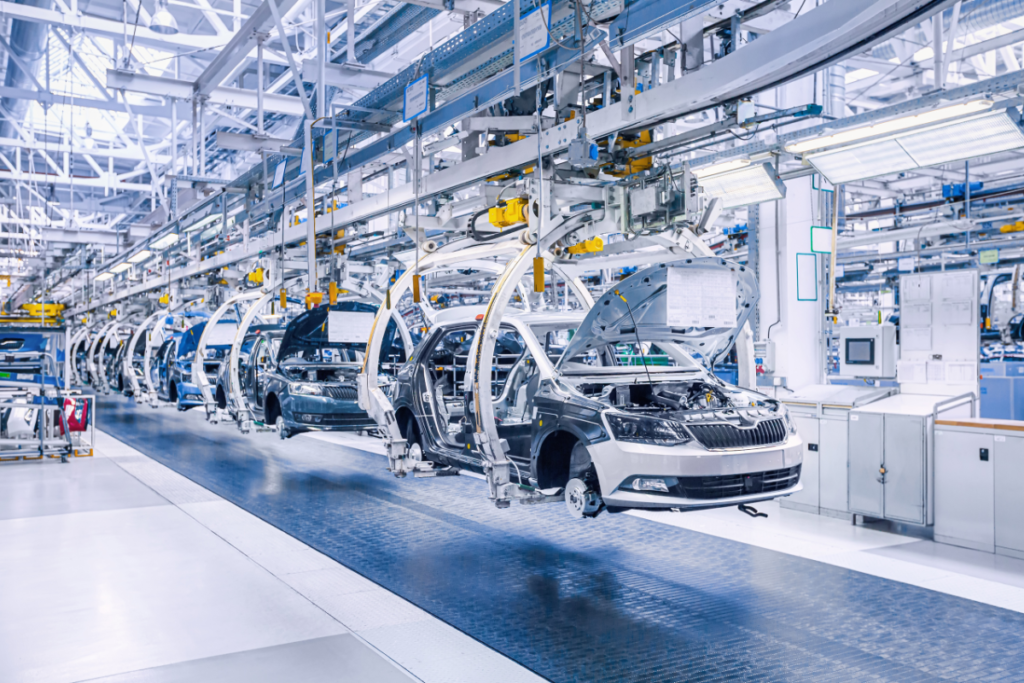
Did you know that human errors can have significant consequences across various industries? From manufacturing defects to service errors, these mistakes can result in quality issues, safety hazards, and financial losses. However, there’s a remarkable technique called Poka Yoke, derived from the Japanese term meaning “mistake-proofing.”
In this comprehensive guide, we’ll explore the origins, principles, and practical applications of Poka Yoke, and uncover how it can revolutionize industries by preventing errors and ensuring excellence.
What is Poka Yoke?
Poka Yoke, a concept originating from Japan, is a methodology designed to prevent human errors in the production process. Coined by Shigeo Shingo, an industrial engineer who revolutionized quality control practices, Poka Yoke is an integral part of the Toyota Production System and lean manufacturing philosophy. The primary objective of this concept is to create foolproof systems that make errors virtually impossible and ensure quality at every step.
Poka Yoke focuses on two key objectives: error prevention and quality improvement. By implementing its techniques, organizations aim to identify and eliminate potential errors in their processes. Additionally, Poka Yoke contributes to quality improvement by enabling the production of defect-free products or services. Furthermore, it increases efficiency by reducing the time and resources wasted on reworking or rectifying errors.
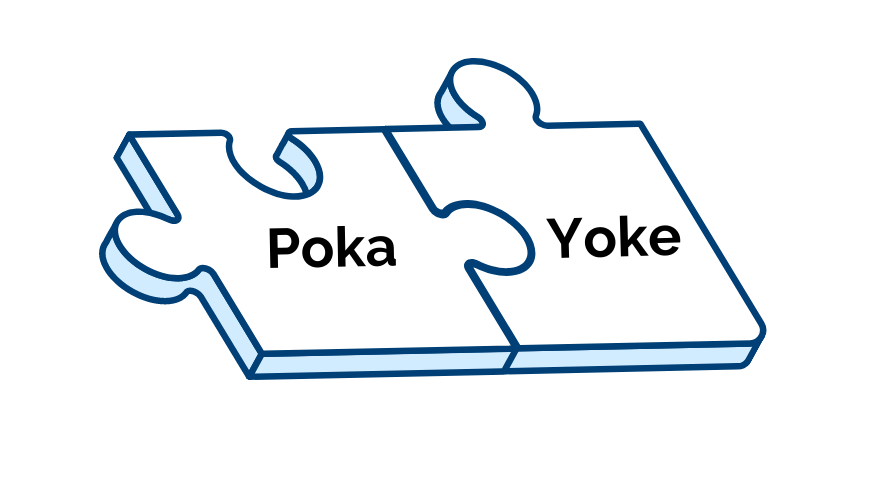
How Does Poka Yoke Work?
Poka Yoke relies on the principles of mistake-proofing and foolproofing. Mistake-proofing involves implementing mechanisms that prevent errors from occurring or immediately detect them. These mechanisms can take various forms, such as visual cues, physical devices, or checklists. The goal is to create a system that guides the user toward the correct action and alerts them if an error is about to occur.
Foolproofing takes mistake-proofing a step further by anticipating human behavior and designing processes that make errors nearly impossible, even for individuals unfamiliar with the system. It involves incorporating mechanisms that force the correct sequence of actions or prevent further progress until certain conditions are met. By doing so, foolproofing minimizes the likelihood of errors and ensures the desired outcome.
Different types of Poka Yoke techniques and devices exist, such as contact methods, fixed-value methods, and physical attribute methods. Contact methods use physical contact to detect errors, such as sensors that confirm the presence or absence of a specific component. Fixed-value methods involve setting predetermined values to ensure correctness, such as using templates or jigs to guide assembly processes. Physical attribute methods use the physical properties of objects to prevent errors, such as using unique shapes or sizes to ensure proper alignment.
Examples of Poka Yoke in Action
Poka Yoke techniques find practical applications in everyday business situations, helping organizations prevent errors, improve quality, and streamline their operations. Let’s explore two relevant examples:
Automotive Assembly:
In the automotive manufacturing industry, precision and accuracy are paramount to ensure safe and reliable vehicles. Poka Yoke is extensively utilized to eliminate assembly errors and maintain high-quality standards. For instance, automotive assembly lines incorporate specialized fixtures and jigs that only allow components to be installed in the correct orientation and sequence. These fixtures may include sensors or limit switches that verify the proper alignment or insertion of parts before the assembly process can proceed. By implementing such error-proofing measures, automotive manufacturers minimize the risk of incorrect installations, ensuring the integrity and functionality of the final product.
Assembly Line Manufacturing:
Consider a complex electronic device manufacturing process that involves multiple components. Poka Yoke can be applied by incorporating visual cues, such as color-coded indicators or unique shapes, on components that require specific assembly steps. This ensures that operators correctly identify and install each component in the designated location, reducing the likelihood of errors and improving overall efficiency. Furthermore, automated Poka Yoke devices, such as sensors or scanners, can be integrated into assembly lines to verify the presence or alignment of critical parts at various stages of the process. These automated checks act as safeguards, detecting errors in real time and preventing defective products from progressing further down the line, thereby reducing rework and minimizing waste.
Benefits of Implementing Poka Yoke
Implementing Poka Yoke offers several benefits to organizations:
- Increased Productivity: By preventing errors and reducing rework, Poka Yoke improves overall productivity. Workers can focus on value-added tasks instead of rectifying mistakes, leading to streamlined processes and faster production cycles.
- Cost Reduction: Poka Yoke minimizes the costs associated with errors, such as rework, scrap, or customer complaints. By preventing errors at the source, organizations save time, materials, and resources, resulting in substantial cost savings.
- Enhanced Customer Satisfaction: Poka Yoke ensures that products and services consistently meet customer requirements and expectations. By reducing defects and errors, organizations can deliver high-quality products that satisfy customer needs, ultimately enhancing customer satisfaction and loyalty.
- Improved Employee Morale: When employees work in error-free environments, their morale and job satisfaction increase. Poka Yoke empowers employees by providing them with the tools and systems to perform their work accurately, which boosts confidence and job engagement.
A systematic approach to implementing Poka Yoke is crucial for success. Organizations must focus on understanding their processes, identifying error-prone areas, and designing appropriate Poka Yoke techniques. It is essential to involve employees throughout the process, providing training, and fostering a culture of continuous improvement.
Implementing Poka Yoke in Your Organization
Implementing Poka Yoke in your organization requires a thoughtful and systematic approach. It is not simply about introducing a few error prevention measures but rather cultivating a culture of continuous improvement and quality assurance. Here are key steps and considerations to guide you through the implementation process:
1. Identify Error-Prone Areas and Root Causes
To effectively implement Poka Yoke, start by analyzing your processes to identify areas where errors commonly occur. Engage with employees and gather their insights and experiences to gain a comprehensive understanding of potential pitfalls. This step involves conducting thorough root-cause analyses to determine the underlying reasons for errors. By addressing root causes, you can implement targeted solutions that have a lasting impact on error prevention.
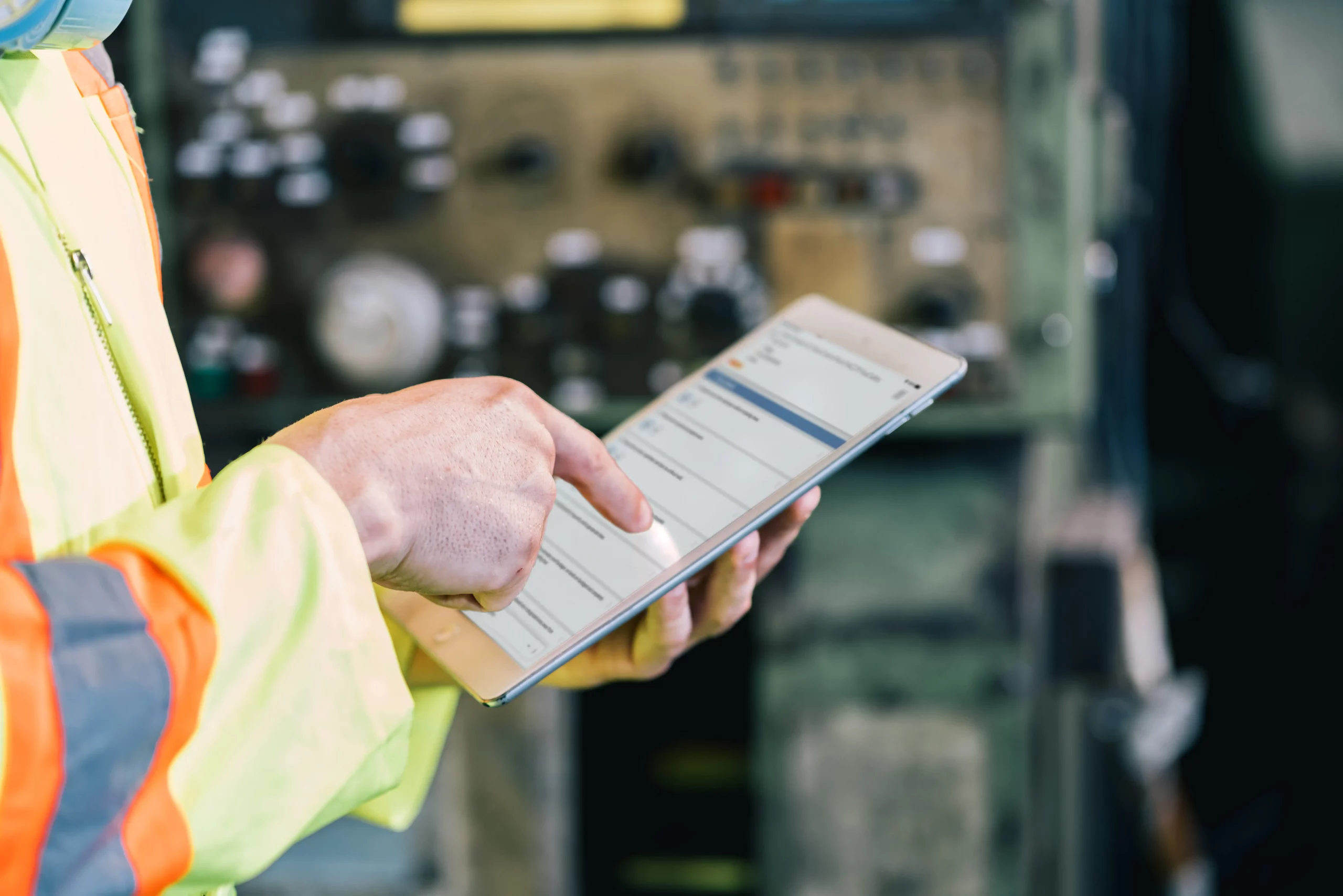
30+ Audit and inspection checklists free for download.
2. Design Error Prevention Measures
Once you have identified the error-prone areas and their root causes, it’s time to design and implement error prevention measures. Consider a range of Poka Yoke techniques and devices suitable for your specific context. These can include visual cues, checklists, sensors, automation, and more. The key is to develop measures that are intuitive, user-friendly, and seamlessly integrated into existing processes.
3. Involve Employees in the Process
Employees are the driving force behind the successful Poka Yoke implementation. Their experience and insights are invaluable for identifying potential errors and designing effective preventive measures. Actively involve employees in the design and implementation process, seeking their input and feedback. This not only enhances the quality of error prevention solutions but also fosters a sense of ownership and engagement among employees.
4. Provide Comprehensive Training and Education
To ensure successful adoption, provide comprehensive training and education to all employees involved in the process. This includes training on the purpose and benefits of Poka Yoke, as well as the specific techniques and devices being implemented. Employees should understand how these measures contribute to error prevention, quality improvement, and the overall success of the organization. Ongoing training and reinforcement are essential to maintain a high level of awareness and adherence to Poka Yoke principles.
5. Foster a Culture of Continuous Improvement
Poka Yoke implementation is not a one-time project but an ongoing journey toward continuous improvement. Encourage employees to report errors, suggest improvements, and actively participate in the refinement of error prevention measures. Establish feedback channels, such as suggestion boxes or regular team meetings, where employees can voice their observations and concerns. Regularly review and evaluate the effectiveness of implemented Poka Yoke measures, and be open to making adjustments as necessary. This culture of continuous improvement will foster innovation and ensure that error prevention remains a top priority within your organization.
6. Overcome Challenges and Considerations
Implementing may come with certain challenges and considerations. Resistance to change, lack of employee buy-in, or resource constraints can hinder the successful implementation of error prevention measures. It is essential to address these challenges proactively by fostering open communication, providing sufficient training and support, and clearly articulating the benefits of Poka Yoke. Additionally, ensure that your organization has allocated the necessary resources, both in terms of time and budget, to implement and sustain these initiatives.
7. Share Best Practices and Success Stories
As you embark on your Poka Yoke journey, share best practices and success stories within your organization. Highlight examples of how Poka Yoke has led to error reduction, improved quality, and enhanced productivity. Recognize and celebrate employees who actively contribute to the success of error prevention initiatives. This sharing of experiences and successes will inspire others and further embed these principles into your organizational culture.
Supporting Poka Yoke With Certainty Software
As industries evolve, so does the application of Poka Yoke. From manufacturing to healthcare, the benefits of error prevention and quality assurance are universal. With the support of comprehensive tools like Certainty Software, organizations can streamline their Poka Yoke implementation, simplify error prevention processes, and achieve higher levels of operational excellence.
With Certainty Software, organizations can easily create customized checklists and forms tailored to their specific Poka Yoke requirements. These checklists can include built-in validation checks and automated alerts, ensuring that critical steps are followed and errors are prevented. Certainty Software also enables real-time data capture, allowing organizations to monitor and analyze quality metrics to identify areas for improvement and take corrective actions promptly.
Furthermore, Certainty Software provides comprehensive reporting and analytics capabilities, empowering organizations to gain valuable insights into their Poka Yoke initiatives. Through detailed reports and dashboards, stakeholders can track performance, measure the effectiveness of error prevention measures, and make data-driven decisions to enhance quality control. If you’d like to learn more about what Certainty Software can provide for your quality improvement plans, schedule a free demo with us.
You might also be interested in: