Table of contents
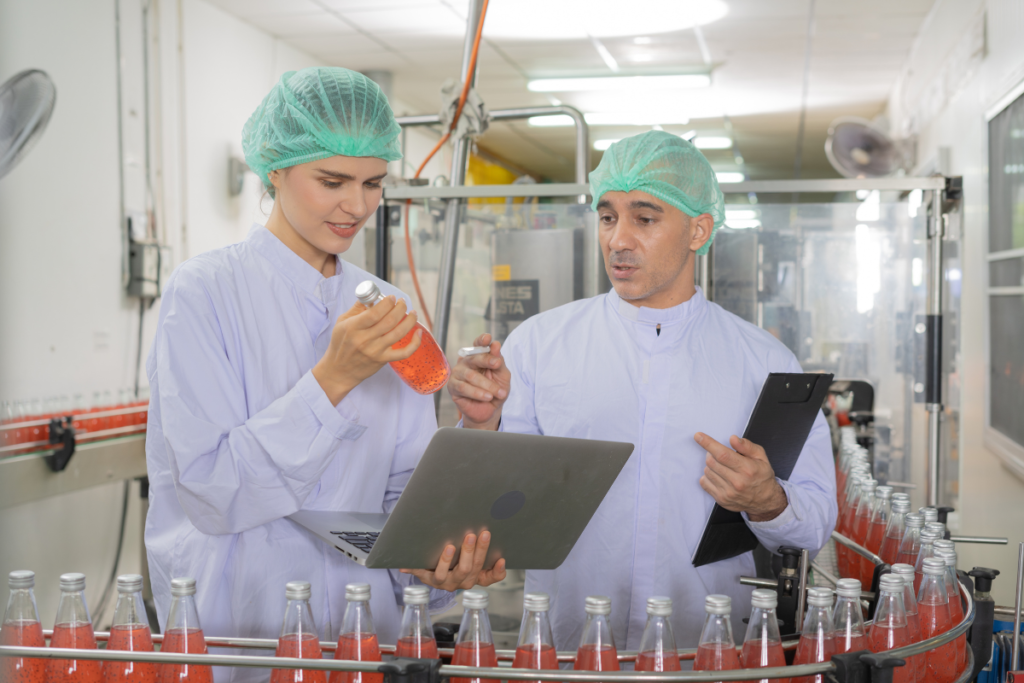
The British Retail Consortium (BRC) is well-known to those working in the food, packaging, or storage and distribution industries. The BRC, a well-known trade group that represents UK retailers and their suppliers, is an industry leader in terms of compliance, quality, and safety for a variety of supply chain components.
Understanding BRC audits, however, goes beyond simply adhering to industry norms to guarantee the greatest levels of quality and customer satisfaction. In fact, because they value dependability and honesty in their business relationships, many discerning retailers and buyers look for suppliers who have passed BRC audits.
In this article, we’re going to examine what BRC audits comprise, why they’re important, and how to handle them skillfully to improve your company’s performance and reputation.
What is a BRC Audit?
An objective evaluation of your company’s compliance with a particular BRC standard is a BRC audit. A BRC audit’s goal is to confirm that your systems, processes/process controls, and products adhere to the standards and that you have put in place reliable controls to guarantee performance.
There are various BRC standards for various supply chain segments, including:
BRC Food
The BRC Food standard focuses on food quality and safety management for food manufacturers. It’s based on guidelines like Good Manufacturing Practice (GMP), Hazard Analysis and Critical Control Point (HACCP), and industry best practices.
Retailers, producers, regulators, and consumers all throughout the world recognize and recognize BRC standards. Additionally, they are compared to the Global Food Safety Initiative (GFSI), a project led by the food industry with the goal of unifying food safety standards around the world.
BRC Packaging
For packaging manufacturers, the BRC Packaging standard addresses hygiene, safety, and quality control. This standard encompasses all packaging materials, from paper and plastic to metal, glass, and wood.
BRC Storage & Distribution
This standard covers hygiene, safety, and quality management for storage, distribution, transportation, and logistics services, applying to both food and non-food products.
BRC standards are recognized worldwide by retailers, regulators, and consumers. They’re also aligned with the Global Food Safety Initiative (GFSI), a global effort to harmonize food safety standards.
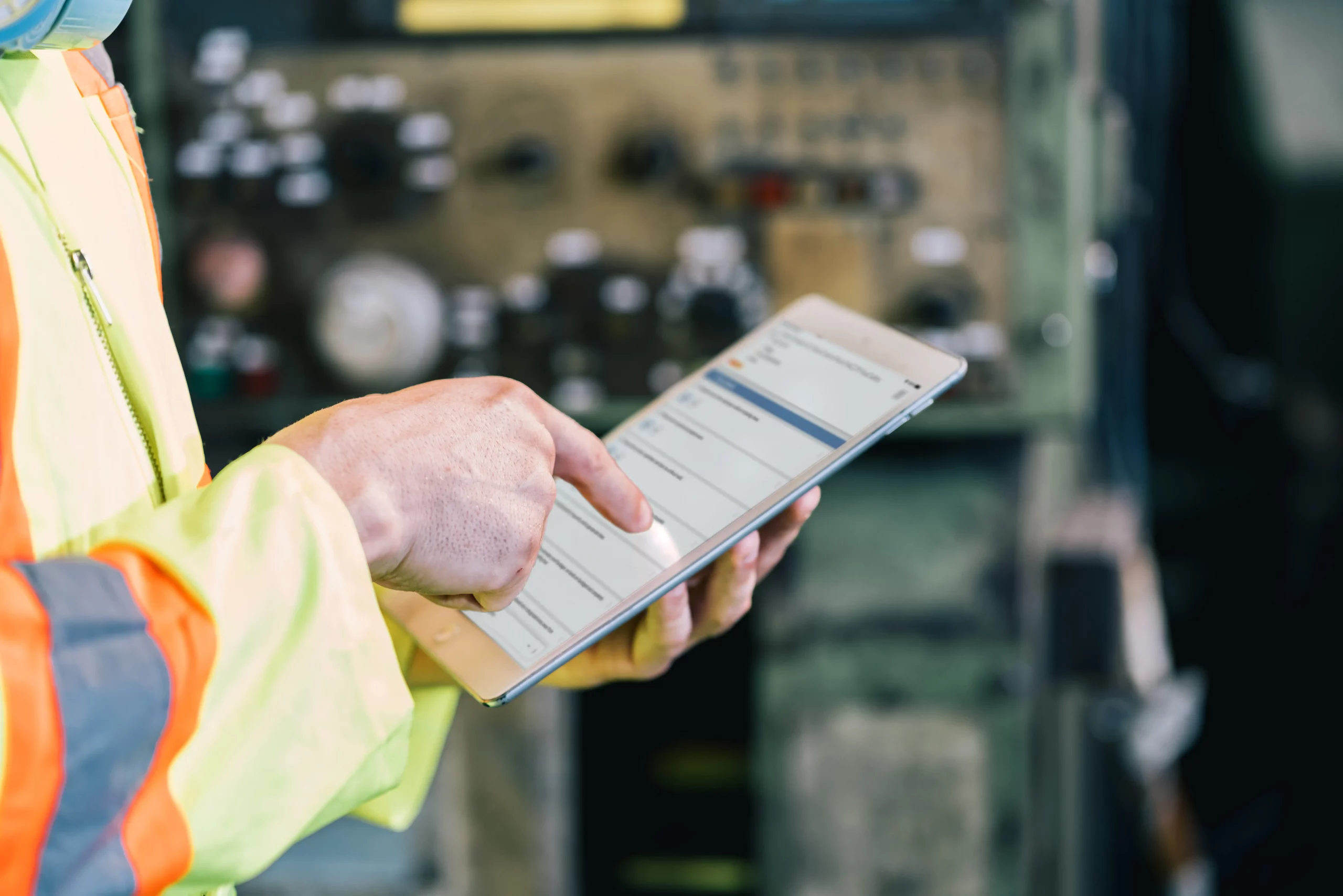
30+ Audit and inspection checklists free for download.
Why is a BRC Audit Important?
Retailers, regulatory agencies, and consumers all recognize the value of BRC standards. Not only are these standards well-known, but they also support the Global Food Safety Initiative (GFSI), a global initiative aiming at harmonizing food safety procedures.
In today’s very competitive and complicated business climate, adherence to industry-specific regulations and standards is not only necessary by law but by a strategic imperative. The benefits of adopting BRC principles are numerous, enabling your firm to:
Elevate Credibility & Reputation
Accreditation by the BRC is a visible sign of your unshakable dedication to excellence, exceeding both stakeholder and customer expectations. It also gives you a distinct advantage over your rivals, opening you fresh possibilities for development and expansion.
Mitigate Risks & Costs
BRC audits serve as a proactive line of defense, spotting possible risks and problems in your products, processes, and systems before they develop into severe crises. You can avoid expensive recalls, fines, legal entanglements, and brand damage by taking this proactive strategy. You strengthen your defenses against unforeseen events by putting corrective and preventive actions into place.
Enhance Efficiency & Performance
BRC audits act as a catalyst for operational excellence by optimizing your operations, cutting waste, increasing efficiency, decreasing mistakes, and guaranteeing consistent product quality. You may reach higher quality standards while maximizing resource usage by following best practices and fostering a culture of continuous improvement.
Did you Know?
A BRCGS survey found that obtaining BRC certification had a positive impact on organizations. The following benefits were stated by respondents:
- Increased competitiveness (70%).
- Enhanced operational efficiency (69%).
- Increased sales (55%).
3 Steps to Conducting a Successful BRC Audit
It takes careful planning, implementation, reporting, and follow-up for a BRC audit to be successful. The four key steps to performing a successful BRC audit are as follows:
Step 1: Preparation Phase
Successful BRC audit execution necessitates detailed preparation, exact execution, thorough reporting, and proactive follow-up. Here, we outline the four essential steps to help you conduct a successful BRC audit:
Select Your Audit Team
Your audit team should be made up of auditors who have in-depth knowledge, competence, and experience in the particular BRC standard, industrial area, and company processes that will be scrutinized. Their objectivity in delivering a fair review is equally crucial. Audit procedures including observation, sampling, testing, verification, assessment, and reporting should be thoroughly understood by auditors.
Gathering Documentation
Gather a broad range of documents that attest to your compliance with the BRC standard. Policies, procedures, records, manuals, specifications, plans, reports, certificates, licenses, permits, contracts, agreements, and any other relevant records should be included in these documents. The most important thing is to make sure your paperwork is accurate, thorough, consistent, conveniently available, and traceable.
Defining Audit Scope & Objectives
Clearly define the audit’s objectives and scope. The target audience, products, systems, sites, and divisions that will be inspected should all be specified in the audit scope, which should also define the audit’s boundaries and coverage area. The audit objectives, on the other hand, describe what you hope to accomplish with the audit, be it confirming compliance, identifying gaps, gauging performance, or suggesting improvements. These goals must be in line with the BRC standard, your corporate goals, and client requirements.
Communicating with the Relevant Parties
Maintain open lines of contact with all key participants in the audit process. This includes the auditee (the company being audited), the auditor, the certification body (the organization in charge of awarding BRC certification), and any additional stakeholders (such as customers, suppliers, representatives of the government, or employees) who might be involved in or affected by the audit. Make sure that the audit plan, which includes the agenda, methodology, standards, and expectations, is openly shared. Define each party’s roles and responsibilities as well as the standards and practices for the audit as well and the security and confidentiality policies that govern data collecting.
Step 2: Audit Execution Phase
The pre-audit briefing, documentation review, on-site conditions inspection, and evidence evaluation are all part of the audit execution phase.
Pre-Audit Briefing
Hold a pre-audit briefing with the auditee and the auditor before starting the audit. This briefing’s goals are to build rapport and confidence, validate the audit’s scope and goals, go over the audit plan, and answer any queries or worries.
Document Review
Conduct a thorough examination of the auditee’s records. Here, it’s important to make sure that the paperwork follows the BRC standard, accurately depicts the business’s operations and results, and offers verifiable proof of compliance. The document evaluation may also reveal discrepancies or omissions that call for additional research or explanation.
On-Site Inspection
The process of witnessing and evaluating the physical circumstances and operations at the auditee’s premises is called an on-site inspection. The goal of the on-site inspection is to confirm that the conditions and operations are by the paperwork, that they adhere to the BRC standard, and that they guarantee the products’ safety and quality. The on-site examination could involve:
- Personal Hygiene and Sanitation
- Product Handling and Storage
- Documentation and Records
- Personnel Practices
- Equipment and Machinery
- Quality Control Procedures
- Emergency Preparedness
- Training and Competence
- Evaluating the Evidence
Step 3: Reporting and Follow-up Phase
Documenting the audit findings, performing a root cause analysis, creating a corrective action plan, offering suggestions for continuous improvement, disseminating and reviewing the audit results, and carrying out post-audit activities are all part of the reporting and follow-up phase.
Audit Findings Documentation
Reporting the findings of the audit in the documentation of the findings is done. The audit scope, objectives, methodology, evidence, evaluation, audit NCs, observations, audit conclusion, and recommendation are all included, along with any other pertinent data. The documentation of the audit findings must be objective, accurate, complete, accurate, and clear.
Root Cause Analysis
The process of locating and examining the underlying causes of the NCs is known as root cause analysis. By addressing the root cause of the issue rather than just the symptom, the root cause analysis aims to avoid the NCs from recurring. The 5 Whys, fishbone diagram, Pareto chart, SWOT analysis, and other tools and methodologies may be used during the root cause analysis.
Corrective Action Plan
The steps that will be taken to address the NCs and stop them from happening again are outlined in the corrective action plan. The description of the NCs, the underlying causes, the corrective measures, the accountable parties, the intended completion dates, and the verification techniques are all included. The corrective action plan needs to be time-bound, relevant, practical, explicit, measurable, and doable.
Continuous Improvement Recommendations
The proposals for continuous improvement are ideas that go above and beyond what is required by the standard to enhance the operation’s performance and compliance. Best practices, standards, innovations, or chances for improvement might be among them. The suggestions for ongoing improvement should be supported by facts, information, analysis, or feedback.
Leveraging Technology for Your Next BRC Audit
Technology can help you streamline and enhance your BRC audit process by automating, simplifying, standardizing, and optimizing various aspects of the internal audit, such as documentation, data collection, reporting, communication, and data analysis.
At Certainty Software, we open new windows of audit and inspection opportunities. We do this by giving you the power to easily create, manage, and report on your audits and inspections. This is done by offering customizable checklists, mobile data collection, remote auditing, integrated media, automated reporting, and data analysis. Our goal is to enable you to improve your compliance, reduce your risks, enhance your performance, and increase your customer satisfaction.
Want to learn more about how Certainty Software can integrate with your BRC audit systems or other food safety plans? Book a no-obligation demo with us here.
You might also be interested in: