Table of contents
- What is risk-based-thinking (RBT)?
- Why risk-based thinking is significant in QMS
- The signs of poor risk-based thinking in enterprises
- ISO 9001:2015’s relationship to risk-based thinking
- Global quality assurance regulations and risk-based thinking
- Steps for implementing risk-based thinking
- Emerging trends in RBT
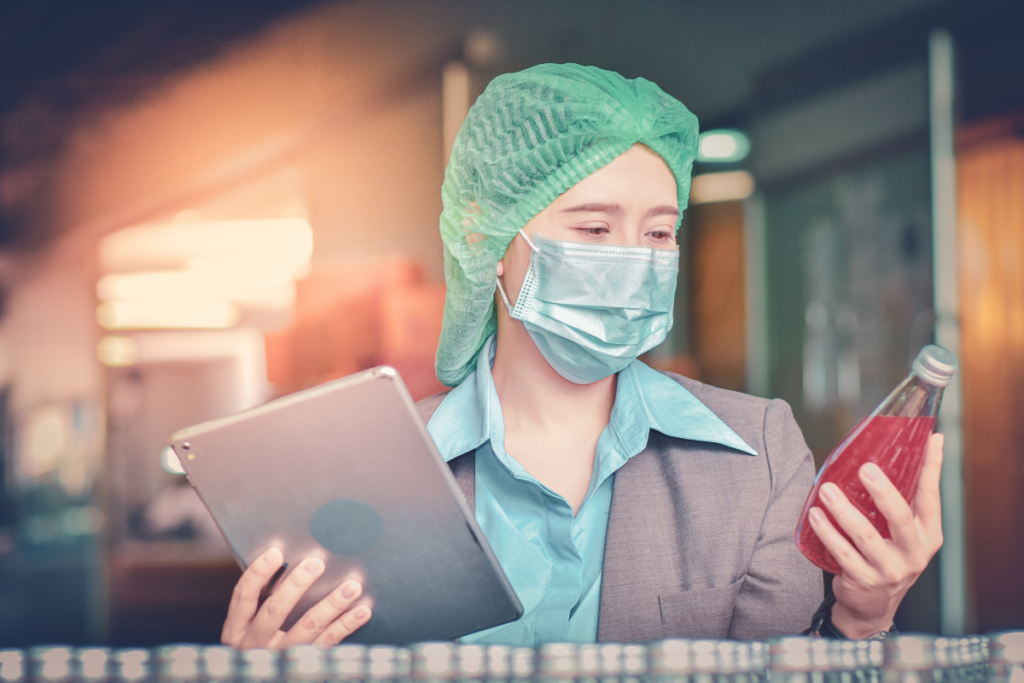
The quality of products and services is crucial for business success in today’s competitive market. For leaders in quality assurance, maintaining high standards is essential for operational excellence throughout the enterprise. The shifting landscape of global markets requires not only compliance with established standards but also strategic foresight to proactively identify and manage risks.
This blog post will delve into how Risk-Based Thinking (RBT) aligns with ISO 9001:2015 requirements and other global quality assurance standards. We will explore the implementation of RBT and highlight its significant benefits for organizations striving for excellence and sustainability.
What is Risk-Based Thinking?
Risk-Based Thinking (RBT) is the systematic approach to identifying, assessing, and mitigating risks within the QMS framework. Unlike traditional methods that respond to issues post-occurrence, RBT emphasizes foresight and preventive action, embedding risk awareness into all organizational processes. The RBT approach is crucial for maintaining high standards of quality, as well as ensuring that potential problems are addressed before they escalate into significant issues.
The Significance of Risk-Based Thinking in Quality Management
The integration of RBT within QMS ensures that potential issues are addressed before they escalate, fostering a culture of continuous vigilance and improvement. As a proactive, rather than reactive approach, Risk-Based Thinking continues to be significant in today’s highly reactive supply chain.
A key part of the overall improvement and maintenance of high-quality standards, RBT delivers:
- Enhanced Decision-Making
- Continuous Improvement
- Compliance with Standards and Regulations
- Organizational Resilience
- Customer Satisfaction
- Strategic Competitive Advantage
- Resource Optimization
Historical Context
The journey of quality assurance has evolved significantly over the decades. From the early days of simple inspection methods to the adoption of Total Quality Management (TQM) and Six Sigma, the field has continuously advanced. The introduction of the risk-based approach to thinking in ISO 9001:2015 marked a significant milestone, reflecting the industry’s shift towards a more anticipatory and strategic approach to quality management.
Signs of Poor Quality Assurance Risk-Based Thinking Management
Effective Risk-Based Thinking (RBT) management is crucial for maintaining high standards of quality and compliance in any organization. However, when RBT management is poorly implemented, several signs can indicate underlying issues that need to be addressed. Identifying these signs early can help organizations take corrective actions and improve their quality management systems.
Frequent Quality Issues:
One of the most apparent signs of poor RBT management is the recurrence of defects and non-conformances in products or services. If an organization is constantly dealing with quality issues, it suggests that potential risks are not being adequately identified or mitigated.
High Rate of Product Recalls
Many product recalls indicate a failure to manage risks effectively. Recalls can be costly and damaging to a company’s reputation, highlighting the importance of robust risk management practices.
Regulatory Non-Compliance
Failure to meet regulatory standards and thus receive penalties or warnings from regulatory bodies is a clear sign of poor RBT management.
Increased Customer Complaints
A surge in customer complaints often points to gaps in identifying and addressing quality-related risks.
High Internal Failure Costs
Significant costs associated with internal failures, such as rework and scrap, reflect poor risk management. These costs can erode profit margins and indicate that processes are not being effectively controlled.
Low Employee Engagement
Employees may become disengaged or demotivated if they feel that risks are not adequately managed or if they are constantly dealing with quality issues.
Ineffective Corrective Actions
Repeated occurrences of the same issues suggest that corrective actions are not addressing the root causes.
Lack of Continuous Improvement
The absence of ongoing improvement initiatives and stagnation in quality performance is another sign of poor RBT management. Continuous improvement is essential for adapting to changes and maintaining high standards.
Poor Supplier Quality
Frequent issues with supplier quality indicate a failure to manage supply chain risks effectively. Reliable suppliers are critical to maintaining product quality, and poor management of supplier risks can lead to significant quality problems.
Inadequate Documentation
A lack of thorough documentation for risk assessments, mitigation plans, and quality processes is a clear sign of poor RBT management. Proper documentation is essential for tracking progress, ensuring accountability, and maintaining compliance with standards.
ISO 9001: 2015 and Risk-Based Thinking
ISO 9001:2015 is the latest iteration of the globally recognized standard for quality management systems. The standard emphasizes a process-oriented approach, integrating various elements such as customer focus, leadership, engagement of people, process approach, improvement, evidence-based decision-making, and relationship management. Its purpose is to ensure that quality management is not a standalone function but an integral part of the entire organizational ecosystem.
Key Principles and Structure
How does ISO 9001:2015’s structure support the integration of Risk-Based Thinking? Several key principles within the standard collectively ensure effective quality management through an RBT approach. Here is a summary of those principles:
- Understanding and meeting customer requirements is paramount.
- Strong leadership is essential for establishing unity of purpose and direction.
- Involving competent, empowered, and engaged people enhances the organization’s capability.
- Managing activities as processes ensures consistent and predictable results.
- Continuous improvement is a permanent objective of the organization.
- Decisions based on the analysis of data and information are more likely to produce desired results.
- Managing relationships with interested parties (such as suppliers) optimizes performance.
How is Risk-Based Thinking Integrated in ISO 9001:2015?
RBT is embedded throughout ISO 9001:2015, with specific emphasis in Clause 6.1, which mandates organizations to identify and address risks and opportunities that could affect the QMS. Clause 6.1 specifically ensures that risk management is a continuous and integral part of the QMS processes:
“When planning for the quality management system, the organization shall consider the issues referred to in 4.1 and the requirements referred to in 4.2 and determine the risks and opportunities that need to be addressed.”
Clause 6.1.2 follows suit requiring an RBT approach to quality management:
“The organization shall plan:
a) actions to address these risks and opportunities
b) how to:
- integrate and implement the actions into its quality management system processes
- evaluate the effectiveness of these actions”
Download our free Quality Management System (QMS) Audit Checklist to ensure your processes align with standards such as ISO 9001:2015
Global Quality Assurance Regulations and Risk-Based Thinking
Various global regulations underscore the importance of RBT, aligning closely with ISO 9001:2015. For instance, the FDA’s quality system regulation (QSR) mandates risk management in medical device manufacturing, ensuring patient safety and product efficacy. These regulations highlight the critical role of RBT in maintaining compliance and safeguarding public health.
Industry-Specific Applications
Automotive: In the automotive industry, IATF 16949 is the global standard that incorporates RBT to enhance supplier quality and manage supply chain risks. This standard aligns with ISO 9001:2015 but includes additional requirements specific to the automotive sector.
Aerospace: The AS9100 standard for the aerospace industry integrates RBT to ensure high reliability and safety in aviation products. This standard extends the principles of ISO 9001:2015 with sector-specific requirements to address the unique challenges of aerospace manufacturing.
Healthcare: In the healthcare sector, various regulations emphasize the importance of RBT. The FDA’s QSR mandates risk management practices for medical devices, while the International Organization for Standardization (ISO) 13485 standard specifies requirements for a quality management system that demonstrates the ability to provide medical devices and related services that consistently meet customer and regulatory requirements.
Pharmaceutical: The International Conference on Harmonisation (ICH) Q9 guideline provides a framework for Quality Risk Management (QRM) in the pharmaceutical industry. This guideline emphasizes a systematic process for the assessment, control, communication, and review of risks to the quality of the drug product.
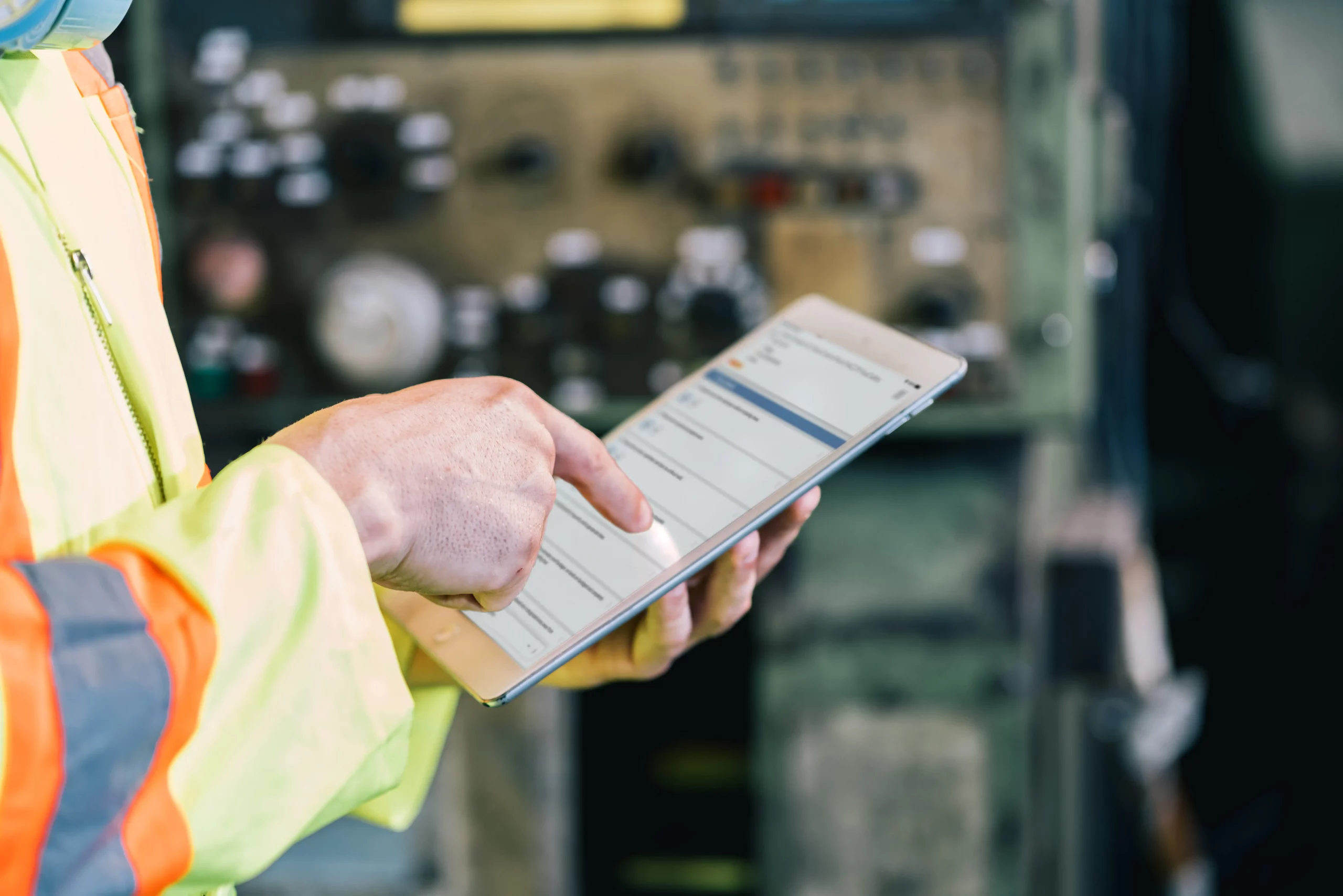
30+ Audit and inspection checklists free for download.
Practical Steps to Implement Risk-Based Thinking
1. Risk Identification
Utilize tools such as FMEA, SWOT analysis, and brainstorming sessions to identify potential risks within the QMS. Encourage cross-functional teams to contribute, ensuring a comprehensive risk identification process. Collaboration in this first initial step ensures that all potential risks are identified and addressed.
2. Risk Assessment
Following your risk identification, start to evaluate risks based on their severity, likelihood, and impact on the organization. Use risk matrices and other assessment tools to prioritize risks effectively. Following this step in implementation confirms that the most significant risks are addressed first, minimizing their potential impact on the organization.
3. Risk Mitigation
Next, develop and implement your organization’s risk mitigation plans, assigning responsibilities and setting timelines for action. Regularly monitor the effectiveness of these plans, making adjustments as necessary.
4. Continuous Improvement
Finally, and most importantly, foster a culture of continuous improvement by integrating RBT into all aspects of the QMS. Encourage feedback, conduct regular audits, and stay updated with industry best practices.
Emerging Trends in RBT
The landscape of Risk-Based Thinking (RBT) is rapidly evolving, bringing transformative changes to how organizations manage quality and risk. Here are some key trends that are shaping the future:
AI and Machine Learning
AI and machine learning are game-changers in risk management. These technologies analyze vast amounts of data to uncover patterns and predict potential risks that might otherwise go unnoticed. Imagine AI predicting equipment failures before they happen, saving time and reducing costs. Organizations using AI are not just reacting to risks—they’re staying a step ahead.
Blockchain
Blockchain technology is revolutionizing supply chain management by ensuring transparency and security. Beyond financial transactions, blockchain creates a tamper-proof record of every component and step in a product’s lifecycle. For example, in the pharmaceutical industry, blockchain can track drugs from manufacturer to consumer, ensuring authenticity and regulatory compliance. This technology shifts trust from reputation to data, fundamentally transforming risk management in supply chains.
Sustainability
Sustainability is becoming a core business strategy, not just a regulatory requirement. Companies are integrating RBT with sustainability initiatives to manage environmental risks and create value. For instance, using life cycle assessments, businesses can innovate in product design to reduce their carbon footprint.
Certainty’s Role
Certainty provides innovative solutions for implementing RBT, enhancing your quality assurance processes, and ensuring compliance with global standards. Our customizable form builder, corrective action delegation, notification system, and the entirety of our tool help enterprises navigate the complexities of risk management and achieve their quality goals.
And now, with Certainty’s AI features, unlock automation throughout your entire risk-management process. Whether it be quickly and accurately completing internal audits and inspections, Enhanced checklist insights, or enterprise-wide AI-enhanced analytics, Certainty AI is advancing risk management.
Book a call with our team today to learn how Certainty can support your risk management program.
You may also be interested in: