As a pioneer in technology and a recognized automotive supplier founded in 1908, Brose is committed to influencing the direction of mobility. By offering cutting-edge mechatronic systems and components, Brose, a German company with its headquarters in Coburg, has established itself as a key player in the automotive sector. Because of the company’s consistent dedication to innovation, quality, and sustainability, top automakers throughout the world view it as a reliable partner.
A noteworthy turning point in Brose’s path was its victory in 2013 when it was honored for its excellent contributions to automotive innovation with the prestigious PACE Award (Premier Automotive Suppliers’ Contribution to Excellence). This renowned award, given to Brose in recognition of its outstanding accomplishments, strengthened its status as a forerunner in the sector. The broad range of products offered by Brose includes for interior components, electric drives, powertrain systems, and vehicle access solutions.
Brose continues to pioneer the way for improvements in automotive technologies that improve safety, comfort, and efficiency all around the world by placing a significant emphasis on research and development.
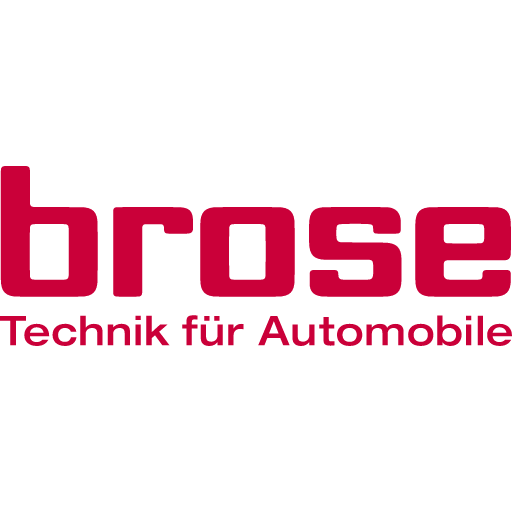

The Challenge
To manage their Layered Process Audits (LPA), which were carried out often and daily across all of their production sites worldwide utilizing Ease.io, Brose faced considerable difficulties before using Certainty Software. It was clear that numerous serious problems existed:
Multilingual Checklists:
Brose operates in numerous locations across the globe, meaning the availability of multilingual checklists with precise translations is a must. Their prior system had issues with effectively producing and maintaining these checklists across multiple languages, which hampered effective compliance and communication.
Reporting Consistency:
Brose had issues combining and consistently reporting LPA findings across several plants. The collection of data for insightful analysis and decision-making was hampered by the lack of a uniform mechanism for question identification.
The Solution & Result
Certainty Software emerged as a comprehensive solution that expertly solved Brose’s issues in handling Layered Process Audits (LPA) throughout their global production units. The introduction of Certainty Software resulted in revolutionary improvements in key operational areas.
A continuous, error-free workflow was made possible by Certainty Software’s seamless integration of all LPA process phases into a single system, which removed the need for manual data transfers. This integration improved data consistency and accuracy throughout the audit process in addition to streamlining processes.
By utilizing mobile devices, Certainty Software enabled Brose’s auditors to record findings immediately on the job, enabling real-time documentation that was supplemented with pictures and graphics. This innovation not only sped up reporting but also improved the accuracy and dependability of audit reports, hastening decision-making and corrective actions.
Brose’s language requirements were successfully met by the multilingual checklist support provided by Certainty Software. By enabling the construction of a single checklist in numerous languages, this feature promoted consistent communication between diverse regions and plants. Standardized question IDs additionally permitted cross-plant result comparison and evaluation, promoting cooperation and knowledge-sharing on a global scale.
The Layered Process Audit (LPA) management landscape across Brose’s global production plants was transformed as a result of the adoption of Certainty Software. These results were greatly aided by the strategic approach used throughout the implementation phase, which included time commitment and obstacle removal.
The following crucial steps were included in the implementation strategy:
Step 1: Administrator Qualification
Brose carefully selected administrators and critical users with in-depth knowledge of the Certainty Software platform. This made sure that the deployment and support processes had a solid base.
Step 2: Pilot Audits
To start the implementation process, pilot LPAs were carried out at a few selected plants in various geographic areas. With this method, adjustments and customization depending on local needs and feedback were possible.
Step 3: Rollout Planning
A thorough planning phase included user qualification, data migration, and LPA questionnaire setup. This stage made sure that the full-scale rollout went smoothly.
Step 4: Continuous Improvement
A notable feature of the implementation process was the inclusion of a feedback loop for continual improvement. In close collaboration with Certainty, Brose actively gathered user feedback to jointly improve the system and improve the product based on actual user experiences.
Together, these tactical actions enabled Brose’s production units to achieve the astonishing feat of streamlining LPA procedures, improving reporting accuracy, and fostering better teamwork.
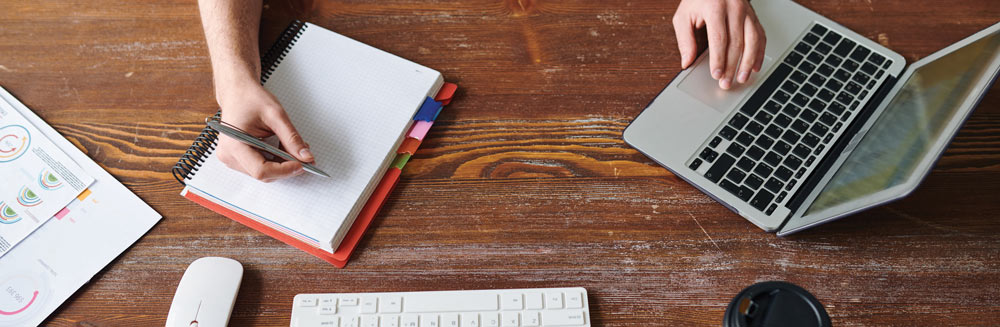