Quality management is an essential component of any business, and its significance is growing with time. To ensure quality, organizations use various tools and techniques to manage their processes and minimize errors. However, the complexity of these processes can make it difficult for individuals to understand and assess them. This is where the Turtle Diagram comes in. […]
Quality Management
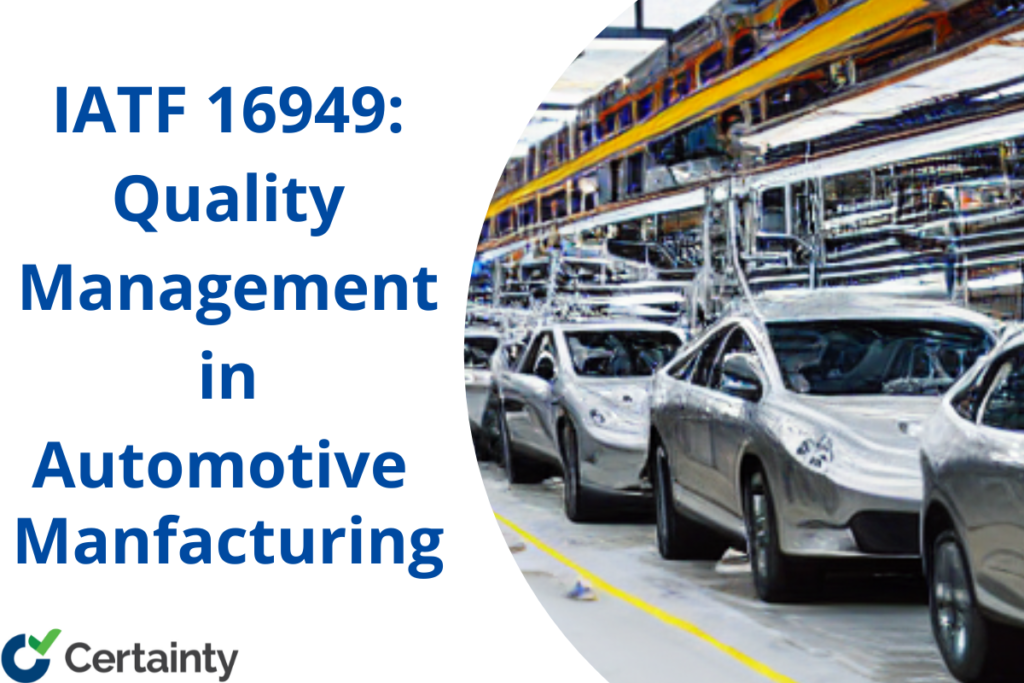
IATF 16949: Quality Management in the Automotive Manufacturing Industry
IATF 16949:2016 is a quality management system (QMS) standard specifically developed for the automotive industry. It was created by the International Automotive Task Force (IATF) and is based on the ISO 9001 international standard, with additional requirements to support the unique characteristics of the automotive industry. Like ISO 9001, IATF 16949 is based on Deming’s plan, do, check, act cycle of continuous improvement. […]
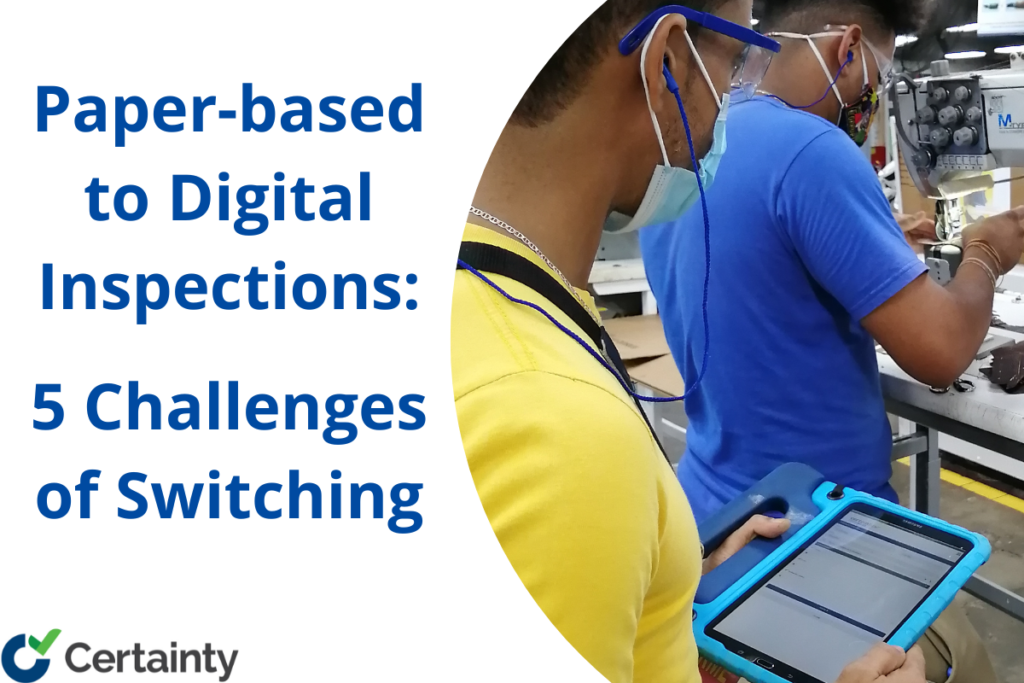
5 Challenges When Switching From Paper-based Inspections to Digital Inspections
Table of contents If you are a business that relies on paper-based inspections, you are likely familiar with the challenges that come with this type of system. Paper-based inspections can be cumbersome and inefficient, from time-consuming data entry to the difficulty of tracking and storing inspection data. Fortunately, there is a better way. Digital inspections […]
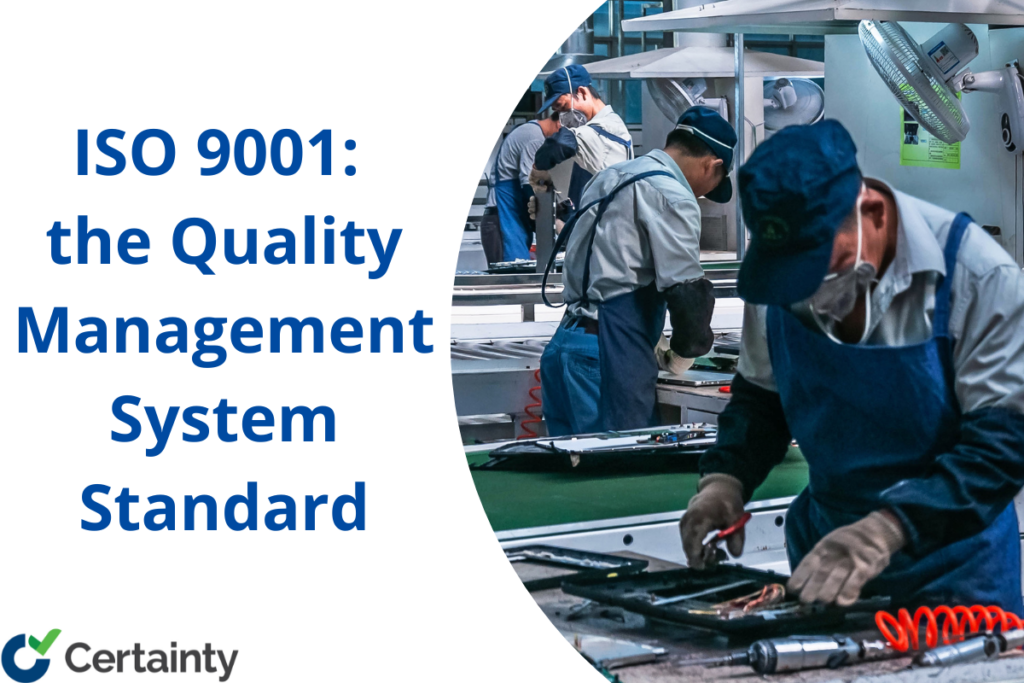
ISO 9001: an Overview of the Quality Management System Standard
The international standard in quality management systems (qms), ISO (International Organization for Standardization) 9001 is currently certified by over one million organizations and companies in over 170 countries (ISO). Built to be used by any business no matter the size, industry, or location, the objective of the ISO 9001 standard is to set clear guidelines for building an optimal quality management system that ensures quality, consistency, and customer satisfaction. […]
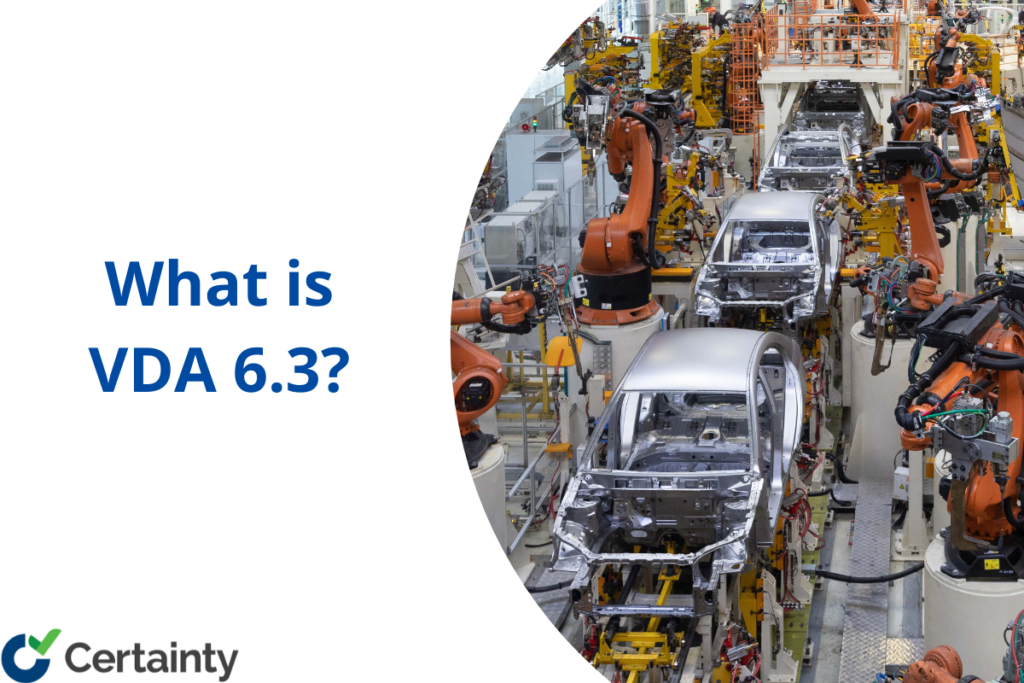
What is VDA 6.3?
VDA 6.3 is a guide to process auditors and outlines the certification requirements for process-based audits and for evaluating controls in the manufacturing process. The internal analysis process of VDA 6.3 focuses on customer satisfaction with customer-specific requirements. […]
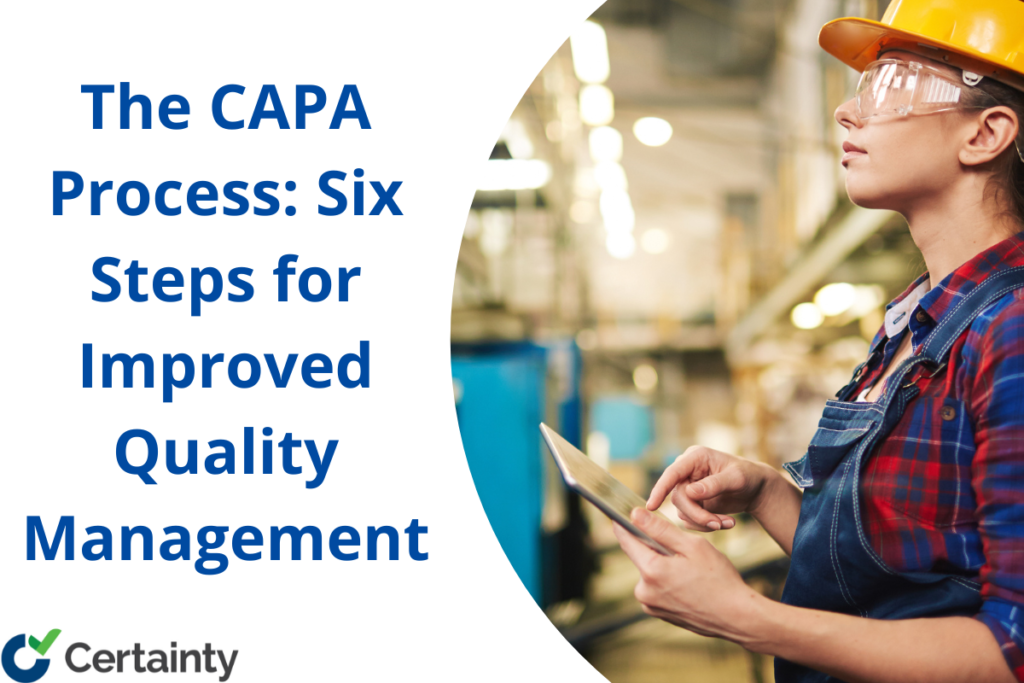
The CAPA Process: Six Steps for Improved Quality Management
The CAPA system helps companies identify non-conformity issues that negatively impact quality, correct these issues through targeted action, and prevent these issues from recurring. […]
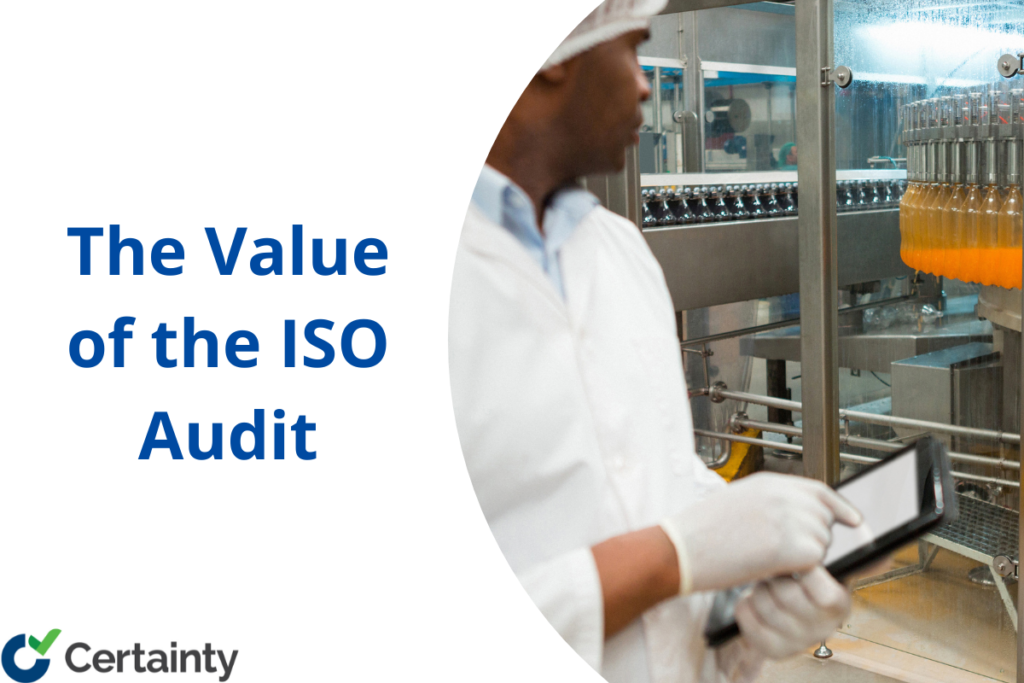
What is an ISO Audit — and Why Does Your Business Need One?
The International Organization for Standardization (ISO) is an independent, non-governmental international organization and certification body with more than 167 members. The goal of the ISO is to create voluntary international standards that help companies evaluate and improve current processes. ISO has been creating and evolving standards for more than 70 years, helping companies stay up-to-date […]
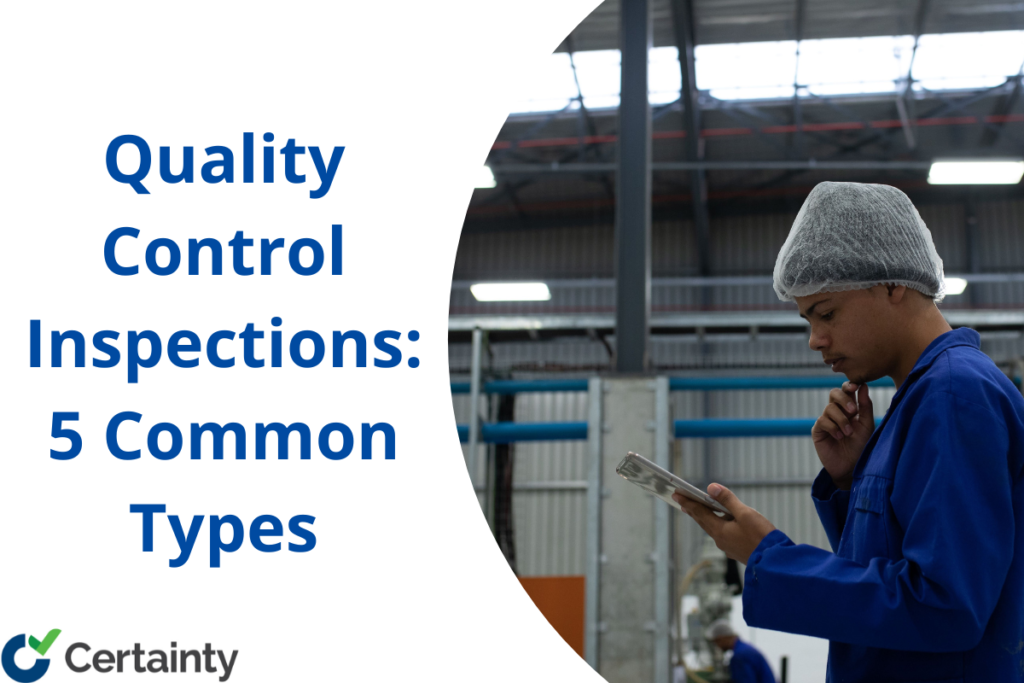
Quality Control Inspections: 5 Common Types to Boost Your QMS
How do you know if your products are good enough for your customers? If you are a manufacturer, you probably have a set of quality standards and specifications that you follow to ensure that your products meet the expectations of your customers and the requirements of the market. But how do you verify that your […]
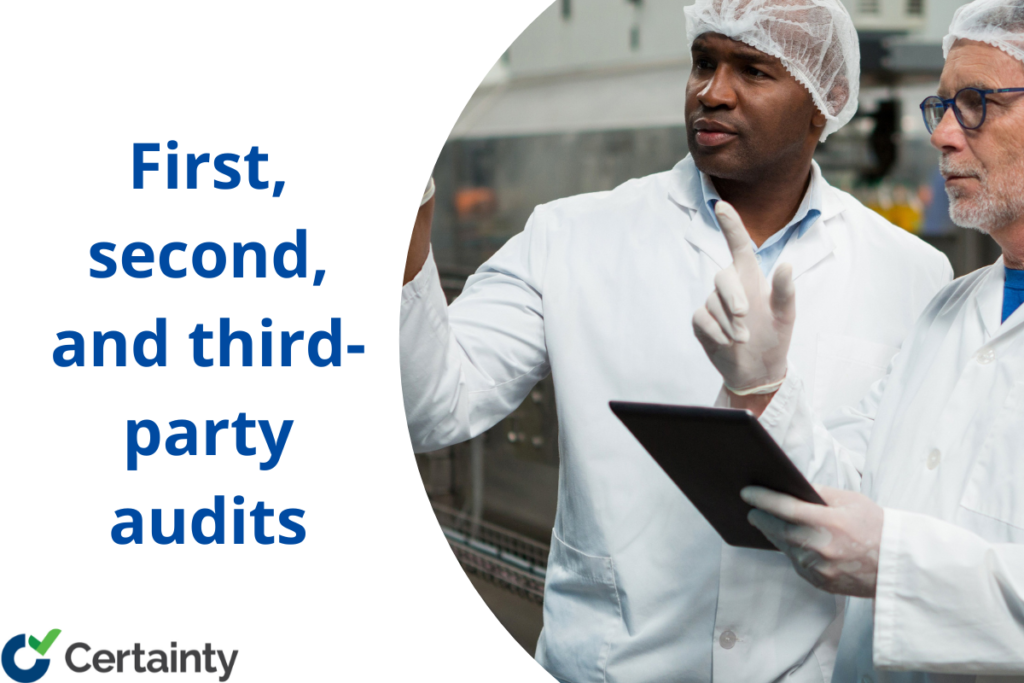
Audit Types Explained: What You Need to Know About First, Second, and Third-Party Audits
Auditing is a process of verifying and evaluating a business’s compliance, quality, and performance. However, there are different types of audits that serve different purposes and have different requirements. In this blog post, you will learn what first-party, second-party, and third-party audits are, how they differ, and why they are important for your business […]
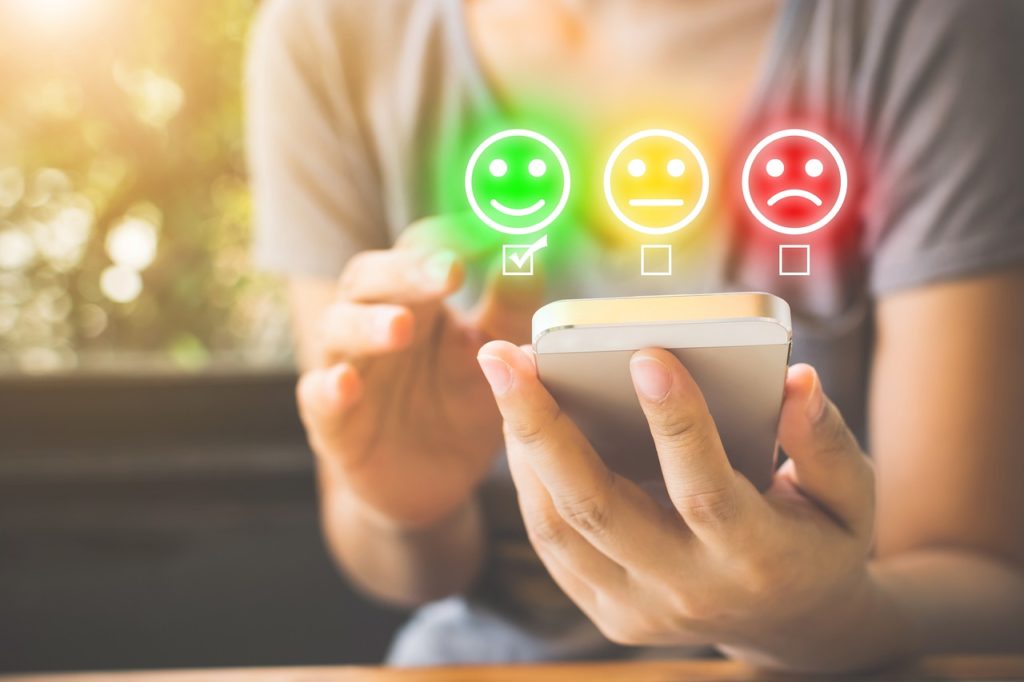
3 Customer Satisfaction Metrics to boost customer loyalty
In a recent article from Deloitte, they found that businesses that offer a high-quality customer experience can lower the cost of serving customers by up to 33%. With competition growing rampantly across the business landscape, customer loyalty has grown in importance. The Customer Satisfaction Assessment helps to address customer needs and strengthen the customer relationship, […]
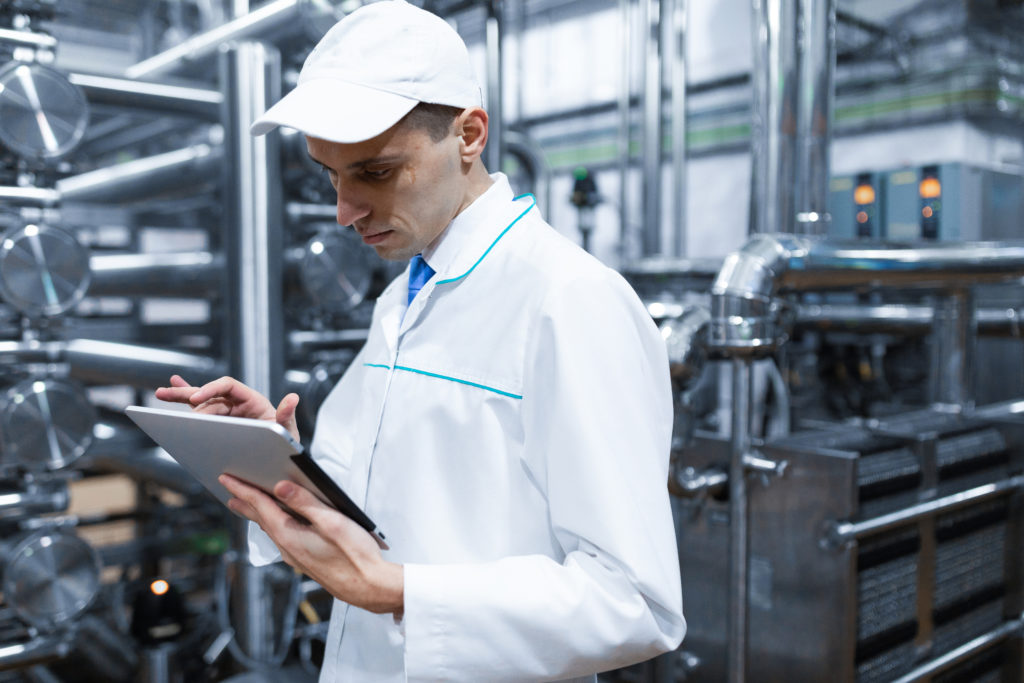
Targeting Total Quality: How a Total Quality Management Audit can Help
Companies lose between 20 and 30 percent of their revenue each year to process inefficiencies. For manufacturing firms, this loss of revenue is often tied to production line processes that are inconsistent, time-consuming, or error-prone. This in turn reduces overall performance and impacts potential profit. An internal Total Quality Management Audit, also known as a […]
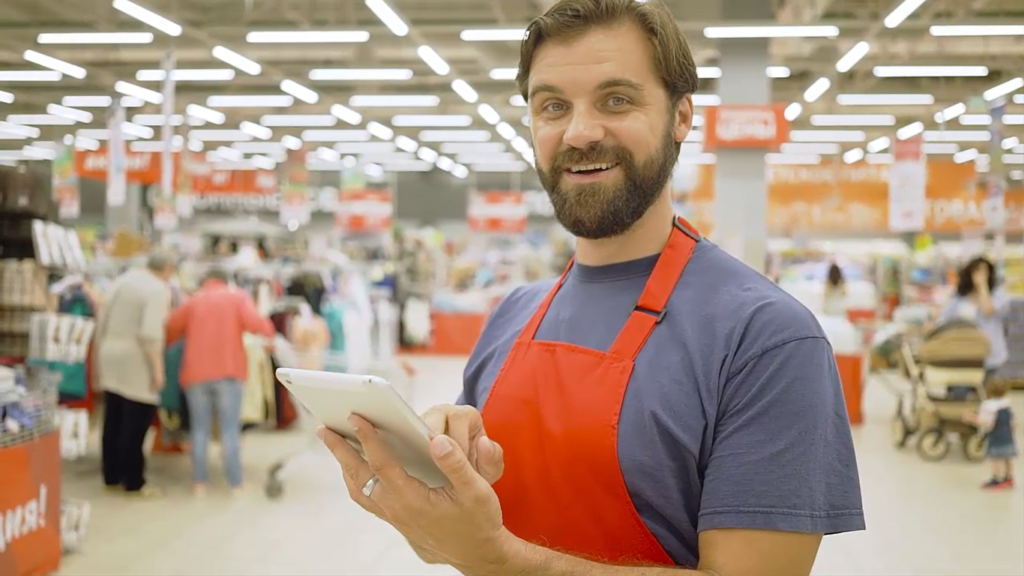
The Four Phases of a Continuous Improvement Assessment — and What They Mean for Your Business
For manufacturing companies to respond to shifting consumer demands and supply chain constraints, continuous improvement is crucial. In order to improve your company’s operations, employ the continuous improvement assessment frameworks described in this blog article. […]
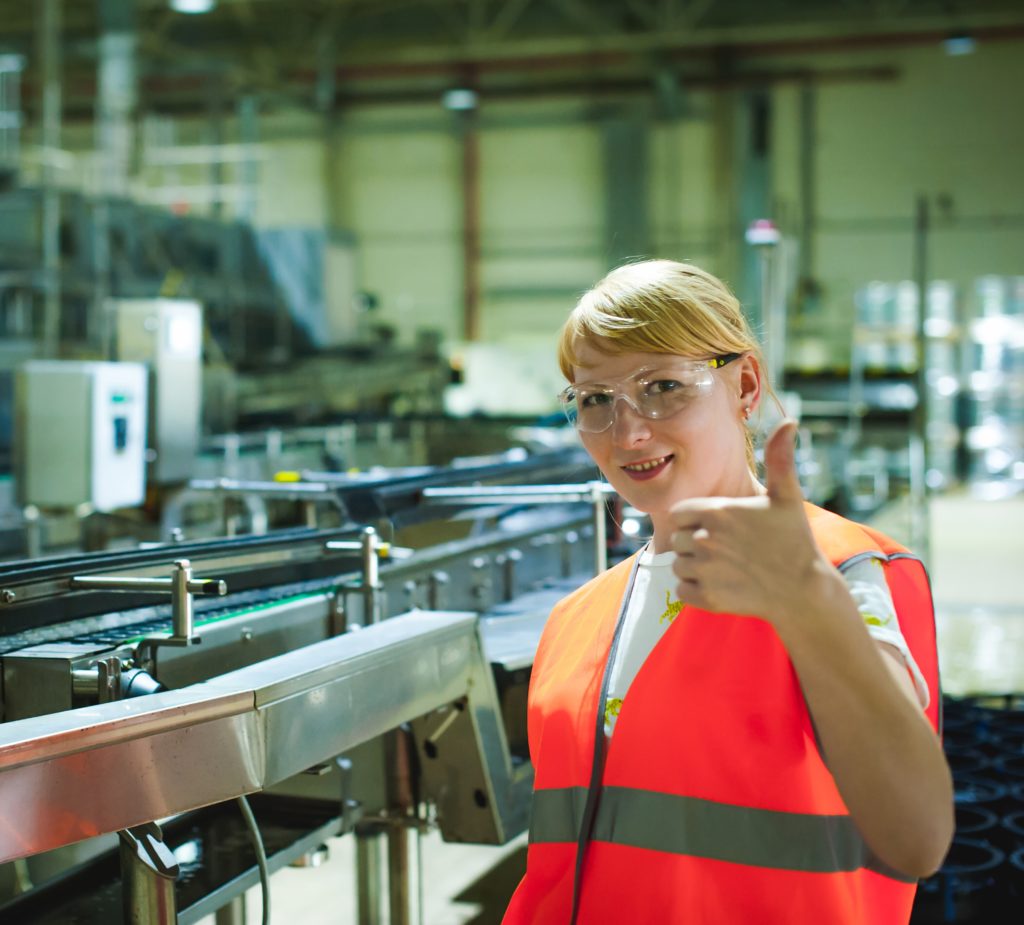
Keeping Quality High: The Benefits of a Layered Process Audit
Manufacturers in the United States employ more than 8.5 percent of the total workforce and account for over 10 percent of the country’s gross domestic product (GDP). As the scale of manufacturing ramps up, however, so does regulatory oversight to ensure that products produced meet standards such as the ISO 2859-1 acceptance quality limit (AQL). […]
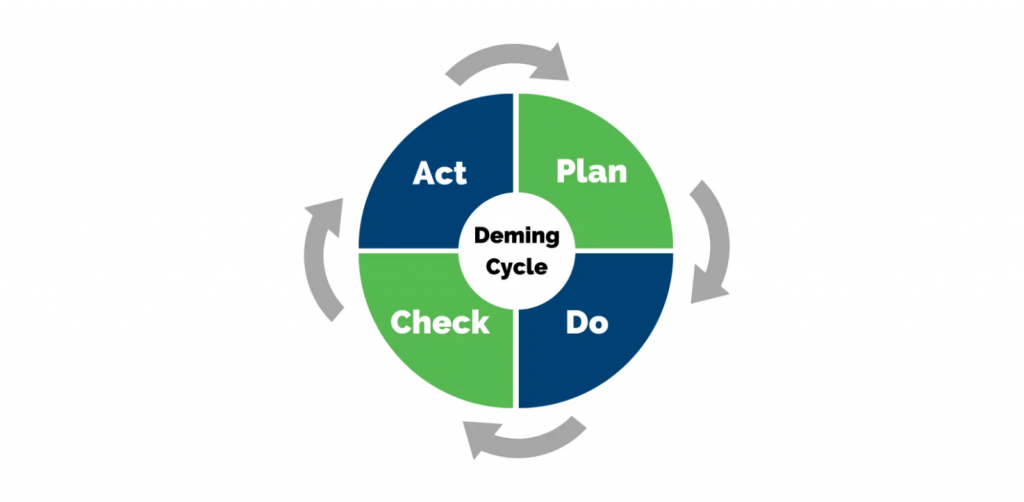
What Is An ISO 9001 Audit And How To Be Prepared
According to one study, businesses that implemented the ISO 9000-based quality standards found an 18% increase in client satisfaction and a 15% cost reduction. ISO 9001 is an internationally recognized Quality Management System (QMS) criteria program. This program guides businesses of any size to maintain or find improvements in their quality management system and processes. The ISO approach […]
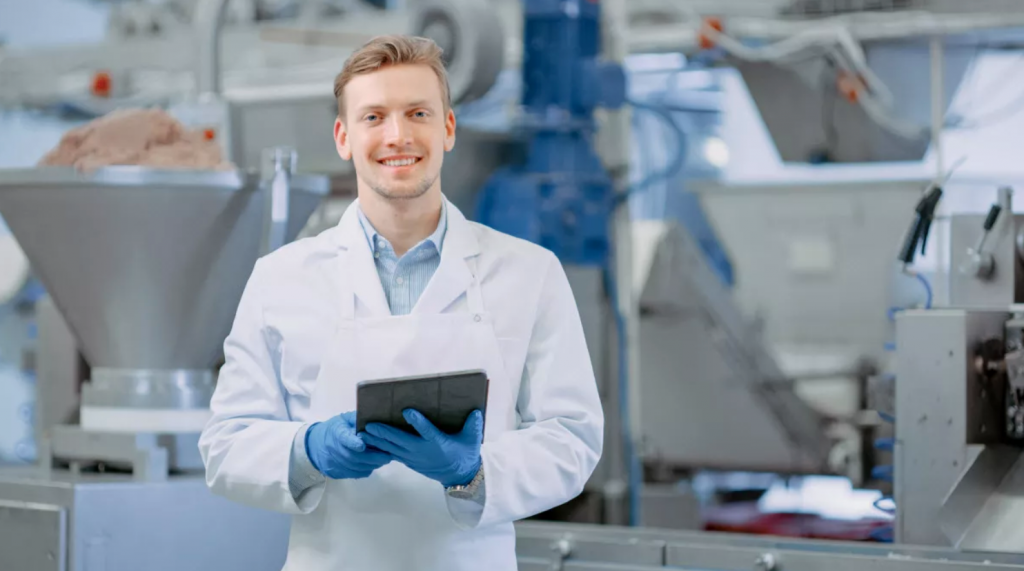
What Are Quality Assurance Inspections And Why They Matter
While price and positive experiences remain the leading factors in brands’ abilities to keep customers satisfied, quality also plays a critical role. According to research firm PWC, 52 percent of U.S. consumers would consider switching from one brand to another based on product quality. The result? It’s critical for companies to create policies and processes that […]