Table of contents
Hazardous substances in the workplace pose potential health risks. Consider a manufacturing plant with an excess of dust and vapors. Not only could these substances harm workers after prolonged exposure, but could lead to even more significant hazards such as unexpected and uncontrolled fire or explosions. This isn’t just an academic risk — as noted by World-Grain, the United States experiences eight-grain dust explosions every year on average.
Regulations such as COSHH were designed to help manage and mitigate these risks. But what is COSHH? What does it cover, and who’s impacted? Let’s dive in.
What Does COSHH Stand For?
COSHH stands for the Control of Substances Hazardous to Health. It was implemented in the UK in 2002 and designed to help protect workers from hazardous substances in the workplace and reduce the risk of potential injuries or accidents caused by these substances.
COSHH is a law, not a guideline, which means that all businesses subject to COSHH regulations must follow them — failure to do so could result in workplace audits along with business fines and penalties.
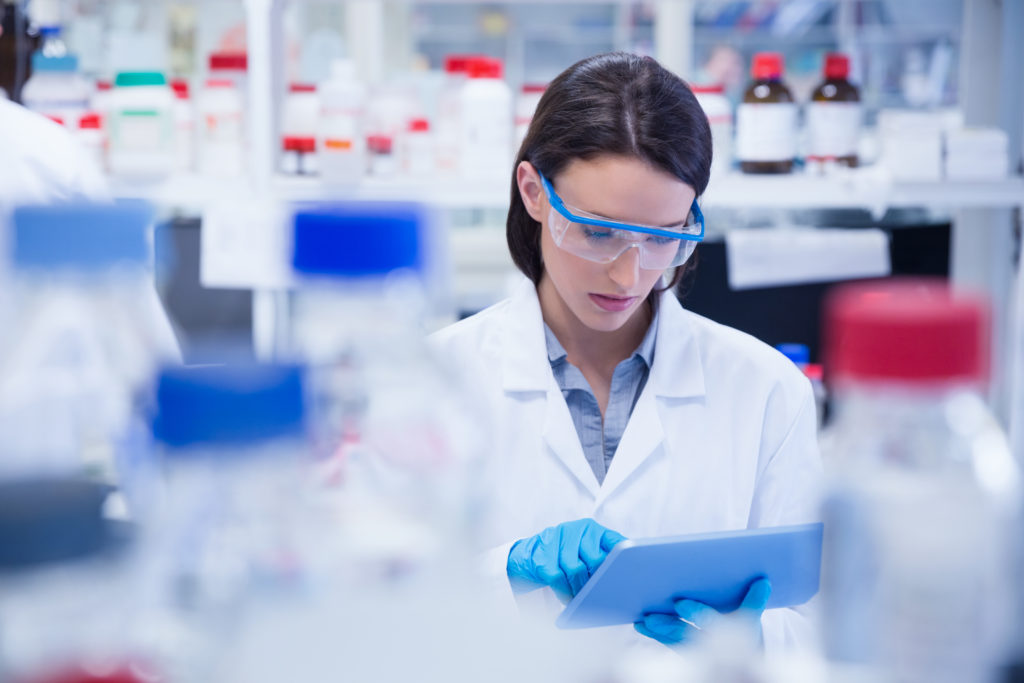
Who’s Impacted by COSHH?
According to the UK’s Health and Safety Executive (HSE), any business that uses potentially hazardous or harmful substances or materials is subject to COSHH. This includes those who are self-employed, whether they have a staff or are the only worker. In the event they are the only employee of the business but take or use hazardous materials on the premises of other people or other businesses, all parts of COHH apply except for those related to monitoring and health surveillance.
Put simply, if you have hazardous substances in your workplace or transport them somewhere else for use, COSHH applies.
What Substances Does COSHH Cover?
Potentially hazardous substances include:
- Chemicals
- Products that contain chemicals
- Fumes
- Respirable Dust
- Vapors
- Mist
- Gases
- Biological agents, such as germs
- Carcinogens
- Corrosive or flammable materials
- Eye or skin irritants
Worth noting? COSHH does not cover lead, asbestos, or radioactive substances. This isn’t because they don’t pose any risk (they do), but because each of these materials is governed by specific legislation that details their handling, storage, and disposal.
Five Tips to Implement COSHH
So how do you implement COSHH in your organization? Start with these five essentials.
1) Asses Risks
First up is a COSHH risk assessment. By evaluating potential health hazards across your organization, you’re better equipped to take effective action. Here, tools such as job site safety inspection checklists and personal protective equipment (PPE) assessment checklists can help streamline this process. Where a site inspection checklist lets you pinpoint current problems, PPE assessment ensures that in cases where working with chemicals is a necessity, the staff is protected.
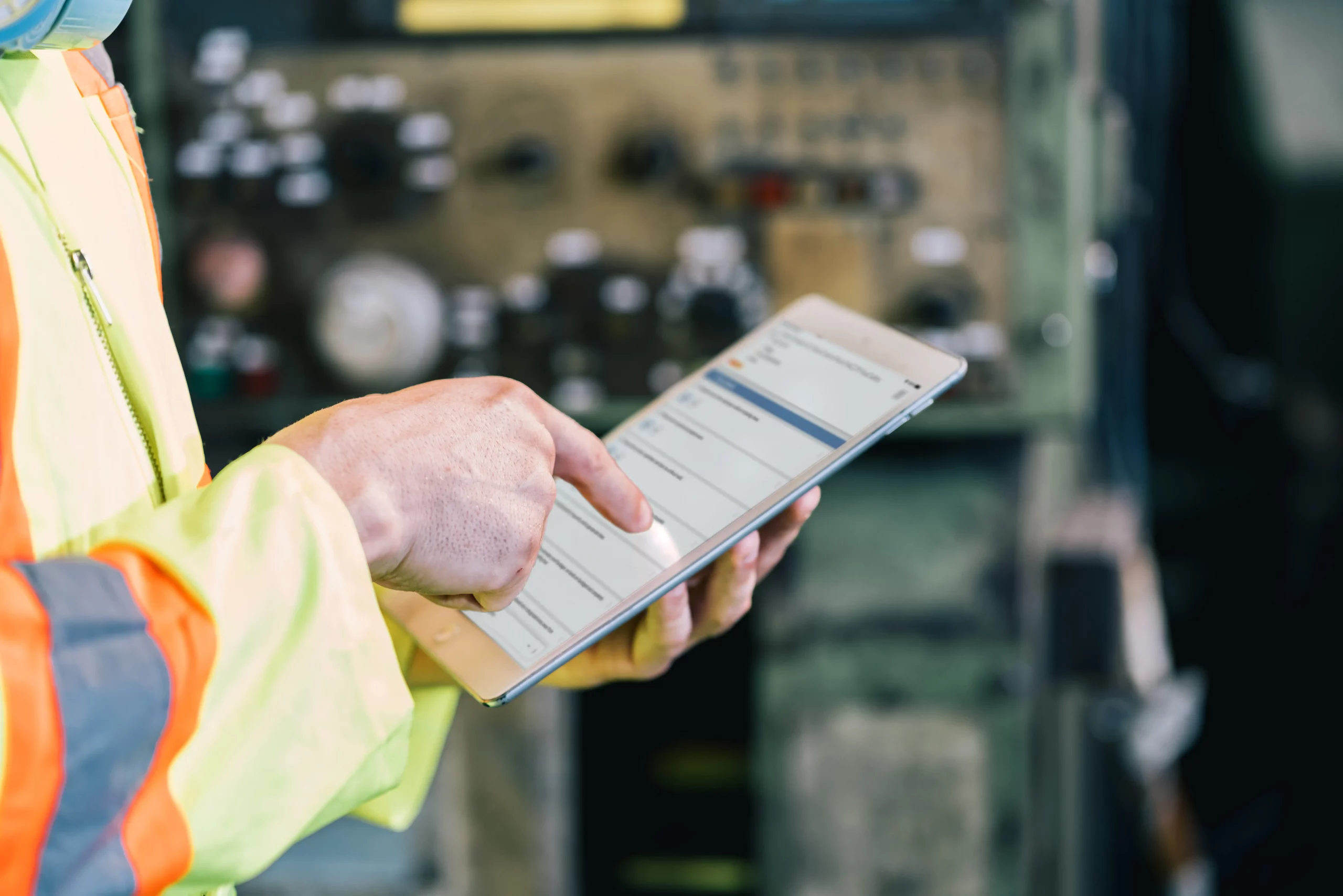
30+ Audit and inspection checklists free for download.
2) Educate Employees
Next up is employee education with training. Here’s why: The more workers know about hazards and how to avoid them, the better you’re able to meet COSHH regulations. For example, training can help staff identify the telltale signs of a gas leak or vapor issue before lives are put at risk.
3) Create Control Measures and Prevention Plans
COSHH also requires companies to create and implement control and prevention plans that both reduce the risk of hazardous material threats and help limit overall risk in working environments. In practice, this means finding ways to reduce the use of hazardous chemicals or ensure control of exposure during use.
4) Ensure Controls are Effective
Simply creating controls isn’t enough: Companies also need to ensure these controls are effective. This means conducting regular tests to make sure controls are working as intended, and making changes as necessary to adapt as worksite environments change.
5) Develop a Robust Accident Response Plan
Finally, organizations must develop accident response plans to deal with issues as they occur. No matter how good your planning or how robust your training, accidents are (by their nature) unexpected, meaning they can happen at any time. From spillages that cause ill health to chemical mixtures that exceed workplace exposure limits, accidents are always possible. Accident response plans are therefore necessary as a framework for teams to follow if an accident occurs and lives are at risk.
You may also be interested in:
Safety Observations: 9 Common Examples