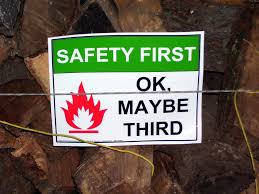
We often say that safety is our number one priority and we’d probably like it to be. But if we drill down into our business we’d probably find that not everyone agrees with us. We may have signs and slogans plastered all over our walls shouting ‘Safety First’ but in real terms, our behavior probably indicates that ‘getting the job done’ is our number one priority. ‘Safety’ is not a priority that can change according to external factors, it’s a core value that must be considered in every action and task that we undertake. So, do we really put safety first? Let’s discuss.
We probably don’t mean it but there are many ways we demonstrate exactly where ‘safety’ is on the management priority list. An example of this probably starts with our board meetings… where does ‘safety’ appear on the directors’ board agenda every month? It may well be down at the foot of the page and is the last thing to be discussed after all the interesting stuff has been debated, everyone’s tired and wants to go home. If safety really is our top priority, perhaps it should be the FIRST topic of conversation on the agenda. Other examples might include spending hours in operations planning or production meetings but only a few minutes on safety or toolbox talks. Failure to do what we say we do sends a powerful message about safety to all our people. It’s our inaction and lack of belief in our own rhetoric that sends a far more powerful signal than any slogan we’ve got posted up in the office or out on site.
A good question to ask is why do our managers and people who really should care deeply about safety behave in ways that contradict their supposed values. We need to look closely at how it is measured. Incident Rate, Lost Time Rate, and other indicators can be poor measures of safety. These indicators may tell us how many people got hurt and how badly, but they don’t tell us how well our business is doing at preventing accidents. This is because these indicators can be a poor gauge of prevention because of what statisticians call ‘natural variation’. In other words, it is a statistical fact that if the number of unsafe conditions and behaviors in a period of, say, a year were held constant, a business could experience a different number of incidents during the first half of the year and the last half. Thus, incident rates can get better or get worse with absolutely no change in conditions or behaviors being made. The result is that a business can go for long periods of time without accidents, despite having an unsafe work environment. This situation mitigates making safety a priority when managers may do nothing about safety for a period yet their behavior can be reinforced with a good incident rate. This is probably what contributed to the concerns of the Maritime Union of Australia (MUA) which we referred to last week.
In the case of measuring productivity and quality, for example, we find that those measures tend to be provided with more frequent and sensitive measures and are therefore more visible and immediate and therefore likely to change management behavior. So it’s easy for ‘safety’ to find itself on the back burner. When an incident rate is apparently low, we might assume all is well with safety and focus on other priorities.
If we really want to make ‘safety’ a priority, we need to use various measures to quantify it. While Incident Rates are necessary and important measures, they should be used along with others. Other measures should focus on employee behavior such as tracking what people are doing every day to prevent accidents. When there are measures of what we really do on a regular basis to prevent accidents, we can ensure those activities do occur. For example, a business that has a behavior-based safety process in place has records that track our regular activities aimed at improving safety conditions and behavior. Daily and weekly responsibilities will ensure that safety is elevated to an equal footing with other business measures and really help make safety a priority for everyone.
To learn more about Certainty Software, click here.