Table of contents
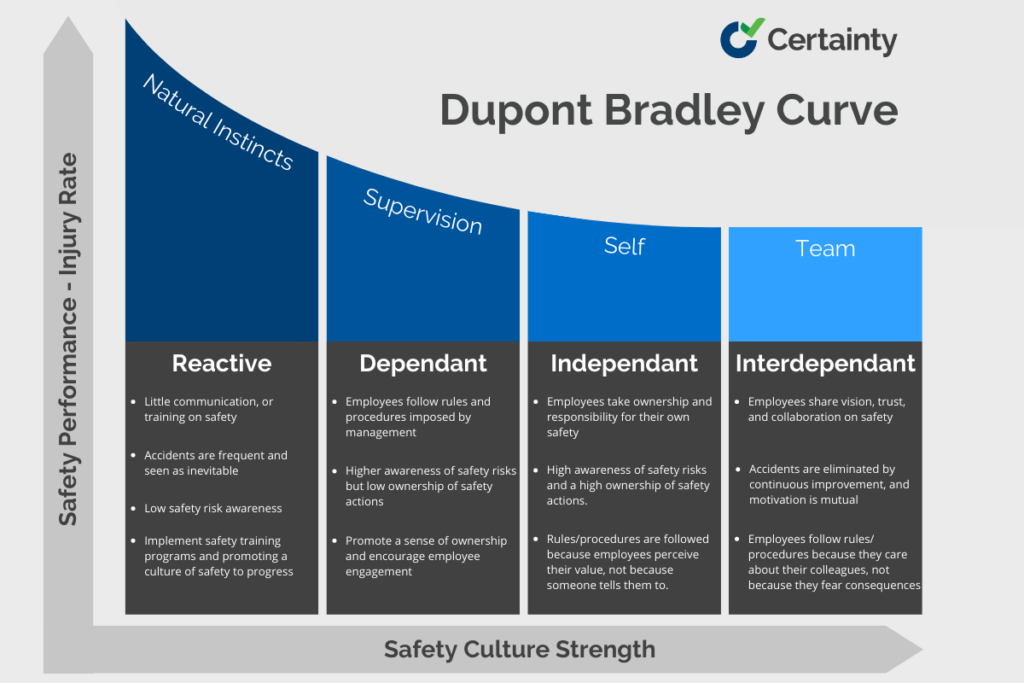
What do you consider operation excellence to be? For many, it’s considered to be when a company can reliably and effectively add value for its stakeholders, consumers, and workers. To succeed in business today, one must have a competitive edge, please clients, and expand.
It is not simple to achieve operational excellence, though. Numerous issues confront organizations including shifting consumer expectations, escalating rivalry, developing technological capabilities, and regulatory constraints. Organizations need to approach performance measurement and improvement holistically to address these issues. Examining the process maturity, safety performance, and financial results are all part of this.
Here’s where the Bradley Curve comes in handy. As a framework that shows how safety culture and operational performance are related, it demonstrates how raising the safety culture improves performance in other areas including quality, efficiency, and profitability.
What is the Bradley Curve?
The Bradley Curve is a framework that illustrates the relationship between safety culture and operational performance. It shows how improving safety culture leads to better outcomes in other aspects of performance, such as quality, efficiency, and profitability.
The original Bradley Curve was created by DuPont in 1995 based on a plant manager’s reading of a book by Stephen Covey. It has since helped many organizations understand the importance of taking responsibility for safety and moving towards zero injuries.
Having gone through a few updates, the original Bradley Curve with just three stages has been updated to now include a fourth and vital stage in safety culture – the Interdependent Stage.
What makes the Bradley Curve stand out is that It’s not a prescriptive or linear model, but a descriptive and dynamic one. It can help organizations better assess their current situation, identify improvement opportunities, and track their progress.
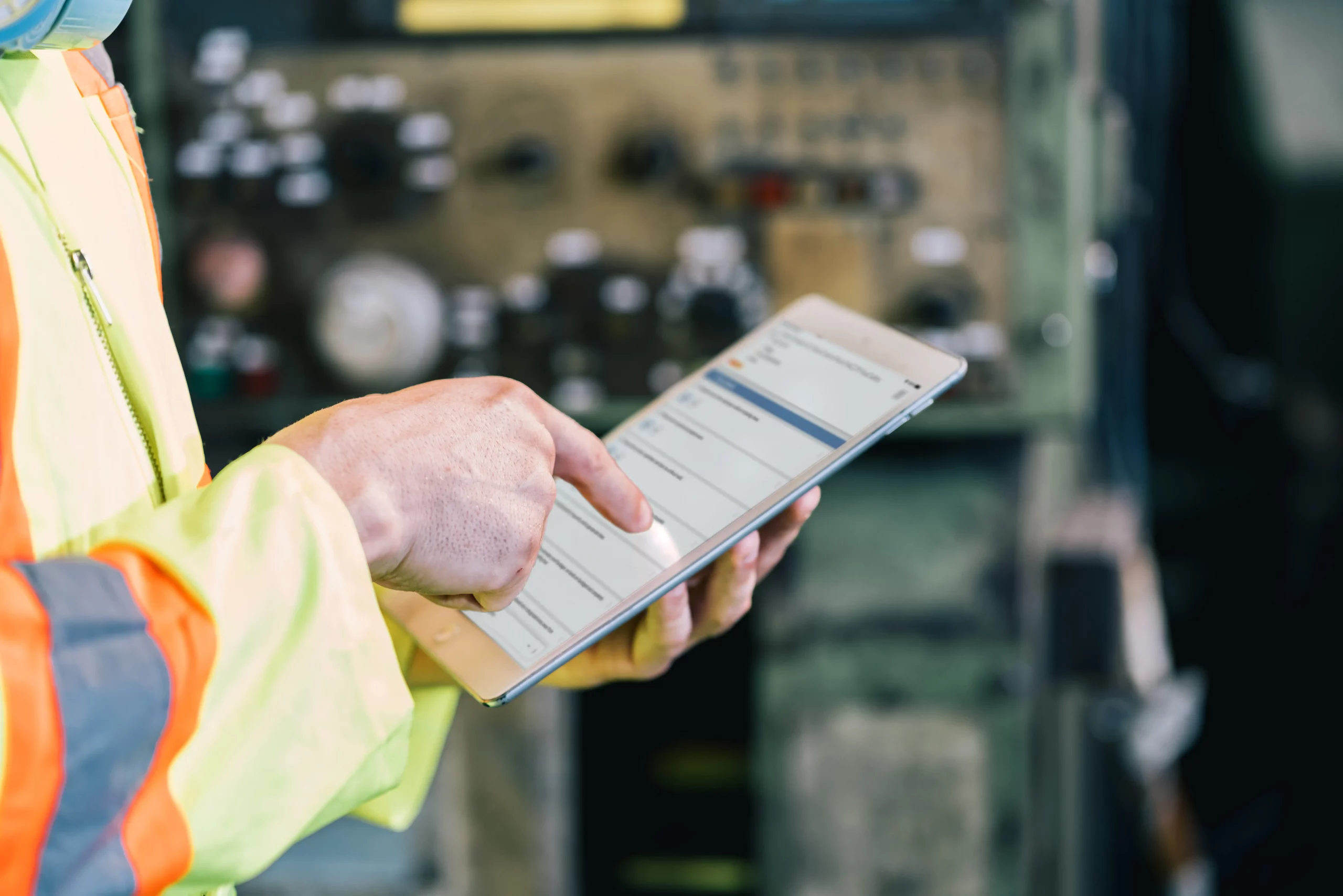
30+ Audit and inspection checklists free for download.
The 4 Stages of the Bradley Curve
Setting off on a path of operational excellence and safety culture, the Bradley Curve lays out its structure, connecting the fundamental elements and the stages that businesses go through. The four stages of the Curve reveal how safety culture and performance are changing, just as the essential elements affect each other.
Reactive Stage
The Reactive Stage represents the lowest level of safety culture, where employees rely on their instincts and look out for themselves. There is little management commitment, communication, or training on safety. Here, accidents are frequent and seen as inevitable. Businesses in the Reach Stage commonly experience poor financial results and suboptimal processes. If you determine that you’re business is operating in the Reactive Stage, then it might be time to hit the emergency button and make changes immediately.
From an employee standpoint, signs of Reactive Stage behavior would be a tolerance of risky behavior and a lack the care about the potential impact of a workplace accident. There is a severe lack of ownership in workplace safety and employees tend to place the blame for injuries, or other harm on other workers or other forces.
Dependent Stage
The Dependent Stage is the second level of the Bradley Curve, where workers comply with directives from management about policies and practices. Safety awareness and training have increased, but motivation comes from outside sources such as management pressure. Although fewer, accidents are still thought to be inevitable.
Employee ownership of safety measures is limited at this point, despite a heightened awareness of safety hazards. They don’t follow policies or processes because they wish to; they do so because they feel they have to. There’s little to no effort to enhance the current quo of safety. Instead, employees might consider that solely the role of upper management. It would be uncommon for employees to ask for criticism or opportunities for improvement since they consider accidents as isolated incidents or bad luck.
Independent Stage
At the third level of the Bradley Curve, known as the Independent Stage, workers assume accountability and ownership for their safety. There is a feeling of accomplishment, ability, and self-satisfaction.
At this stage, employees have a high awareness of safety risks and a high ownership of safety actions. They follow rules or procedures because they perceive their value, not because someone tells them to.
Interdependent Stage
The Interdependent Stage occurs when employees collaborate and support one another, fostering a strong safety culture. This stage is characterized by teamwork and mutual care among employees and leads to the highest level of safety culture within the organization. There is a shared vision, trust, and collaboration on safety.
At this point, workers are very aware of safety risks and take responsibility for their own and others’ safety. They follow rules or procedures because they care about their colleagues, not because they fear consequences. They act proactively to prevent incidents for themselves and others, and they report and learn from near misses as a team.
How to Implement the Bradley Curve
To apply the Bradley Curve framework to your organization, you should follow this four-step process:
1. Assess Your Current Performance
To find your position on the curve, you must need to first collect and examine the right data and key performance indicators (KPIs). This often involves direct feedback from your staff, management, or other key stakeholders. There are numerous approaches to achieve this feedback such as questionnaires, internal audits, interviews, or observations.
While there are many options on KPIs in this situation, injury rate, incident rate, and near miss rate are three of the common safety performance indicators we recommend at a minimum.
2. Identify Improvement Opportunities
Based on your assessment, you will need to identify the gaps between your current and desired performance. You can use tools such as root cause analysis, SWOT analysis, or benchmarking to find out what causes your problems and what solutions are available.
3. Develop Action Plans
Based on your improvement opportunities, the next step is to develop action plans to address them. You can use tools such as SMART goals, PDCA cycle, or RACI matrix to define your objectives, actions, responsibilities, and timelines.
4. Implement and Monitor
Based on your action plans, you now need to implement them and monitor their progress. Use tools like dashboards, reports, or feedback loops to track KPIs, assess results, and make necessary changes.
Some examples of tools that you can use are:
- Dashboards: A visual display of your KPIs that shows your current performance and progress toward your goals.
- Reports: A written document that summarizes your data and analysis and provides recommendations for improvement.
- Feedback loops: A process of collecting and acting on feedback from your stakeholders to ensure alignment and satisfaction.
Self-Assessing Your Safety Culture
Self-assessing your safety culture is no small feat. It takes time and resources to dive into the details and uncover where you might sit on the Bradley Curve. However, we’ve put together this table that gives you a quick and easy general idea about where your organization might be sitting. This table does not provide a definitive answer, but it supplements your research and can give you an initial idea about where you stand
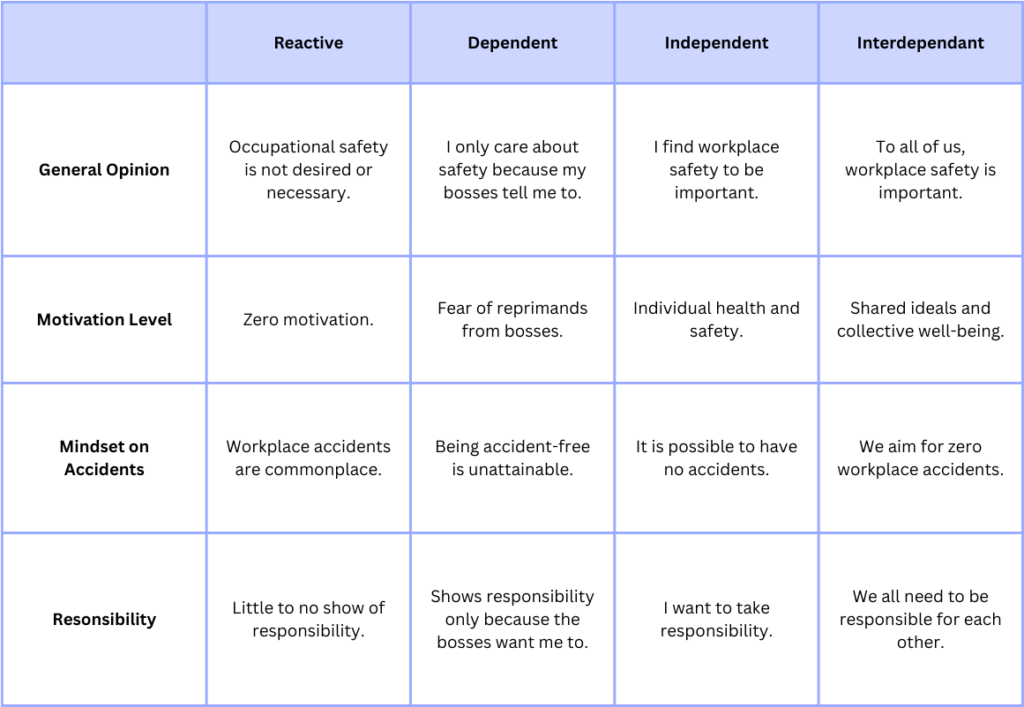
Do you see a pattern in your employees’ conduct that suggests they are merely “going through the motions” when it comes to workplace safety because management is pressuring them to? Then you’re likely at the second stage – better known as the Dependent Stage. Or do you observe that your company is committed to promoting collective safety? Then you’re organization has a thriving safety culture as you’re likely in stage for or the Interdependent Stage. Instead of doing a drawn-out examination, you can use this chart to get quick advice on where you fit into the Bradley Curve.
How to Optimize Your Safety Culture
The main challenge of using the Bradley Curve is collecting accurate data for reliable insights and reporting results effectively. If your data is incomplete, inaccurate, or outdated, your assessment may be skewed or misleading.
You need strong and dependable software for inspecting and auditing. One that helps you gather, monitor, and report precise data for a better understanding of your business. This will enable your team to enhance performance and sustainability.
Certainty Software is an enterprise-level inspection software solution that specializes in helping organizations improve their safety culture and operational performance. With Certainty Software, you can:
- Easily create and customize forms for any type of inspection or audit
- Collect data wherever you are – online, offline, in the field, or on the shop floor
- Track and manage issues, risks, and non-conformances by creating and delegating actions
- Report consistent, comparable, and accurate performance metrics using dashboards, reports, or feedback loops
- Benchmark and improve your safety culture using the Bradley Curve framework
To learn more about Certainty, you can schedule a brief demo. This will help you understand how Certainty can benefit your audits and inspections.
You may also be interested in: