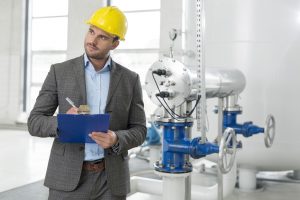
Sure, there are some obstacles to using checklists which we’ve touched on in the preceding blogs. But the far biggest obstacle to their successful implementation is the ‘expert’ who’s offended at the thought of ever needing a checklist. That ‘expert’ can be anyone in the organization. The expert will give any number of reasons checklists are a waste of time but none of those reasons really stand up to scrutiny.
The use of a checklist WILL help improve efficiency by minimizing mistakes. Checklists provide a written trail detailing what’s been done at every stage of a project. Checklists can be created and used on paper or online. They are as good for making time-critical decisions as they are for methodically going through a step-by-step procedure. They work equally well in any industry or field that requires a process— from hotel management, education, manufacturing, and auto repair to the practice of medicine, aviation, oil, gas, and the shipping industries.
The ideal checklist should be precise, efficient, easy to use in any situation, and straight to the point. All the items on a good checklist should be actionable and grouped by category. You can get started easily and create a checklist quickly and simply yourself by using WORD or other software. In WORD, for example, you can create two kinds of checklists:
- Lists with checkboxes or check marks instead of bullets or numbers. Use boxes if you plan to print the list, for example, and check off each item you complete, or
- Lists you can check off in Word. This involves adding content control from the Developer tab, but you don’t need to be a developer to do it.
Just check out the Microsoft support page here:
If you’re still not sure if a checklist will improve the performance results of your current or future projects, just have a think about the different purposes they can have.
- Step-by-step Procedures: Checklists that take a person through a complex procedure to minimize errors.
- Verification and Inspection: Checklists allow someone to check that a task has been done correctly for inspection purposes.
- Evaluation: Checklists allow the user to assess a person or a product. For example, whether someone is a good match for a job or whether a product has all the required components.
- Troubleshooting: Checklists can be used for finding a technical or mechanical error when it lists ways to troubleshoot common problems.
- Observation: Checklists delineate a set of possible behaviors an observer can check off when trying to understand an individual’s performance.
For more on Certainty Software Checklist Solutions, click here.