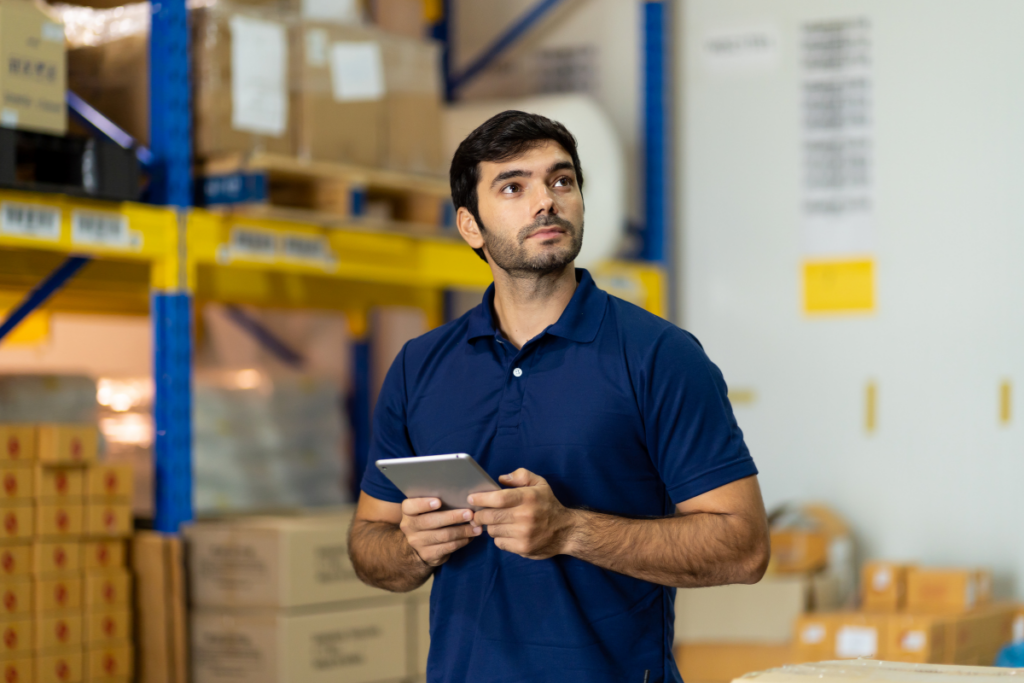
Ensuring the quality and compliance of your products before they reach customers is more important than ever in today’s market. Pre-shipment inspections (PSI) play a crucial role in this process, a safeguard to confirm that products meet all necessary standards and specifications.
What is Pre-Shipment Inspection?
Pre-shipment inspection (PSI) is a quality control process conducted before goods are shipped to verify that they conform to specified quality standards and contractual requirements.
The primary objectives of PSI are:
- Quality Assurance: Ensuring your products are free from defects and meet quality standards.
- Quantity Verification: Confirming that the correct quantity of goods is being shipped.
- Regulatory Compliance: Ensuring your products comply with relevant regulations and standards to avoid legal issues and ensure smooth customs clearance.
Industries such as manufacturing, retail, electronics, and textiles rely heavily on PSI to maintain high product standards and ensure customer satisfaction.
The Importance of Pre-Shipment Inspection
Implementing pre-shipment inspections offers several critical benefits for businesses:
- Reduction of Defective Products: When you can identify defects and discrepancies before shipping, you can avoid the substantial costs associated with returns and recalls, protecting your organization’s financial interests.
- Customer Satisfaction and Brand Reputation: High-quality products lead to satisfied customers, enhancing your brand loyalty and market position.
- Minimization of Financial Losses: Preventing the shipment of non-compliant or defective products helps businesses avoid financial losses due to returns, recalls, and non-compliance penalties.
- Legal and Regulatory Compliance: Ensuring adherence to international standards and regulations minimizes the risk of legal issues and fines, ensuring smooth cross-border transactions.
Key Components of Pre-Shipment Inspection
A comprehensive pre-shipment inspection involves several critical components:
Visual Inspection
Visual inspection is the first step in PSI and involves checking your products for any visible defects or damages. This step is crucial for identifying issues such as:
- Surface Imperfections: Scratches, dents, or discoloration.
- Assembly Issues: Misalignment or loose parts.
- Contamination: Presence of foreign materials.
Standards like ISO 2859-1 for statistical sampling procedures and inspection by attributes often guide these inspections. Utilizing the Acceptance Quality Limit (AQL) method, inspectors can determine the maximum number of defective units allowed in a batch for the lot to be accepted.
Verification of Product Specifications
This component ensures that your product meets all required measurements and standards. Specific checks that should be made in a pre-shipment inspection include:
- Dimensions and Weight: Verifying the product’s size and weight against the specifications.
- Materials and Components: Ensuring the correct materials and components are used as per the Bill of Materials (BOM).
- Compliance with Industry Standards: For example, in electronics, compliance with standards like RoHS (Restriction of Hazardous Substances) or CE marking in Europe.
- Adherence to ANSI/ASQ Z1.4 Standards: This is the standard for sampling procedures and tables for inspection by attributes, used widely for product quality inspections.
Functional Testing
Functional testing ensures your product performs as expected. This involves:
- Operational Checks: Testing the product’s functionality in real-world scenarios.
- Performance Metrics: Measuring performance against specified benchmarks.
- Safety Tests: Ensuring compliance with safety standards such as UL (Underwriters Laboratories) for electrical products or ASTM (American Society for Testing and Materials) standards.
Packaging and Labeling Checks
Ensuring that packaging and labeling comply with shipping and regulatory standards is critical for:
- Protection During Transit: Verifying that packaging materials meet ISTA (International Safe Transit Association) standards.
- Regulatory Compliance: Ensuring labels include necessary information such as handling instructions, product information, and regulatory markings (e.g., FDA for food and drugs).
- Brand Consistency: Checking for accurate and consistent branding and labeling across all units.
Documentation Review
Verifying that all necessary paperwork is complete and accurate involves:
- Invoices and Packing Lists: Confirm that quantities, product descriptions, and pricing match the purchase order.
- Certificates of Compliance: Check for certificates like Certificate of Origin, MSDS (Material Safety Data Sheet), or any industry-specific certifications.
- Customs Documentation: Ensure all documents required for international shipping are to avoid delays at customs.
Pre-Shipment Inspection Procedures
Conducting a pre-shipment inspection involves a series of well-defined steps:
- Pre-Inspection Preparations:
- Define inspection criteria and standards.
- Select an experienced inspection team.
- Prepare the necessary tools and documentation.
- On-Site Inspection Process:
- Conduct random sampling of products.
- Perform visual inspections and functional tests.
- Verify product specifications and packaging.
- Post-Inspection Procedures:
- Compile a detailed pre-shipment inspection report.
- Address any identified non-conformities.
- Implement corrective actions as necessary.
Best Practices for Effective Pre-Shipment Inspections
To maximize the effectiveness of pre-shipment inspections, your company should:
- Establish Clear Inspection Criteria: Define and communicate specific standards and criteria for inspections.
- Regular Training for Inspection Teams: Ensure that inspection teams are well-trained and up-to-date with the latest standards and practices.
- Leverage Technology: Utilize advanced tools and software to enhance inspection accuracy and efficiency.
- Continuous Improvement: Use feedback and data analysis to continuously refine and improve inspection processes.
Choosing the Right Inspection Service Provider
Selecting a reliable pre-shipment inspection provider is crucial for ensuring effective inspections. Key factors to consider include:
- Expertise and Experience: Look for providers with a proven track record in the relevant industry.
- Global Reach and Local Presence: Ensure the provider can conduct inspections globally with local teams. This is especially important for companies importing from regions like China.
- Technological Capabilities: Advanced tools and software enhance the efficiency and accuracy of inspections.
- Transparency and Communication: Clear and timely communication is essential for addressing issues and ensuring smooth operations.
How Certainty Enhances Pre-Shipment Inspections
Certainty offers comprehensive audit and inspection tools designed to streamline the inspection process. Key features and benefits include:
- Real-Time Data Collection and Analysis: Facilitates immediate identification of issues and decision-making.
- Comprehensive Reporting and Documentation: Provides detailed and accurate inspection reports.
- Integration with Quality Management Systems: Ensures seamless incorporation into existing workflows.
- Enhanced Compliance Tracking: Simplifies tracking and managing compliance with international standards.
Certainty’s solutions have been successfully implemented in various industries, improving the efficiency and reliability of pre-shipment inspections. These solutions have helped enterprises ensure that their products meet the highest quality standards and comply with all regulatory requirements.
To learn more about more about Certainty’s solutions and how we can benefit your risk management system, book a demo today.
You may also be interested in: