What is PSSR?
The Pre-Startup Safety Review (PSSR) is a critical component of process safety management (PSM), specifically designed to ensure the safe startup of new or modified industrial processes. This review systematically and thoroughly examines all safety aspects before any new facilities, equipment, or methods are put into operation.
The Evolution of PSSR
The practice of conducting PSSRs has evolved significantly over time, moving from a reactive measure to a proactive safety strategy. Initially, PSSRs were often performed only after a significant incident had occurred, serving as a post-incident analysis. However, as industries have recognized the high stakes involved in process safety, the PSSR has transformed into a critical preventive measure integrated into the early stages of project planning and execution.
This evolution has been driven by regulatory advancements, such as OSHA’s PSM standard (29 CFR 1910.119), which mandates PSSRs before the commissioning of new or modified processes. Modern PSSR practices incorporate advanced risk assessment tools like Process Hazard Analysis (PHA) and HAZOP (Hazard and Operability Study), ensuring a comprehensive identification and mitigation of risks. The shift from reactive to proactive PSSRs reflects a broader industry trend toward embedding safety into every phase of operations, enhancing both safety and sustainability.
Why PSSR is Critical
Importance in Preventing Accidents
In high-risk industries, the margin for error is often non-existent. PSSR is crucial for accident prevention because it identifies and addresses potential hazards before they can manifest into real-world incidents. This proactive approach to safety ensures that all safety systems, from emergency shutdown mechanisms to fire protection, are fully operational and meet the required safety standards before the process begins.
For example, in the chemical industry, where hazardous chemicals are prevalent, a PSSR might reveal that certain safety interlocks are not functioning as designed, which could prevent a catastrophic release of toxic substances. PSSR helps prevent accidents that could have severe consequences, including injuries, fatalities, environmental damage, and financial loss because it can catch these accidents early on. The rigorous application of the PSSR process ensures that all potential risks are mitigated, safeguarding both people and assets.
Ensuring Compliance with Safety Regulations
The pre-startup safety review is a key tool in ensuring that companies adhere to stringent safety regulations, such as those outlined by OSHA and the EPA. These regulations require thorough safety checks before any new or modified process can be put into operation, and PSSR serves as the final verification step in this process.
Through the PSSR, companies can demonstrate compliance with the Occupational Safety and Health Administration’s PSM standard, particularly the elements related to process safety information, management of change (MOC), and process hazard analysis (PHA). Moreover, PSSR documentation is often scrutinized during safety audits and investigations, making it essential for companies to maintain detailed and accurate records. Ensuring compliance through PSSR not only protects the company from regulatory penalties but also reinforces a culture of safety and accountability.
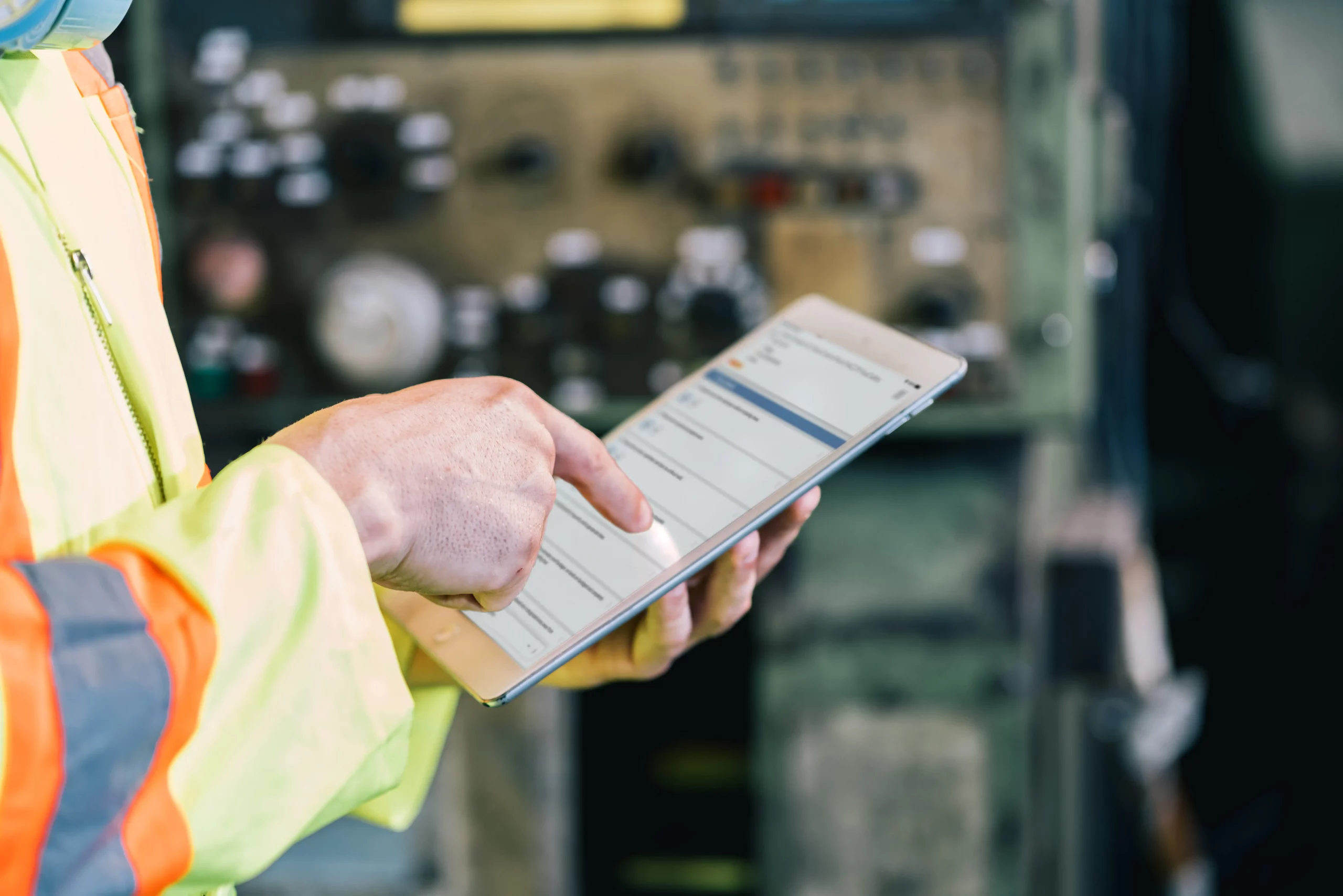
30+ Audit and inspection checklists free for download.
Key Components of a PSSR
Hazard Identification
One of the primary goals of a PSSR is to identify and assess potential hazards that could compromise the safety of the operation. Hazard identification is a meticulous process that involves reviewing all aspects of the process, including equipment design, operating conditions, and environmental factors. The PSSR team, typically comprising engineers, safety professionals, and maintenance personnel, utilizes various risk assessment tools such as HAZOP and Process Hazard Analysis (PHA) to systematically identify potential issues.
This component is crucial because it ensures that all possible risks are considered before the process begins. For instance, in an oil & gas facility, the hazard identification process might reveal that certain pipelines are susceptible to corrosion, posing a risk of leaks or explosions. Because risks were identified early, the PSSR team can recommend preventive measures, such as enhanced monitoring or the installation of additional safety barriers, ensuring that the operation starts on a solid safety foundation.
Safety Procedures Review
The review of safety procedures is another vital component of the PSSR. This step ensures that all operating procedures, maintenance procedures, and emergency procedures are clearly defined, up-to-date, and aligned with the specific requirements of the new or modified process. It’s not enough to have procedures in place—they must be rigorously evaluated to ensure they are effective in managing the identified risks.
During this review, the PSSR team examines whether the procedures are adequate for the safe operation of the process under various conditions, including normal operation, startup, and emergency shutdown scenarios. For example, if the PSSR reveals that the emergency shutdown procedures are outdated or unclear, this issue must be addressed immediately to ensure that in the event of an emergency, the response will be swift and effective. This thorough review process helps prevent accidents and ensures that all team members are prepared to act decisively in any situation.
Personnel Training
Even the best safety procedures are ineffective if the personnel responsible for executing them are not adequately trained. Therefore, personnel training is a critical aspect of the PSSR process, ensuring that every employee involved in the startup is fully aware of their responsibilities and capable of carrying them out safely. This training includes not only technical skills but also a deep understanding of safety protocols and emergency response procedures.
Continuous training is essential, particularly in industries where processes and technologies evolve rapidly. For instance, in the chemical industry, where new hazardous chemicals or processing techniques might be introduced, ongoing education ensures that operators remain competent in managing the associated risks. Investing in the training of each employee means companies can maintain high safety standards and ensure that their workforce is prepared to handle any challenges that arise during operations.
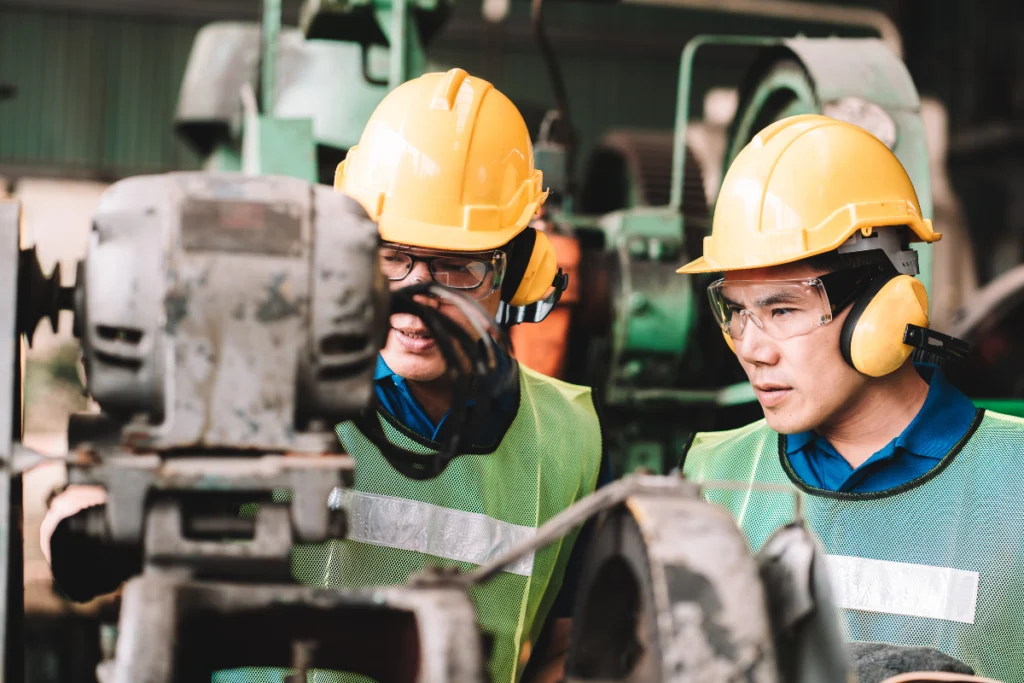
Documentation and Record-Keeping
Thorough documentation is indispensable in the PSSR process. This includes detailed records of hazard identification, safety procedure reviews, personnel training, and any corrective actions taken. Proper documentation serves multiple purposes: it ensures compliance with regulatory requirements, provides a reference for future PSSRs, and supports continuous improvement by allowing the organization to learn from past experiences.
Maintaining accurate and accessible records is also crucial for demonstrating compliance during audits or inspections. Tools like Certainty can help streamline this process by providing digital solutions for real-time data entry, automated checklist management, and comprehensive reporting capabilities. Through meticulous record keeping, companies can ensure that their PSSR processes are transparent, traceable, and aligned with best practices in safety management.
PSSR in Different Industries
PSSR in Manufacturing
In the manufacturing industry, PSSR is vital for ensuring that new machinery and production lines are safe. Manufacturing environments often involve complex, high-speed machinery that, if not properly vetted, can pose significant risks to operators and maintenance personnel. A PSSR in this context typically includes:
- detailed review of the machinery’s design specifications
- integration of safety features
- adequacy of operating and maintenance procedures.
Challenges in manufacturing often include the need to quickly bring new lines or equipment online to meet production demands. However, rushing the PSSR process can lead to overlooking critical safety issues. For example, a PSSR might reveal that a newly installed robotic arm lacks proper guarding, posing a risk of injury to workers. Addressing such findings before startup ensures equipment operates safely and efficiently, reducing downtime and avoiding potential accidents.
PSSR in Oil & Gas
The oil & gas industry presents unique challenges for PSSR due to the high-risk nature of its operations. Whether dealing with crude oil extraction, refining processes, or the maintenance of pipelines, the potential for catastrophic incidents is ever-present. PSSR in this industry is comprehensive, involving detailed reviews of all process safety information (PSI), including:
- mechanical integrity of equipment
- safety operating procedures
- effectiveness of emergency shutdown systems.
Real-world incidents, such as the Deepwater Horizon disaster, underscore the critical importance of robust PSSR processes in this sector. A well-conducted PSSR can identify weaknesses in process design, such as inadequate blowout preventers or insufficient emergency response plans, that could lead to major accidents. Addressing these issues before operations commence means companies can significantly reduce the risk of disasters, ensuring the safety of their personnel and the protection of the environment.
PSSR in the Chemical Industry
In the chemical industry, handling hazardous chemicals and complex chemical processes necessitates a rigorous PSSR process. The review ensures that all process changes, including the introduction of new chemicals or the modification of existing processes, do not introduce new risks. The PSSR checklist for chemical facilities often includes reviewing process hazard analyses (PHA), verifying the adequacy of safety interlocks, and ensuring that emergency procedures are communicated and understood by all personnel.
The stakes are particularly high in this industry because even small deviations from standard operating procedures can lead to significant safety incidents, such as chemical spills or explosions. The involvement of Health, Safety, and Environment (HSE) professionals is critical in the PSSR process to ensure that all potential hazards are identified and mitigated.
The PSSR Process: A Step-by-Step Guide
1. Pre-Planning Stage
The PSSR process begins with careful pre-planning. This stage involves:
- selecting the review team
- defining the scope of the review
- gathering all necessary documentation and resources.
The team should include representatives from various departments, such as engineering, safety, operations, and maintenance, to ensure a comprehensive review.
During this stage, it’s also important to establish clear objectives and timelines for the PSSR, ensuring that all stakeholders are aligned and prepared for the review process. Effective pre-planning sets the foundation for a successful PSSR by ensuring that all aspects of the review are thoroughly considered and well-coordinated.
2. Execution Stage
The execution stage is where the actual PSSR takes place. This involves:
- conducting on-site inspections
- reviewing safety procedures
- verifying personnel training
- documenting all findings.
During this stage, the team should systematically assess every aspect of the operation, identifying any potential hazards and ensuring that all safety measures are in place.
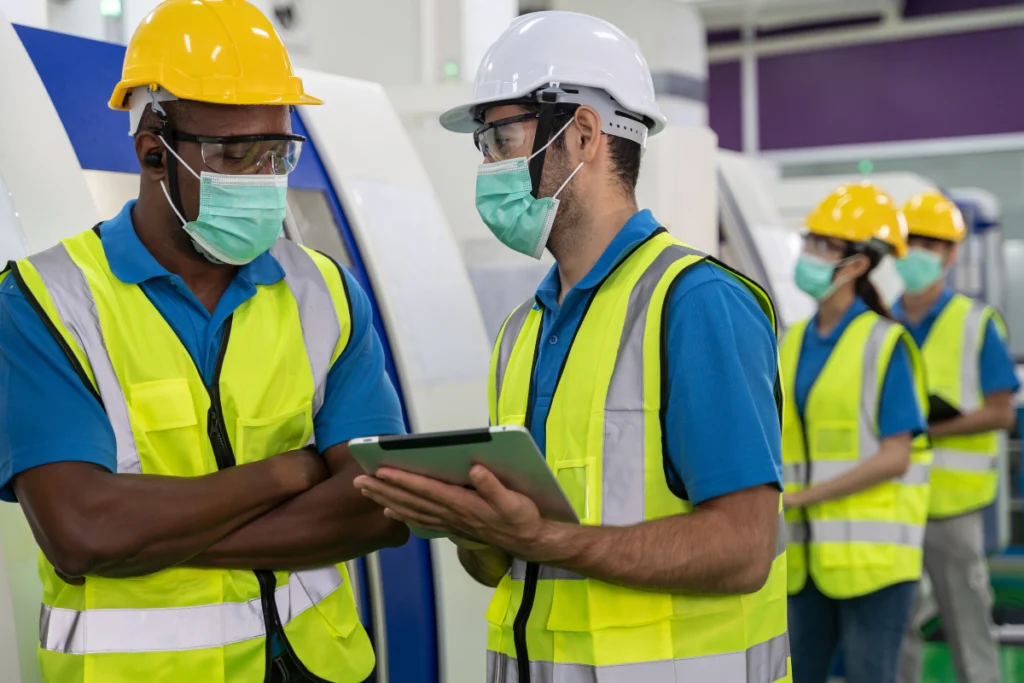
Documentation is a critical part of this stage, as it provides the evidence needed to verify that all safety requirements have been met. Any issues identified during the review should be addressed immediately, with corrective actions documented and implemented before the equipment or process is started.
3. Post-Review Stage
The post-review stage involves:
- follow-up actions
- continuous monitoring
- re-evaluation to ensure that all safety protocols remain effective over time.
This stage is critical for maintaining long-term safety and compliance, as it helps identify any emerging risks or changes in the operational environment that could impact safety.
Key activities in this stage include regular safety audits, updates to safety procedures, ongoing training for personnel, and periodic reviews of PSSR documentation. Maintaining a proactive approach to safety means organizations can ensure that their PSSR processes remain effective and responsive to changing conditions.
Common Challenges in Implementing PSSR
Resistance to Change
One of the most common challenges in implementing PSSR is resistance to change. This can stem from a variety of factors, including a lack of understanding of the PSSR process, concerns about the time and resources required, or simply a reluctance to adopt new practices.
Overcoming this resistance requires strong leadership, clear communication, and a commitment to safety from all levels of the organization. Providing education and training on the benefits of PSSR, as well as involving employees in the process, can help build support and reduce resistance.
Resource Allocation
Resource allocation is another significant challenge, particularly for smaller companies with limited budgets and personnel. Implementing a thorough PSSR process requires time, expertise, and financial investment, which can be difficult for some organizations to justify.
However, the costs of not implementing PSSR—such as accidents, regulatory fines, and damage to reputation—far outweigh the initial investment. To overcome resource challenges, companies can prioritize critical areas of their operations, allocate resources strategically, and seek out cost-effective solutions like digital tools to streamline the PSSR process.
Compliance Issues
Even with a robust PSSR process in place, companies may still face compliance challenges. These can arise from changes in regulatory requirements, differences in the interpretation of standards, or gaps in the PSSR process itself. Addressing compliance issues requires staying up-to-date with the latest regulations, conducting regular internal audits, and being prepared to adapt processes as needed.
Proactively engaging with regulatory bodies, seeking clarification on ambiguous requirements, and continuously improving the PSSR process can help mitigate these challenges. Maintaining open communication with regulatory agencies and involving them early in the planning stages of major projects can also help ensure compliance and avoid potential conflicts.
Best Practices for an Effective PSSR
Engage Cross-Functional Teams
Engaging cross-functional teams is crucial for a successful PSSR. By involving representatives from various departments—such as engineering, safety, operations, and maintenance—organizations can ensure that all aspects of the operation are thoroughly reviewed. This collaborative approach not only enhances the quality of the review but also promotes a culture of safety throughout the organization.
To facilitate effective cross-functional collaboration, it’s important to establish clear roles and responsibilities for each team member and encourage open communication. Regular meetings, feedback sessions, and joint problem-solving activities can help build strong working relationships and ensure that all team members are fully engaged in the PSSR process.
Use of Technology
The use of technology can significantly enhance the effectiveness of the PSSR process. Digital tools, such as those provided by Certainty, can streamline the PSSR process by automating checklists, facilitating real-time data entry, and enabling seamless communication among team members. These tools can also help with record-keeping, ensuring that all documentation is accurate, complete, and easily accessible.
Implementing technology in the PSSR process not only improves efficiency but also reduces the likelihood of human error.
Regular Updates and Training
Regular updates to PSSR protocols and ongoing personnel training are essential for maintaining high safety standards. As processes evolve and new technologies are introduced, it’s important to ensure that all safety procedures are up-to-date and that all employees are trained to handle any changes.
How Certainty Enhances PSSR
Certainty provides advanced digital solutions that enhance the PSSR process by automating the creation and management of checklists, records, and reports. These tools ensure that every aspect of the PSSR is thoroughly documented and that all action items are tracked and resolved on time. With Certainty, organizations can improve the accuracy, efficiency, and effectiveness of their PSSR processes.
Schedule a demo with our team today to improve your PSSR implementation with Certainty.
You may also be interested in: