Table of contents
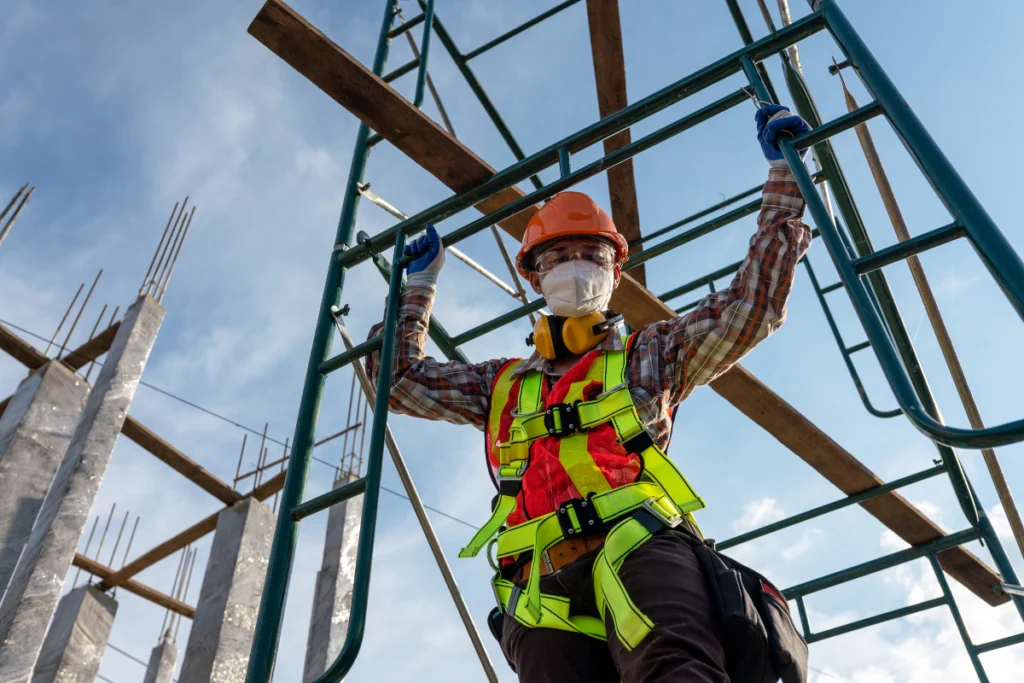
A Job Safety Analysis (JSA) is an essential tool in workplace safety, designed to identify and mitigate risks associated with specific tasks or jobs. This detailed guide will walk you through a comprehensive step-by-step process on how to perform a JSA, ensuring that you can confidently assess risks and implement controls to prevent workplace incidents. This guide aims to provide you with actionable insights that will serve as the cornerstone of your safety strategy.
What is Job Safety Analysis (JSA)?
A Job Safety Analysis (JSA), also known as a Job Hazard Analysis (JHA), is a systematic approach used to break down job tasks into individual steps, identify hazards at each stage, and implement measures to control or eliminate these risks. The primary purpose of a JSA is to make the job safer for the worker by proactively identifying potential risks before they result in accidents. Businesses that perform regular job safety analyses create a clear roadmap for how to complete a task safely, which ultimately contributes to a safer workplace culture and ensures compliance with regulatory standards.
How to Perform a JSA
Step 1: Identify the Job or Task to be Analyzed
The foundation of an effective JSA lies in selecting the right job for analysis. This critical first step often gets rushed, but taking the time to choose which tasks to analyze methodically ensures your safety efforts have the greatest impact.
Start by reviewing your workplace’s incident history over the past three to five years. Look beyond just the major accidents – pay close attention to patterns in near-misses and even seemingly minor injuries recorded in first aid logs. These patterns often point to underlying risks that need addressing.
When selecting tasks for analysis, prioritize based on:
- Accident history and near-miss frequency
- Tasks with the potential for severe injury or illness
- Newly established or modified procedures
- Complex jobs with multiple steps
- Routine tasks that may have become complacent
To bring structure to your selection process, gather key stakeholders – supervisors, experienced workers, and safety team members. Together, create a comprehensive list of all jobs in the work area. For each task, consider three key factors:
- Potential for injury
- Severity of potential harm
- Frequency of task performance
Practical Example: Risk Scoring
Comparing two tasks using a 1-5 scale for each factor:
Hydraulic Press Operation:
- Injury potential: 4
- Severity potential: 5
- Frequency: 3
- Total score: 4 x 5 x 3 = 60
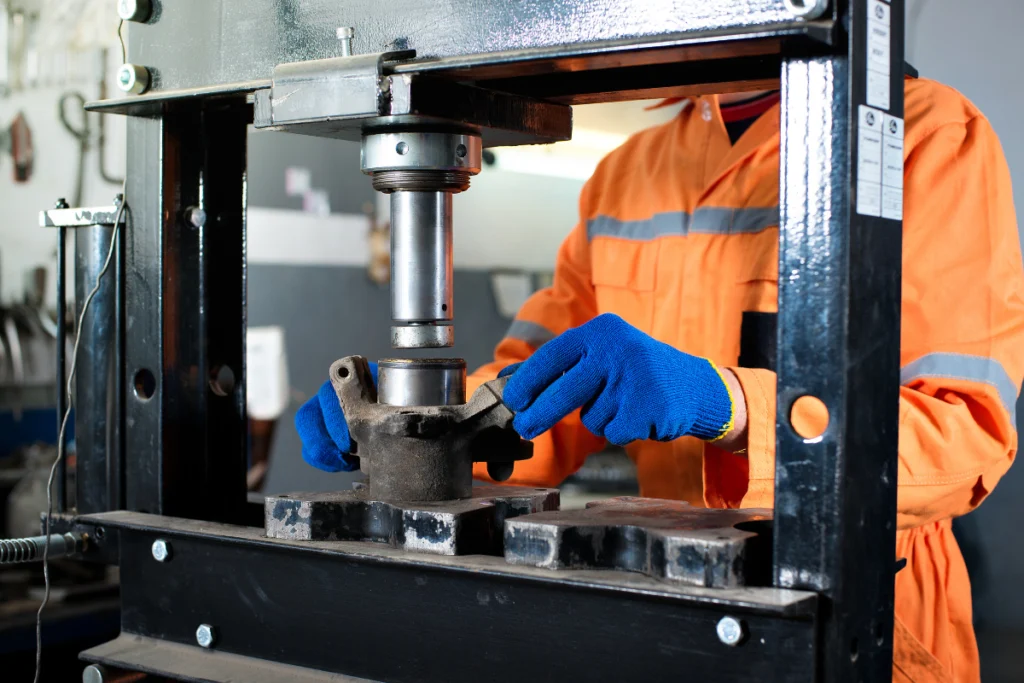
Manual Lifting Task:
- Injury potential: 3
- Severity potential: 2
- Frequency: 5
- Total score: 3 x 2 x 5 = 30
This scoring system helps prioritize which tasks to analyze first, focusing your efforts on where they’ll have the most impact.
Step 2: Break Down the Job into Sequential Steps
Now that you’ve selected your task, it’s time to dissect it into its component steps. Breaking down a job effectively requires both attention to detail and an understanding of the right level of granularity.
Begin by observing the task in action. Don’t just watch one worker – observe at least two or three experienced employees performing the same job. You’ll often notice variations in technique, and these differences can be illuminating. If possible, record the process on video (with workers’ consent, of course).
As you document the process, focus on finding the sweet spot in terms of detail:
Too general – “Operate machine.”
Just right – “Position material and start cutting.”
Too detailed – “Move right hand to the power switch, grasp switch with thumb and forefinger.”
Example: Breaking Down a Grinding Wheel Change
Here’s how to effectively break down a complex task:
- Pre-task preparation:
- Review the machine manual and specifications
- Gather the required tools and replacement wheel
- Notify nearby workers
- Safety measures:
- Lockout power source
- Verify zero energy state
- Wait for the wheel to stop completely
- Removal and replacement:
- Remove wheel guard
- Inspect replacement wheel
- Remove and replace the grinding wheel
- Clean mounting surfaces
- Completion and testing:
- Reinstall the guard and verify the security
- Remove lockout device
- Perform test run
After documenting steps, validate them with experienced workers. Ask key questions:
- “What happens before this step?”
- “Is there anything you do between these steps?”
- “Are there any unofficial ‘tricks’ you use?”
Step 3: Identify Potential Hazards for Each Step
With your steps clearly documented, it’s time for the heart of your job safety analysis: identifying potential hazards. This is where your analytical skills really come into play, as you need to think both broadly and deeply about what could go wrong at each step.
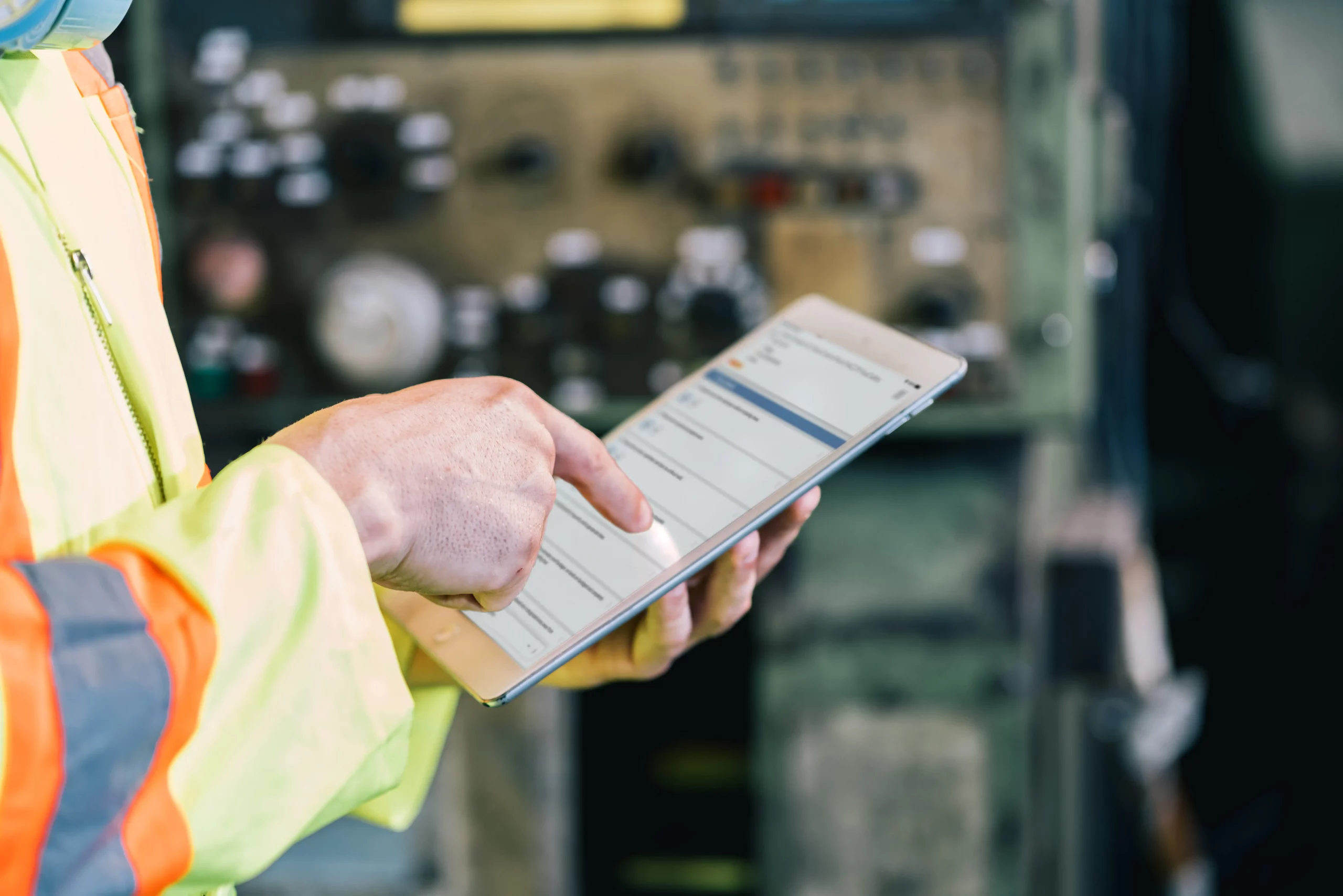
30+ Audit and inspection checklists free for download.
Think of hazard identification as putting on different pairs of glasses, each allowing you to see the task from a different perspective:
- Energy Analysis Perspective Consider all types of energy present:
- Kinetic (moving parts)
- Potential (lifted loads, springs)
- Electrical
- Thermal
- Chemical
- Task Factors Perspective Examine the broader context:
- Tools and equipment
- Work environment
- Time pressures
- Physical demands
- Concurrent operations
- Human Factors Perspective Think about the human element:
- Fatigue and time of day
- Experience and training
- Physical capabilities
- Stress and distractions
Practical Example: Grinding Wheel Removal Hazards
Let’s analyze the hazards in our grinding wheel example:
Physical Hazards:
- Sharp edges causing cuts
- Falling wheel causing foot injury
- Awkward posture leading to strain
Less Obvious Hazards:
- Stored energy from wheel momentum
- Poor lighting affecting visibility
- Metal dust exposure
- Tool slippage or improper tool use
Explore our library of free-to-download safety checklists to help with your hazard identification efforts.
Step 4: Develop Preventative or Control Measures
Now comes the crucial part – transforming your hazard analysis into actionable safety measures. This isn’t just about slapping on some PPE and calling it a day. Effective hazard control requires a thoughtful, hierarchical approach.
The Hierarchy of Controls:
- Elimination Can you completely remove the hazard? Example: Automate a dangerous manual process
- Substitution Can you replace the hazard with something safer? Example: Using lower-voltage electrical systems
- Engineering Controls How can you isolate people from the hazard?
- Machine guarding
- Ventilation systems
- Sound enclosures
- Light curtains
- Administrative Controls How can you change the way people work?
- Robust procedures
- Training programs
- Warning signs
- Buddy systems
- Personal Protective Equipment (PPE) Your last line of defense. Note: Be specific in PPE requirements
Example: Controlling Grinding Wheel Hazards
For the hazard of cuts from sharp edges:
- Engineering Control: Design and implement a wheel removal tool
- Administrative Control: Develop specific removal procedures
- PPE: Cut-resistant gloves (EN 388 level 4)
For metal dust exposure:
- Engineering Control: Local exhaust ventilation
- Administrative Control: Establish maximum exposure times
- PPE:
- N95 respirator
- Disposable coveralls
Step 5: Implement, Monitor, and Review
Your JSA journey doesn’t end with documenting controls – now comes the crucial phase of bringing it all to life. Implementation is where your careful analysis transforms from a document into actual safer practices on the shop floor.
Key Implementation Steps:
- Create clear, user-friendly documentation
- Develop comprehensive training programs
- Communicate effectively about new procedures
- Establish regular monitoring protocols
Monitoring should include:
- Daily supervisor observations
- Weekly safety team spot-checks
- Monthly comprehensive audits
Track these key metrics:
- Incident rates
- Near-miss reports
- Compliance rates
- Worker feedback
Review your JSA:
- Annually at minimum
- After incidents or near-misses
- When processes change
- When new equipment is introduced
Remember, a truly effective JSA is never really finished. It’s a living document that evolves as your workplace does, always striving to create the safest possible environment for your workers.
Is JSA Required by OSHA?
One common question that arises among safety professionals is whether a Job Safety Analysis (JSA) is explicitly required by OSHA (Occupational Safety and Health Administration). The answer is nuanced: while OSHA does not explicitly mandate the use of JSAs for all workplaces, it strongly recommends them as a best practice in identifying and controlling workplace hazards.
OSHA’s guidelines emphasize the importance of proactive hazard identification through processes like Job Hazard Analysis (JHA), which is essentially another term for JSA. OSHA standards require employers to assess workplace hazards and implement preventive measures to reduce the risk of injury, which directly aligns with the goals of the JSA process.
Relevant OSHA Standards Related to JSA:
- OSHA 1910.132 (Personal Protective Equipment – General Requirements): Employers must perform a hazard assessment to determine if PPE is required, a step that is often conducted as part of a JSA.
- OSHA 1910.147 (Control of Hazardous Energy – Lockout/Tagout): Requires the identification of hazards and implementation of energy control procedures, which can be effectively developed through a JSA.
- OSHA 1910.269 (Electric Power Generation, Transmission, and Distribution): Mandates hazard assessments and safe work procedures, both of which can be supported by JSAs.
Why Implementing JSAs is a Best Practice
While not always required by OSHA, incorporating JSAs into your safety program is a proactive way to comply with OSHA’s general duty clause, which states that employers must provide a workplace free from recognized hazards that could cause death or serious harm. By performing JSAs, you not only enhance your occupational safety efforts but also strengthen your compliance with OSHA’s safety standards and regulations.
Practical Impact: Organizations that implement JSAs regularly are better equipped to identify hazards, develop effective hazard controls, and foster a safety culture that prioritizes risk management. Even if not explicitly required, a well-implemented JSA process can significantly reduce workplace injuries, support regulatory compliance, and create a safer, more productive work environment.
Common Challenges and Solutions in Conducting a JSA
Even with a well-structured plan, challenges can arise during the JSA process. These might include resistance from employees, incomplete hazard identification, or inconsistent follow-through on safety measures.
Solutions to common challenges:
- Engage Leadership: Get leadership actively involved to set the tone for a safety-first culture.
- Create Awareness: Regularly communicate the importance of JSAs to all employees, emphasizing how it benefits their safety.
- Simplify the Process: Make the JSA process as straightforward as possible to encourage active participation and consistent use.
How Certainty Supports Your JSA Efforts
Certainty offers comprehensive tools to streamline the JSA process, from hazard identification to monitoring safety controls. It simplifies the documentation process and automates key tasks, making it easier for safety managers to focus on proactive safety measures.
Features of Certainty:
- Automation of JSA Documentation: Certainty’s Vision and Insights machine-learning tools automatically complete and extract actionable information from your safety checklists, saving time and reducing the likelihood of errors. This automation ensures that your JSA documentation is thorough, consistent, and ready for immediate use.
- Data Analytics: Our platform provides advanced reporting that easily communicates your safety data to identify trends, uncover potential risks, and support continuous process improvements. This enables your team to make informed decisions based on real-time insights, enhancing overall workplace safety.
- Regulatory Compliance Support: Certainty helps ensure that all JSA activities align with current OSHA safety standards and industry best practices, keeping your organization compliant and prepared for audits or inspections.
Certainty’s tools are designed to not only streamline the JSA process but also to foster a culture of continuous improvement. Leveraging the power of machine learning and data-driven insights empowers safety managers to create safer, more efficient workplaces while staying ahead of regulatory requirements.
For those looking to take their JSA to the next level, explore Certainty’s innovative solutions to simplify and enhance your safety management processes. Request a demo today to see how we can help you lead your organization to a safer future.
You might also be interested in: