Risks are naturally associated with manufacturing and industrial operations. In 2020 alone, private industry employers reported 2.7 million nonfatal workplace injuries, according to the U.S. Bureau of Labor Statistics.
As a result, it’s in a company’s best interest to mitigate risks — and their potentially negative outcomes — wherever possible. To accomplish this goal, organizations often conduct quantitative risk assessments that leverage data about existing processes and procedures to pinpoint potential problems.
But on their own, quantitative risk evaluation only tell half the story. Paired with qualitative risk assessments of employees’ risk perception, meanwhile, companies can both boost staff safety and reduce overall risk. Here’s how.
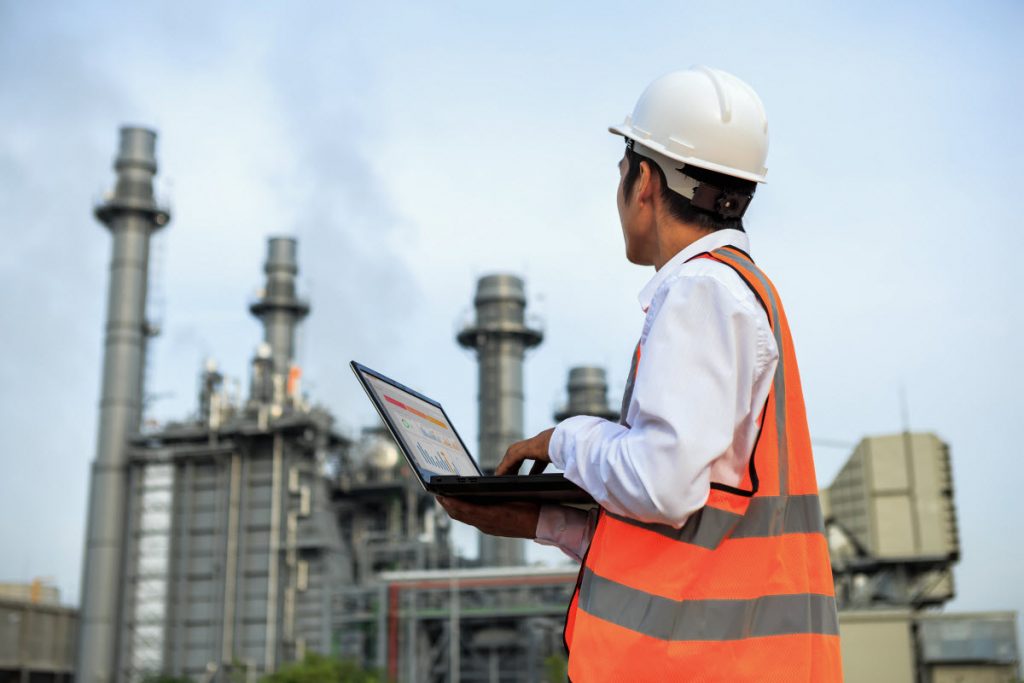
What is a Qualitative Risk Assessment?
A qualitative risk assessment focuses on employees’ perception of risk around specific activities or expectations. Discussions with multiple employees allow companies to “score” risks based on both perceived severity and the likelihood of the potential consequence.
The goal of a qualitative risk assessment is to create rating scales of potential risks based on actual user experience and develop comprehensive risk management strategies. The commonality of experience suggests that the risk is largely universal, while widespread worry about the severity of the risk indicates that it’s not simply an inconvenience — left unchecked, it could derail operational performance.
Qualitative vs Quantitative Risk Assessment
Where a qualitative risk assessment focuses on perception, a quantitative risk analysis leverages data to determine overall risk. For example, a quantitative assessment might use data about machine failure rates per hour or per part produces to determine the probability of occurrence and the likelihood of production stoppages or slowdowns, whereas a qualitative assessment would ask employees and other stakeholders about their perceived experience with the same machine.
If both qualitative and quantitative assessments indicate the probability of the risk is high, it’s worth taking the time to investigate and remediate the concern.
When Should These Assessments be Used?
Qualitative risk assessments are often used at the start of new projects to create a list of risks that could undermine overall performance. By providing staff with information about key project deadlines, deliverables, and the processes required to achieve these goals, project managers can gain valuable feedback that helps prioritize resource allocation to deliver reduced risk.
Consider a project that involves the manufacture, packaging, and shipping of specific goods. A qualitative risk analysis process might reveal widespread concern around certain aspects of the packaging process such as inadequate space, high complexity, and low margin for error that could lead to both production line backups and potential injury. Armed with this information, project managers can allocate resources to address this issue before the project gets underway.
Quantitative assessments, meanwhile, might show high failure rates for a specific piece of machinery on the production line. While it may not have been mentioned by team members during qualitative assessments since the failure is easily corrected with stopgap processes and functional know-how, the time added to the overall production run could derail project timelines, meaning it may be worth spending the money to fix the issue fully before the project starts in earnest.
Best Practices for Quantitative and Qualitative Risk Assessments
While quantitative and qualitative risk assessments have different outcomes, they share similar best practice methodologies for effective project risk management.
Identify key risks
First, companies must identify key risks in the organization. Common strategies here include the use of process safety audits and quality assurance audits and inspections. Using either in-house templates and checklists or those provided by online audit providers, companies can streamline the process of pinpointing risks by allowing auditors to focus their attention on key processes and policies.
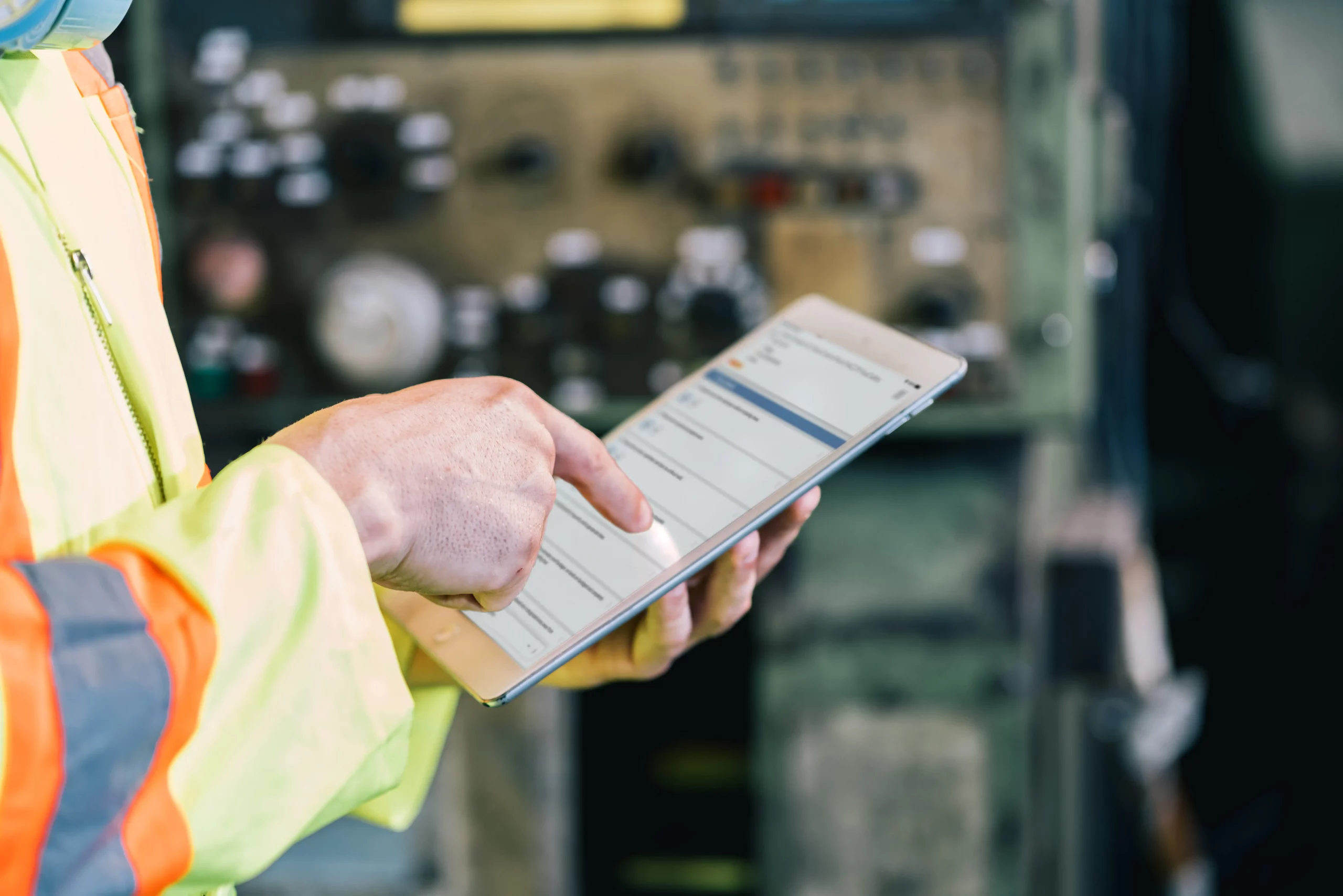
30+ Audit and inspection checklists free for download.
Classify risk impact
Next, companies must classify risk on an impact scale as low, medium, or high based on the likelihood of the risk occurring and its potential results. Consider a high-value, high-throughput piece of machinery that staff report as unreliable and data shows as due for replacement within the next year. Given both perceptive and practical risk information, it may be worth replacing the machine early to avoid the potential impact of risks on project objectives.
Develop risk response
Once risks are classified, companies must prioritize those defined as high risk and develop risk responses for each one, then move down the list to medium and finally low-risk operations. While low-risk concerns may not be addressed for weeks — or months — having a plan in place allows businesses to see how far they’ve come and what they have left to do.
Regularly monitor these risks
Risks don’t simply vanish because they’ve been initially addressed. As a result, it’s worth conducting qualitative and quantitative analysis at the beginning of a new project, at the midpoint, and when the project is completed to evaluate risk change over time and determine if further process improvements are necessary.
Quality and Quantity: The Best of Both Worlds
In isolation, qualitative and quantitative assessments only tell half the story. One provides the perception of risk from workers’ perspective, while the other provides clear data about potential failure rates of identified risks. Using either type in isolation provides valuable information but is missing the larger context: Data indicating physical failures may be offset by staff knowledge, while employees’ perception of risk may not be tied to collected data.
Combining quality and quantity gives companies the big picture by creating a risk assessment matrix. By identifying risks that are both worrisome to employees and are backed up by collected data, organizations can effectively allocate resources to deal with critical concerns and help drive project success.
Combine quality and quantity to reduce your risk with Certainty. Let’s get started.
You may also be interested in:
Reduced Risk, Increased Resiliency: The Advantage of Supply Chain Management Tools