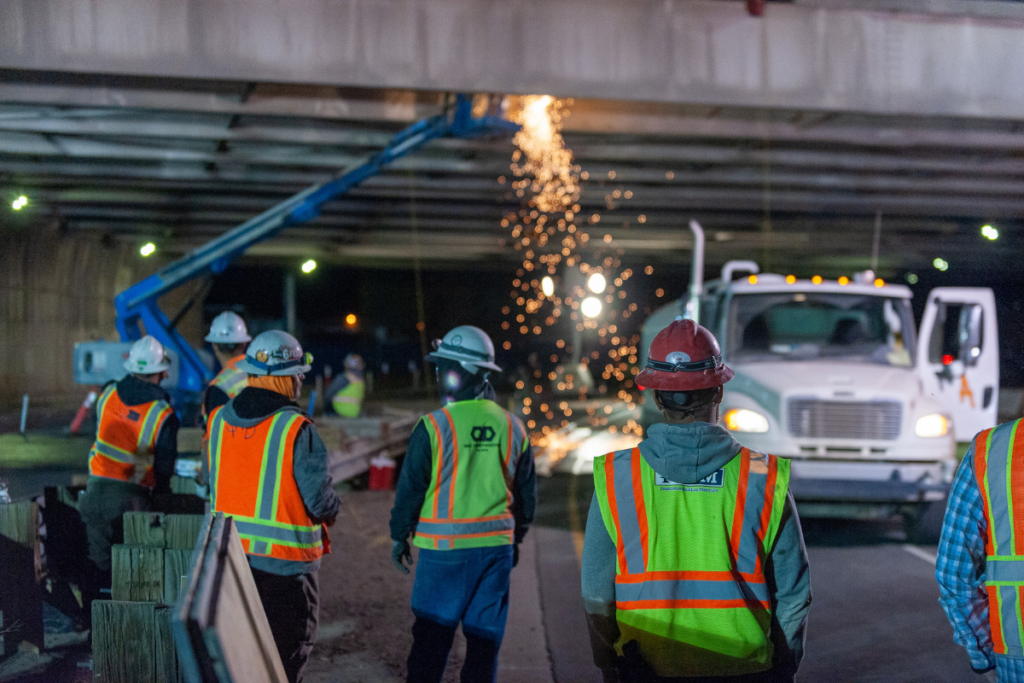
What is Industrial Hygiene?
Industrial hygiene is the science dedicated to preserving and protecting worker health and safety by identifying, evaluating, and controlling environmental hazards in the workplace. It involves managing a wide range of occupational hazards such as chemical, biological, physical, and ergonomic stressors. Essentially, industrial hygiene aims to anticipate and mitigate factors that could cause harm or discomfort to workers, ensuring their well-being.
The Importance of Industrial Hygiene in the Workplace
Maintaining a robust and effective industrial hygiene program usually results in fewer accident and illness reports, and increases productivity and employee satisfaction. In addition, businesses comply with regulatory bodies such as OSHA regulations; ultimately avoiding legal penalties and fostering a positive corporate image, contributing to business success.
The Core Principles of Industrial Hygiene
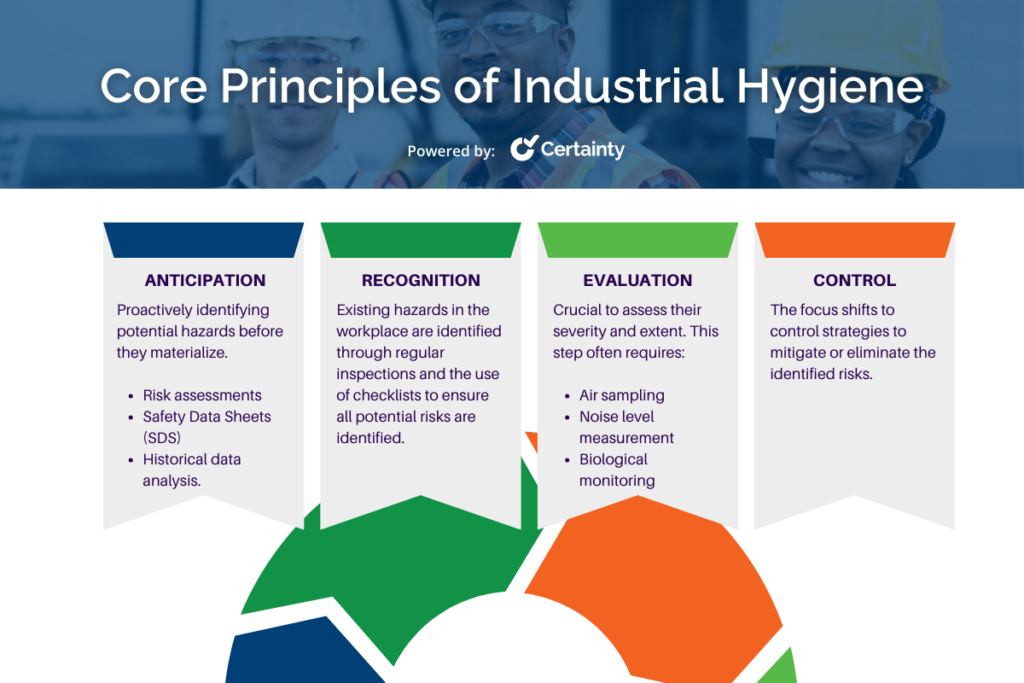
Anticipation
The first principle for effective industrial hygiene is anticipation. Anticipation involves proactively identifying potential hazards before they materialize. It requires a thorough understanding of workplace operations and the associated risks. For instance, in a chemical manufacturing plant, industrial hygienists might anticipate hazards by examining processes involving volatile organic compounds (VOCs) and predicting possible exposure scenarios.
Tools used in anticipation include:
- Risk assessments
- Safety Data Sheets (SDS)
- Historical data analysis
Recognition
Once potential hazards are anticipated, the next core component is recognition. Here, existing hazards in the workplace are identified through regular inspections and the use of checklists to ensure all potential risks are identified.
Common industrial hazards include:
- Chemical Hazards: Exposure to toxic substances, solvents, heavy metals, and vapors.
- Physical Hazards: Noise, radiation, and extreme temperatures.
- Biological Hazards: Pathogens, allergens, and biohazardous materials.
- Ergonomic Hazards: Repetitive motions, poor posture, and poorly designed workspaces.
Effective recognition relies on the expertise of certified industrial hygienists (CIH) who can accurately identify and categorize these hazards.
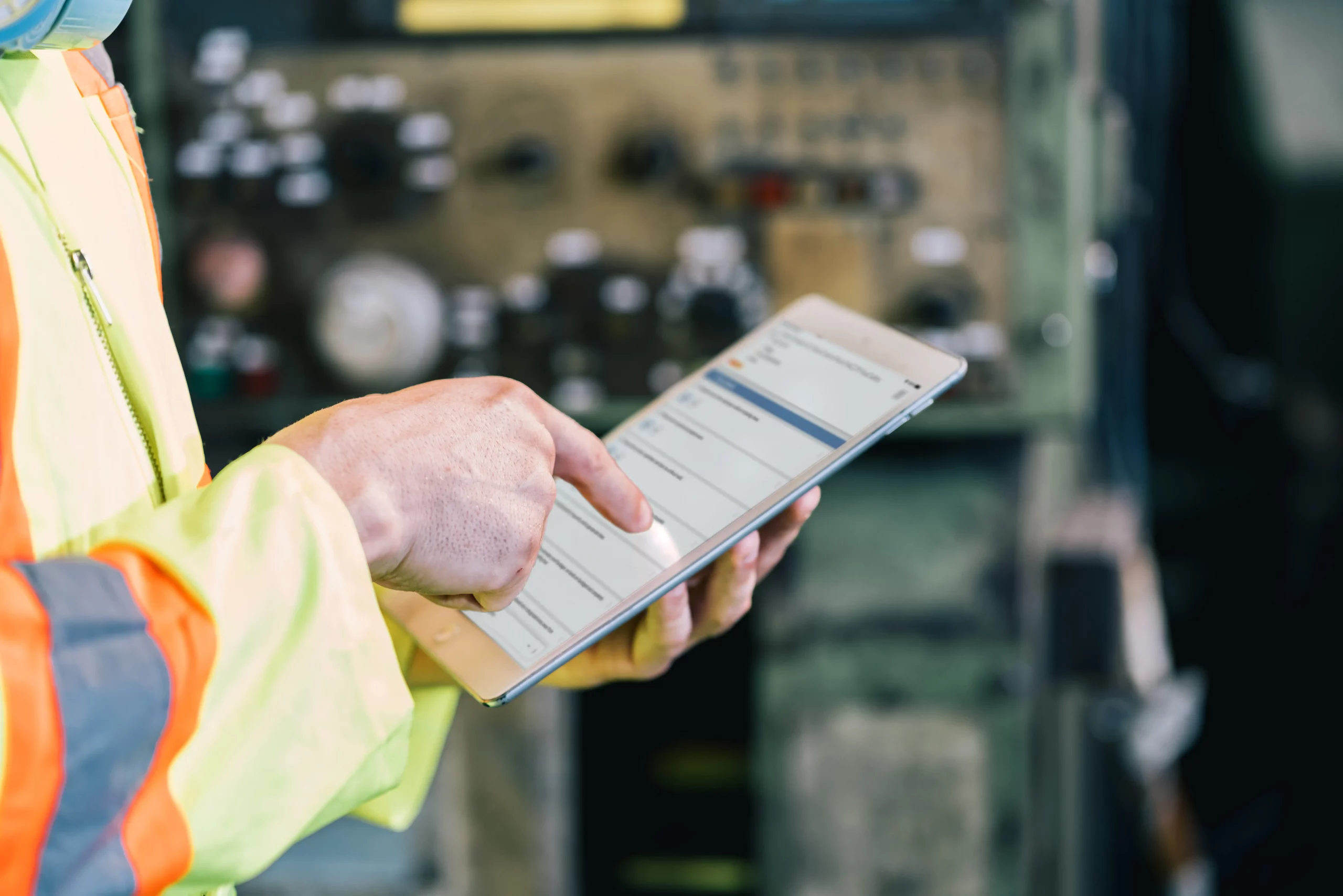
30+ Audit and inspection checklists free for download.
Evaluation
Following the recognition of hazards, evaluation is crucial to assess their severity and extent. This step often requires quantitative measures such as:
- Air sampling
- Noise level measurement
- Biological monitoring
Advanced analytical methods and tools, like gas chromatographs and dosimeters, provide accurate data on exposure levels. For example, an exposure assessment might reveal that workers are exposed to asbestos fibers above the permissible exposure limit, necessitating immediate remediation.
Control
After evaluating the hazards, the focus shifts to control strategies to mitigate or eliminate the identified risks. The hierarchy of controls provides a structured approach:
- Elimination: Removing the hazard entirely, such as discontinuing the use of a harmful chemical.
- Substitution: Replacing a hazardous substance or process with a safer alternative.
- Engineering Controls: Implementing physical changes to the workplace, such as installing ventilation systems.
- Administrative Controls: Changing work practices or policies, such as rotating shifts to reduce exposure time.
- Personal Protective Equipment (PPE): Providing gear like gloves, masks, and goggles to protect workers from hazards.
Key Elements of an Industrial Hygiene Program
Worksite Analysis
Conducting a comprehensive analysis of the worksite forms the foundation of every industrial hygiene program. This includes thorough inspections to pinpoint potential hazards and evaluate the effectiveness of current control measures. Consistent monitoring and assessment are essential to adapt to evolving work environments and emerging risks. It’s vital to prioritize maintaining good indoor air quality during worksite analysis, as poor air quality can result in respiratory issues and decreased productivity.
Hazard Prevention and Control
Creating efficient strategies for prevention is crucial in upholding workplace safety. This includes developing customized control measures based on the hazards identified in the worksite analysis. Implementing these measures and ensuring their continuous effectiveness requires consistent monitoring and adjustments when necessary. For example, if noise levels surpass safe thresholds in a factory, the installation of soundproofing materials and the provision of hearing protection to workers can significantly mitigate the risk of hearing impairment.
Health Surveillance
Health surveillance is an essential component of an industrial hygiene program. Monitoring the health of workers through regular check-ups and medical surveillance programs can detect early signs of occupational diseases, allowing for timely intervention. This proactive approach not only protects workers but also provides valuable data on the effectiveness of control measures. Health surveillance programs should be designed to address the specific risks present in the workplace, ensuring that workers are monitored for conditions relevant to their exposures.
Training and Education
Providing comprehensive training to employees about potential hazards and safe work practices is essential. Continuous education programs help keep workers informed about new hazards and the latest control methods. This ongoing education fosters a culture of safety within the organization, where workers feel empowered to contribute to a safe working environment. Training should be practical and engaging, incorporating hands-on demonstrations and real-life scenarios to ensure that employees fully understand and retain the information.
What are the Common Industrial Hygiene Hazards?
Chemical Hazards
Chemical hazards are a significant concern in many industries. They include exposure to:
- Toxic substances;
- Solvents;
- Heavy metals;
- Vapors
Managing these risks involves:
- Proper labeling and storage of chemicals;
- Using ventilation systems to reduce airborne contaminants;
- Providing PPE such as gloves and respirators;
- And implementing spill containment procedures.
According to OSHA, proper management of chemical hazards can prevent over 500,000 illnesses and injuries each year in the United States alone.
Physical Hazards
Physical hazards, such as noise, radiation, and extreme temperatures, require specific control measures to protect workers. To better manage noise hazards, businesses can install soundproofing materials and provide hearing protection. As for radiation risks, these can be mitigated by using shielding and limiting exposure time. And finally, for temperature extremes, climate control systems and appropriate clothing are essential.
Biological Hazards
Biological hazards, including pathogens and allergens, are particularly relevant in industries like healthcare. Managing these hazards involves maintaining high standards of hygiene and sanitation, providing vaccinations where applicable, using PPE such as gloves and masks, and conducting regular health monitoring to detect early signs of exposure. Effective management of biological hazards is crucial to prevent the spread of infectious diseases and protect worker health.
Ergonomic Hazards
Ergonomic hazards are associated with repetitive strain injuries and poor workplace design. Mitigating these risks involves conducting ergonomic assessments to identify risk factors, redesigning workstations to improve posture and reduce strain, providing ergonomic tools and equipment, and training workers on proper body mechanics and techniques to reduce strain.
Regulatory Framework and Compliance Relating to Industrial Hygiene
OSHA Standards and Guidelines
The Occupational Safety and Health Administration (OSHA) sets comprehensive regulations related to industrial hygiene. Employers must comply with these standards to ensure a safe working environment. Key requirements include:
- Conducting regular hazard assessments;
- Providing necessary PPE;
- Maintaining accurate records of workplace injuries and illnesses;
- And implementing training programs to educate workers on safety practices.
International Standards
For multinational companies, compliance with international standards is crucial. Organizations like the International Labour Organization (ILO) provide guidelines that often align with OSHA regulations but may include additional requirements. Ensuring global compliance helps protect workers across all locations and supports a unified approach to health and safety.
Certainty’s Connection to Industrial Hygiene Management
Certainty is a leading audit and inspection management platform designed to support enterprise health and safety management. Our mission is to provide organizations with the tools needed to ensure compliance and promote worker safety effectively. Certainty helps manage various aspects of industrial hygiene, from risk assessments to health surveillance.
Features Relevant to Industrial Hygiene
Certainty offers a suite of features tailored to support industrial hygiene programs:
- Real-Time Monitoring: Allows for immediate detection of hazards and enables swift response, helping to prevent accidents before they occur.
- Risk Assessment Tools: Facilitates thorough risk assessments, identifying potential hazards and determining appropriate control measures.
- Incident Reporting: Simplifies the process of reporting and tracking workplace incidents, ensuring timely resolution and compliance with regulatory requirements.
- Auditing and Inspections: Streamlines the process of conducting audits and inspections, helping to maintain compliance and improve safety practices.
Interested in learning more about Certainty? Book a demo with our team today for a personalized walkthrough.
You might also be interested in: