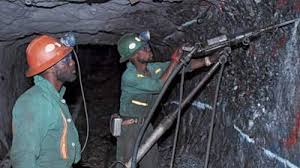
The key purpose of this blog series is to help ‘cross-fertilize’ ideas and opinions from one industry sector to another. This week we’re looking at the mining sector and reflecting on some of the challenges presented there. We found this great article in support of checklists and recommend you read it in full here, – my point is you may recognize this point of view in your own business and the full article may well help you. We’ve summarised a key issue affecting the mining sector raised by Check-6, here:
Knowledge is learned. And since humans are not perfect, failing plays a key role in the learning curve. Trial and error exercises, collaboration, brainstorming, and creative endeavors encourage and embrace failure, which conversely spawns progress.
However, there are industries where failure is not an option and procedural discipline is essential to save lives. Commercial and military aviation, nuclear power, and mining are such industries necessitating performance in high-hazard environments. The mining industry should be heralded as such an industry but has, apparently, woefully fallen short.
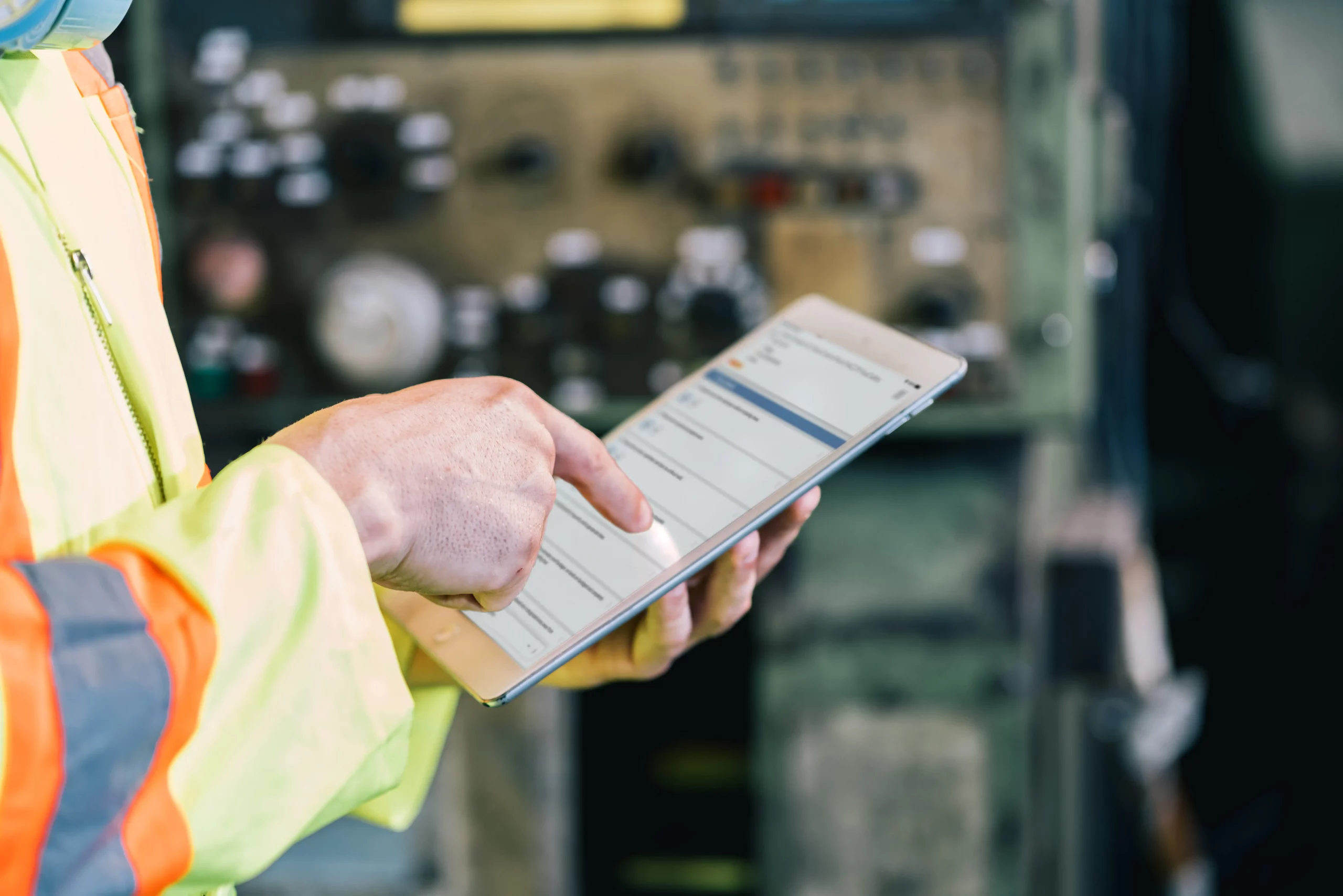
30+ Audit and inspection checklists free for download.
During the extraction, processing, and manufacturing phases, critical tasks are routinely performed with the mentality of “I think” rather than “I know.” After judiciously learning from a procedures manual, miners have no doubt performed the same tasks a multitude of times with repeatable success. Still, people operate mining sites, processing, and manufacturing plants: memories fail and moods swing – human factors can cause even the most experienced operator to have a lapse in judgment or decision-making.
Supervisors and crewmembers who rely on experience to perform high-risk tasks, during normal operations and in emergency situations, often find themselves, knowingly or unknowingly, in the danger zone, far removed from the complexity of procedures manuals. It is during these moments that critical tasks become susceptible to errors that cause Lost Time Incidents (LTI), an increase in Total Reportable Incident Rates (TRIR), downtime, longer flat time, and increased Non-Productive Time (NPT)…
An organization’s absolute best mechanism to prevent human error is to instill a checklist culture. Applied with rigor in various vertical industries such as medical, commercial aviation, and nuclear power, checklists have proven to be essential to the successful implementation of standards. There are many types of checklists based on styles that are in turn based on specific sets of circumstances and needs. However, keep in mind the tangible checklists so often energetically engaged as the end all are merely the beginning, as they are inanimate tools waiting to be implemented. The heartbeat of any mature checklist culture is disciplined human behavior motivated by management’s ability to verify compliance that instills trust among colleagues.
Furthermore, trust is key as a communal discipline allows supervisors and their subordinates to follow a standardized set of company-based procedures, written by boots-on-the-ground with real-world experiences, rather than a chain-of-command hierarchy based on experience learned 20 years ago from a manual, or worse, the previous supervisor. Teamwork is a by-product of reliability and consistency. A checklist culture is a reliably consistent team of individuals who communicate with each other across the enterprise in familiar language and operate in near-perfect rhythm to complete assigned tasks – precisely, safely, and calmly.
Want to learn more about Certainty Software? Click here.