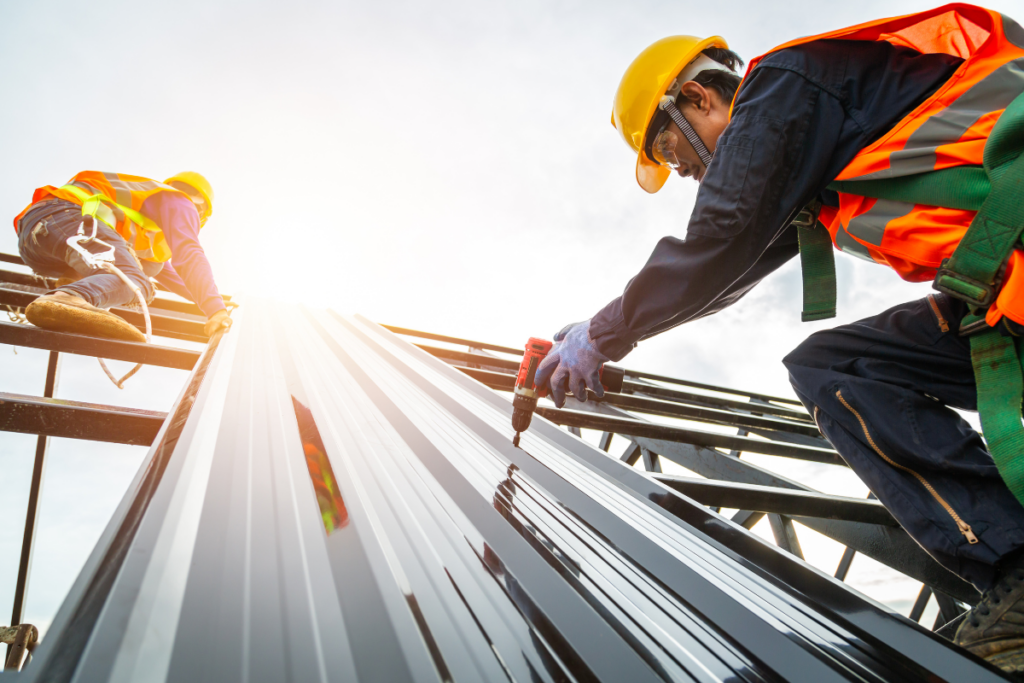
On December 11, 2024, the Occupational Safety and Health Administration (OSHA) announced its final rule on an updated personal protective equipment (PPE) standard for the construction industry. This long-awaited revision mandates that employers provide properly fitting PPE to ensure better protection for construction workers, addressing a critical gap in workplace safety regulations.
Set to take effect on January 13, 2025, the new standard aligns with the PPE requirements already in place for the general industry under Subpart E of OSHA’s safety standards.
Let’s take a look at the key changes in the revised standard. We will also discuss the possible reasons behind the update and the potential impact on construction employers, workers, and stakeholders nationwide.
Why Change Was Necessary
The construction industry remains one of the most hazardous fields of employment. In 2022, 1,069 U.S. construction workers lost their lives—more than any other industry. These fatalities are a stark reminder of the persistent workplace hazards in construction, from falls and head injuries to exposure to health hazards like dust and debris. Behind these numbers are real people: colleagues, friends, and family members who could have been protected by proper safety measures.
Personal protective equipment in construction is one of the most critical defences against these risks. When used effectively, PPE prevents nearly 40% of workplace injuries and diseases. Yet, improperly fitting PPE remains a widespread issue, leaving workers—especially affected employees like women and larger workers. For example, in a survey by JJ Kellar, 85% of women in construction responded that ill-fitting PPE has hindered their ability to work safely. Over 58% of women in other surveys have said they wear protective clothing or equipment, such as vests, that is the wrong size. And 34% of workers in general struggle to find PPE that fits. These findings highlight why OSHA’s rulemaking process prioritized the need for PPE with a proper fit.
This proposed change, now finalized, ensures that no worker—regardless of size, gender, or role—is forced to compromise between performing their job and staying safe. It’s a step forward in addressing the gaps left by standard-sized PPE, which often fails to provide adequate protection for workers with varying needs.
Exploring the Revised Standard
With the final rule now in place, OSHA has taken a significant step toward improving worker safety across the construction industry. The revised standard targets issues that have long plagued stakeholders, including employers, unions, and safety advocates.
Key Aspects of the Revised Standard
- Explicit Fit Requirement: Codified at 29 CFR Part 1926.95(c), the update requires that construction employers ensure PPE fits each worker properly. This addresses the issue of poor fit and reinforces the necessity of a proper fit for effective protection.
- Alignment Across Industries: Now that OSHA has harmonized construction PPE standards with those in general industry and national consensus standards, it is ensuring consistent protections across sectors, reducing confusion and improving compliance.
- Addressing Fit Challenges: The rule acknowledges that standard-sized PPE often fails to meet the needs of smaller or larger workers, particularly women. The emphasis this standard now places seeks to eliminate risks associated with ill-fitting equipment
You can read the full OSHA Construction PPE Standard revision final ruling here.
Implications for Employers
The revised PPE standard represents a significant shift in how employers approach worker safety. It’s no longer sufficient to simply provide personal protective equipment. Employers must now ensure that PPE fits properly and is suited to the unique needs of each worker. This change acknowledges that ill-fitting PPE not only undermines its effectiveness but also erodes worker confidence in workplace safety measures.
For employers, this means rethinking their current processes for selecting, distributing, and inspecting PPE. A proactive approach to compliance—one that includes assessing the specific requirements of the workforce—can help reduce workplace hazards, improve productivity, and build trust with employees. Beyond meeting OSHA’s requirements, these efforts demonstrate a commitment to the well-being of all workers. This in turn fosters a culture of safety and responsibility.
- Assessment and Provision: Employers must assess the fit of all PPE—including harnesses, hard hats, and protective clothing—to ensure every piece provides adequate protection.
- Training and Documentation: Organizations will need to train personnel on selecting and distributing PPE, as well as maintain inspection records to comply with OSHA’s updated standards. This may also reduce the risk of citations from OSHA inspections.
Take Safety Further with Certainty Software’s PPE Inspection Checklist
To help businesses meet the updated PPE standards and protect their workforce, Certainty Software offers a PPE Inspection Checklist. This is a powerful tool to ensure compliance and enhance safety practices.
This comprehensive checklist is designed to help employers:
- Evaluate PPE Fit: Ensure all equipment fits properly, reducing risks associated with ill-fitting gear.
- Inspect PPE Condition: Identify damaged or worn-out equipment before it becomes a hazard.
- Simplify Documentation: Keep thorough records of inspections to demonstrate compliance with OSHA’s revised standards.
With an easy-to-use format and actionable insights, Certainty Software’s PPE Inspection Checklist is a practical resource for implementing OSHA’s requirements and fostering a culture of safety.
Download the PPE Assessment Checklist today to equip your team with the tools they need to protect every worker and stay ahead of compliance requirements.
You might also be interested in: