
Construction sites come with risks. As noted by Industrial Safety & Hygiene News, one in every 10 employees is injured annually on worksites, leading to a non-fatal injury rate 71 percent higher than in any other industry. Taking steps to prevent these injuries such as prioritizing proper Personal Protective Equipment offers multiple benefits for companies: Staff feels safer at work, overall downtime is reduced and businesses can save up to $32,000 per injury avoided.
And while there’s no one-size-fits-all safety plan for construction sites, there is a common starting point: Personal protective equipment (PPE). In this piece, we’ll break down the basics of PPE, what it does, why it matters for the construction industry, and how your business can boost PPE adoption to improve workplace safety.
What is Personal Protective Equipment (PPE)?
According to the Occupational Safety and Health Administration (OSHA), PPE is “equipment worn to minimize exposure to hazards that cause serious workplace injuries and illnesses.” Common examples of PPE include safety glasses and other eye protection, hard hats, steel-toed boots, hand protection, coveralls, respirators, and ear protection. Common workplace hazards include falling objects, forklift injuries, trip and fall hazards, and injuries from power tools.
Data proves that Personal Protective Equipment works: When OSHA mandated the use of hard hats on construction sites in the 1970s, there were 15,000 worker deaths on average each year. In 2016, this number fell to 5,200. And while there’s more work to be done — 5,200 isn’t zero, after all — the role of PPE in worker safety and workplace productivity is undeniable. PPE can also help reduce the risk of near misses. While these misses may not lead to injury, they do require reporting to ensure companies meet OSHA standards.
Considering the Role of Personal Protective Equipment in Construction
Proper use of PPE in construction comes with a two-fold impact. First is the decrease in on-site injuries, which both increases employees’ confidence in workplace environments and reduces total spending to address these injuries and remediate their root causes. Next, is increased productivity, since fewer injuries mean more staff at work and more projects completed on time.
Given the continually-changing nature of construction environments even over the course of a single project, effective PPE strategies can have a significant impact on both the well-being of workers and the ability of companies to meet evolving OSHA expectations.
Exploring the Role of PPE in Workplace Safety
PPE also plays a larger role in workplace safety, so long as organizations can ensure employee buy-in. This is often the biggest challenge with PPE programs; if staff aren’t on-board, even the best equipment won’t prevent injuries. In some cases, resistance comes due to changes in policy, such as the adoption of new PPE regulations that mandate additional personal protection to reduce overall injuries. In others, workers familiar with their job roles may underestimate the risk of a given situation and may choose not to wear mandated PPE unless management staff are present. In both scenarios, the result is increased risk.
One way to boost the adoption of PPE in the workplace is by implementing behavior-based safety (BBS) programs and safety training. These programs focus on creating a shared safety culture by addressing the biggest driver of workplace injuries: Employee behavior. By regularly engaging with employees and soliciting their feedback about both safe and unsafe behaviors in the workplace, companies can build hazard communication and safety programs that proactively address and correct common injuries.
Toolbox Talks and Their Impact on PPE Adoption
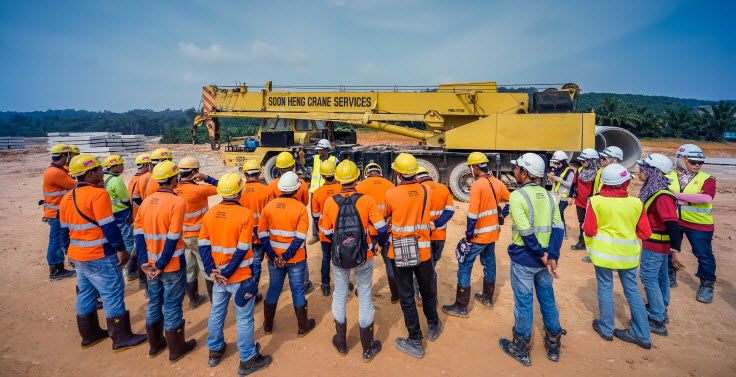
Also called safety meetings, toolbox talks take place before work starts for the day. They should be short (10-15 minutes), should be conducted on-site, and should focus on the potential health and safety risks of tasks in current work environments. These talks aren’t meant to conduct in-depth analysis but rather ensure that supervisors and staff are on the same page when it comes to safety. They should include worker participation — which could mean written job plans or verbal Q&A — and should specifically call out potential hazards and the role of PPE.
Purpose-driven toolbox and safety talks that are time-limited and target specific safety topics can both reinforce the need for PPE on job sites and help ensure companies meet construction safety compliance requirements in the event an injury does occur.
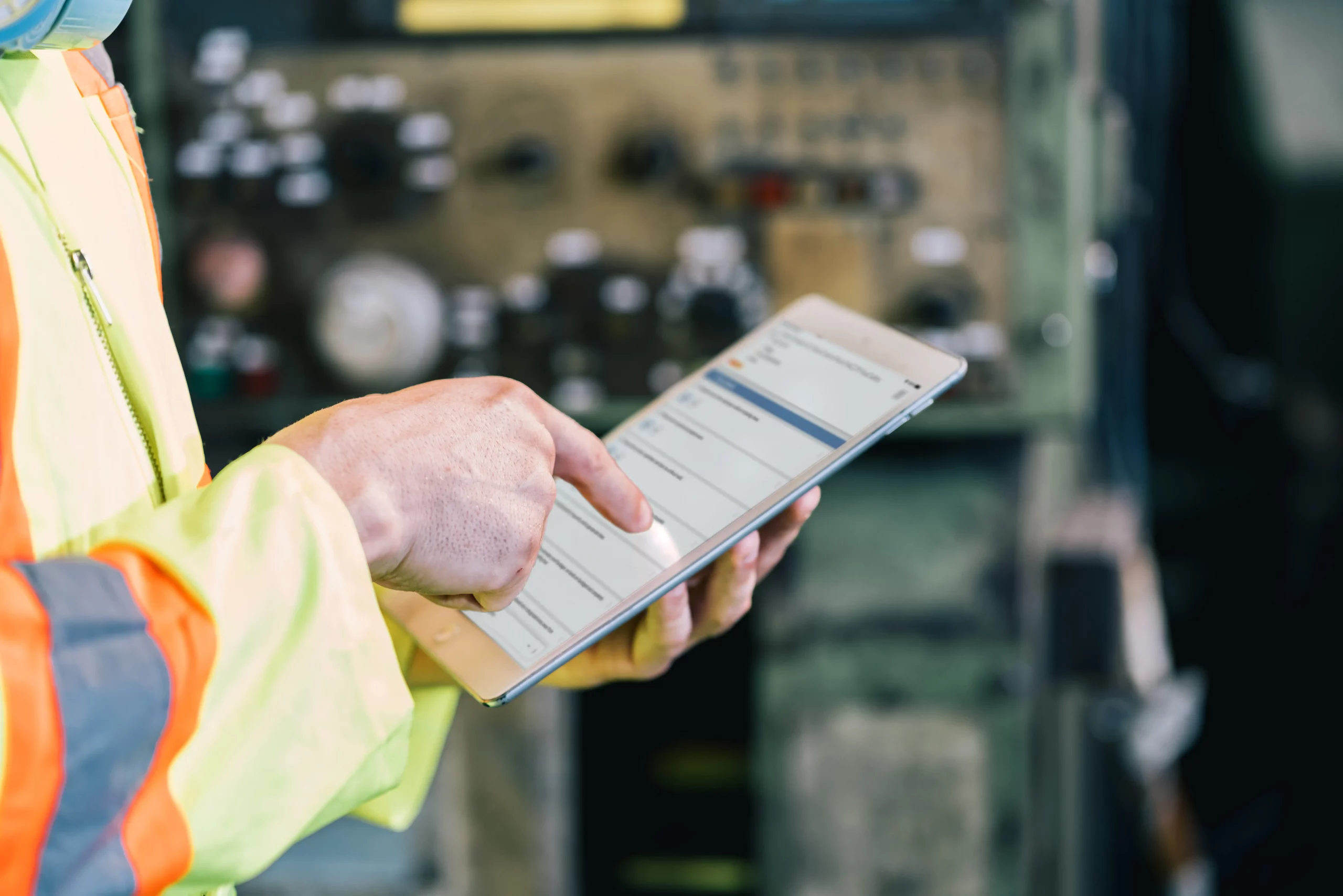
30+ Audit and inspection checklists free for download.
Safety First
Safer worksites are better for everyone. Fewer injuries mean reduced time lost, improved employee confidence, and increased production efficiency — and it all starts with PPE. By identifying key areas of PPE implementation, regularly inspecting equipment, and implementing both robust BBS and regular toolbox talks, a business can boost its bottom line and reduce total risk.
You may also be interested in:
Personal Protective Equipment (PPE) Assessment Checklist