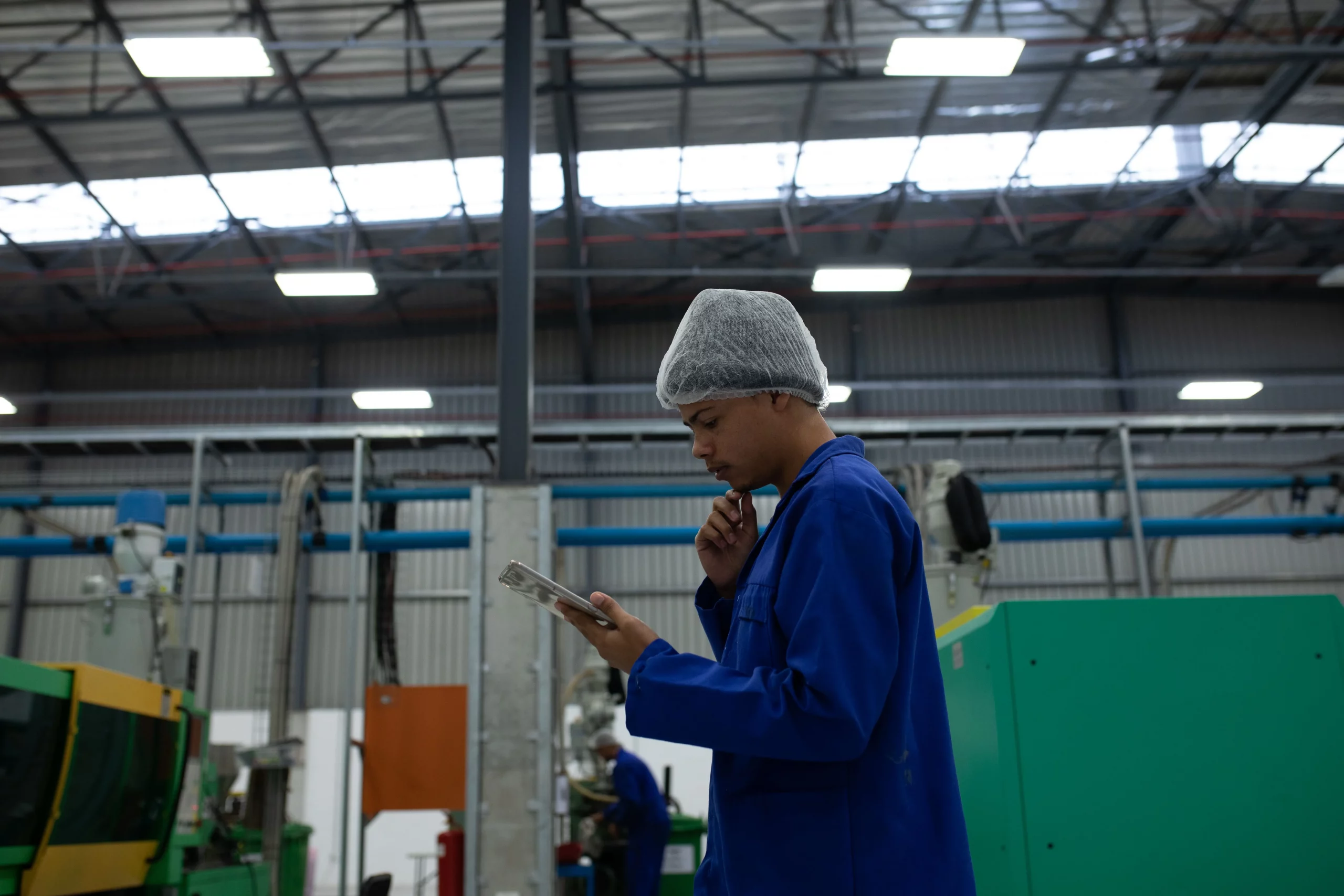
How do you know if your products are good enough for your customers? If you are a manufacturer, you probably have a set of quality standards and specifications that you follow to ensure that your products meet the expectations of your customers and the requirements of the market. But how do you verify that your products actually meet those standards and specifications? That’s where quality control inspection comes in.
Quality control is essential to ensure that the products being produced align with specifications and meet basic standards of reliability and safety. As a result, businesses are best served by regularly carrying out a quality control inspection and quality assurance inspection across the production process to assess the current quality and address potential issues.
What is a Quality Control Inspection and Why is it Important?
Quality control inspection means checking that a product meets what you want and expect. It is the process of evaluating products against a set of established manufacturing process standards and product specifications. These standards may come from international sources such as the ISO or may be part of the requirements in specific countries, states, or even municipalities. Quality control inspection teams are responsible for evaluating both incoming and outgoing products, identifying any defects, and reporting their findings to management and C-suite executives. If defects are significant enough, companies may need to temporarily pause production while processes are adjusted and tests are conducted. While this comes with a loss of productivity, it’s better than the alternative: Product failures leading to injury or death that necessitate immediate action.
By regularly assessing quality at multiple points along the production chain, companies can identify potential pain points that could be contributing to product issues, and take actions to rectify these issues before they result in product recalls.
Five Common Types of Quality Control Inspections
When it comes to quality control inspections, you’ve got a choice. Your teams can assess products at any point in their lifecycle where you believe there might be an issue. For example, if you’ve just purchased a new production line device and want to make sure it’s working as intended, you might assign a quality inspection team to conduct a quality control assessment and ensure the device is working as intended. Or, if you’ve just switched suppliers you may want an inspection of their first few shipments to confirm that the quality is both as expected and consistent across batches.
Although every company is different, there are five common types of quality control inspections often used to evaluate operations.
- Supplier inspections: Evaluate the raw materials or products sent along your supply chain.
- First article inspections: Assess the first mass production run of manufactured products.
- Inter-production inspections: Collect real-time data and ensure quality consistency during the production run.
- Pre-shipment inspections: Use a random sample method to check product quality before shipping.
- Container loading inspections: Ensure proper packing and loading of finished products.
Let’s take a closer look at each type of inspection and how they can help you improve your product quality and customer satisfaction.
Supplier Inspections
Supplier inspections are also called pre-production inspections. Here, teams evaluate the raw materials or products sent along your supply chain. Do they match provided specifications? Are they as durable/flexible/functional as claimed? Are they consistent across batches? Supplier inspections help ensure that your production processes aren’t hampered by low-quality materials and provide you with an inspection report you can take to suppliers for corrective action.
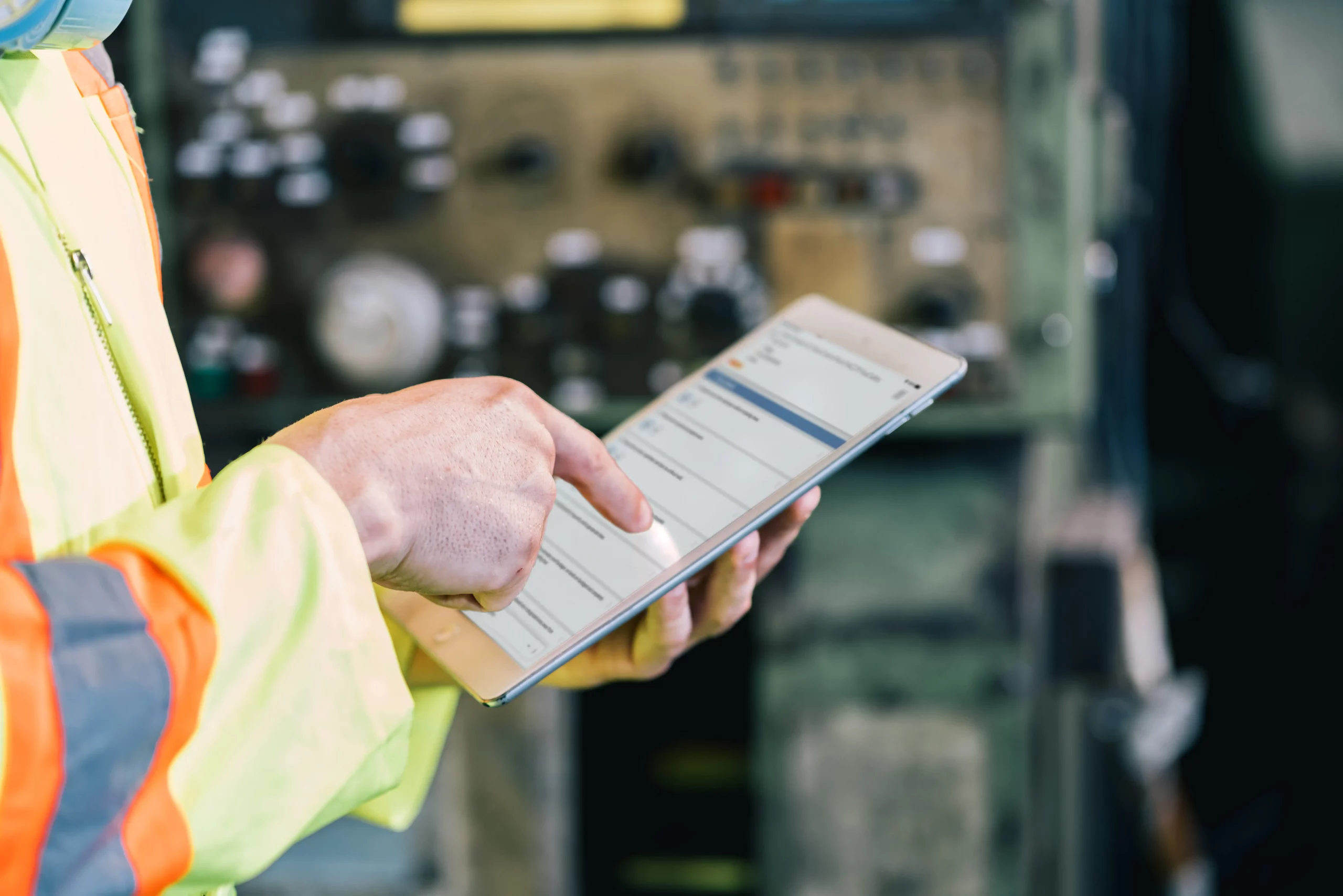
30+ Audit and inspection checklists free for download.
First Article Inspections
First article inspections happen after the first products are produced by your production line. By assessing the first mass production run of manufactured products, teams can compare output to stated product quality specifications and make recommendations for any necessary corrective action.
Inter-production Inspections
Inter-production inspections typically happen when between 30% and 50% of a mass production run has been completed. This allows teams to collect real-time data and ensure that quality hasn’t decreased throughout the production run.
Pre-shipment Inspections
The pre-shipment inspection often occurs when at least 80% of the run is finished and goods are being packed for shipment. Using a random sample method, quality control inspectors can get a general sense of product consistency and remove any faulty products.
Container Loading Inspections
Finally, container loading inspection processes happen after all other quality control inspections have been completed, and focus on ensuring that finished products are packed correctly. It also offers one last chance before shipping to discover any damages or defects in the final products.
The Importance of Quality Assurance and Software Solutions for Product Quality
It is important to note that quality control inspections are not a guarantee of flawless products. Even the most rigorous and comprehensive inspections can miss some defects or errors that may affect the performance or safety of the products. This is why quality control inspections should be complemented by quality assurance processes that monitor and improve the overall production system.
A lack of quality assurance can lead to serious consequences for manufacturers, such as product recalls, customer complaints, legal actions, or reputational damage. A prominent example of this is Tesla, a company that faced quality issues and recalls due to production ramp-up and lack of quality control. According to Reuters, in 2021 Tesla recalled “more than 475,000 of its Model 3 and Model S electric cars to address rearview camera and trunk issues that increase the risk of crashing”.
To avoid such problems and ensure consistent product quality, manufacturers need to use quality control inspection software and quality management software that can help them track, measure, and improve their production processes. Quality control inspection software can help manufacturers automate and streamline their inspection workflows, collect and analyze data, generate reports, and identify areas for improvement. Quality management software can help manufacturers manage their quality standards, policies, procedures, audits, corrective actions, and continuous improvement initiatives. Together, these software solutions can help manufacturers achieve higher levels of quality performance and customer satisfaction.
How to Use Quality Control Inspection Checklists to Improve Your Product Quality
The benefits of an effective quality control inspection include greater confidence that products entering or leaving your facility meet all applicable quality standards, along with the ability to document these findings of reporting and auditing, in turn ensuring that your quality management system is up to date.
But how do you leverage these benefits in practice? It starts by identifying areas of potential concern using inspection checklists. Here, options such as a Gemba Walk Checklist can help pinpoint product processes that are worth a closer look. Then, you can determine where in the product lifecycle these concerns fall: Are they supplier issues? Inter-production problems? Pre-shipment concerns? Once you know what you’re looking for and where it’s happening in your production framework, you can assign a quality control inspection team to carry about the applicable inspection type and report the results.
In this blog post, we learned that:
- Quality control inspection is a process of checking that a product meets the quality standards and customer expectations.
- There are five common types of quality control inspections: supplier, first article, inter-production, pre-shipment, and container loading.
- Quality assurance and software solutions are essential for improving product quality and avoiding problems such as recalls, complaints, or lawsuits.
You may also be interested in:
What are first, second, and third-party audits?
The Four Phases of Continuous Improvement Assessment — and What They Mean for Your Business