Unsafe processes and workspace pose a serious risk for workers and can lead to significant impacts on overall production performance. Consider recent safety data from the National Safety Council, which found that in 2020, more than 1.2 million workers suffered workplace injuries or illnesses related to their job that required time off from work. The message is clear: If companies can eliminate likely areas of injury, they can improve operations and minimize loss. Implementing the Safety Observation system can help streamline this process if they’re effectively designed, implemented, and reviewed.
Not sure where to get started? Follow these five steps to help get your safety management and observation program off the ground.
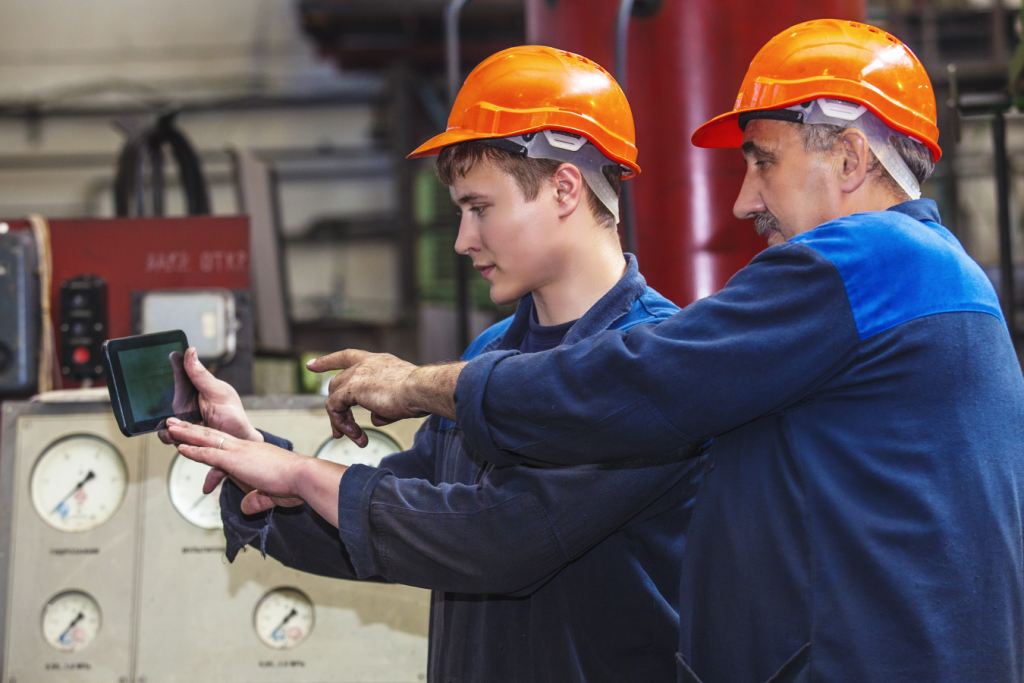
What is a Safety Observation?
Before digging into the 5-step safety process, it’s worth understanding the basics:
A health and safety observation is designed to pinpoint both safe and unsafe actions in workplaces. This helps to provide an overview of what’s working in your current process, what isn’t, and what needs to change.
In practice, safety observation involves designated team members watching employees in action as they perform both day-to-day and mission-critical tasks. Ultimately, they are looking to see where workers are performing tasks correctly, where they may be cutting corners, and where processes themselves may improve.
As an example of a safety observation, consider a staff member using a forklift to reach a pallet on a high shelf. Safety observers are looking to see if proper processes are followed. For instance, is the forklift given a walkaround to identify hazards before use? Is the operator wearing the correct safety gear in case something goes wrong? Are they using the vehicle in a safe manner with consideration for those around them?
Observations for safety also look for elements of the process that create unsafe conditions regardless of the operator’s action. For example, a heavy pallet has an increased risk that the forklift tipping or the pallet itself falling.
Step 1: Understand the Role of Safety Observation
Before creating a safety observation framework and reporting system, it’s important to understand the role of observation across your organization. Effectively implemented, it can help achieve three key goals:
- Reduced risk exposure
By identifying areas of concern across workplace operations, companies can reduce their risk exposure. In turn, reducing the number of potential hazards that exist. Rather than relying on workplace walkthroughs to pinpoint potential problems, safety observations regulate this process to provide consistent risk feedback and ensure companies are aligned with both internal guidelines and external safety expectations, such as those from OSHA.
- Increased process visibility
Safety observations also increase total process visibility by providing insight into each aspect of key operations on the job site. By watching staff as they work — how they interact with devices, machinery, and other employees — companies gain a better sense of what’s happening, when, and why.
- Improved safety awareness
Finally, observations in safety paired with regular training and review can help improve safety awareness among staff. In turn, this reduces total risk and increases the likelihood that employees will report safety concerns.
Step 2: Identify the Scope of Safety Observation
To ensure safety observations deliver on their potential, it’s critical to identify the scope of the process across four areas:
- Who
Stakeholders involved in the safety observation process include safety officers, management, and front-line workers. For this process to be effective, it must be a collaborative effort: If staff feel they’re being singled out or aren’t trusted to complete their work effectively, observations won’t deliver ideal results.
- What
Data gathered in safety observations includes information about how processes are completed, how often unsafe behaviors or unsafe acts occur, the nature of these actions, and the likelihood that they could lead to machinery damage, a near miss, or staff injury.
- Where
Safety observations must take place in the work area itself. While written reports and even video records are useful, effective observation requires direct interaction with the workplace environment.
- How
Along with observing operation data and comparing it to current procedures, observers are best served by speaking with staff to determine if issues related to workplace stress, communication, or trust are negatively impacting safety procedures.
Step 3: Create a Reliable Observation Framework
With goals in mind and the scope defined, the next step is creating a reliable observation framework. While there’s no one-size-fits-all approach to collecting and using safety observation data, common characteristics include a focus on detailed documentation that pinpoints both safe processes and unsafe actions and helps companies prioritize their response.
One option here is to build observation forms and frameworks from scratch, but this process can be complex and time-consuming. For many companies, the simpler path to safety success starts with safety observation checklists and safe behavior templates that provide a jumping-off point for more specific safety design. It’s also worth considering the use of safety observation tools and management software that help streamline safety data collection, centralize key information and make it easy to pinpoint trouble spots in your operations.
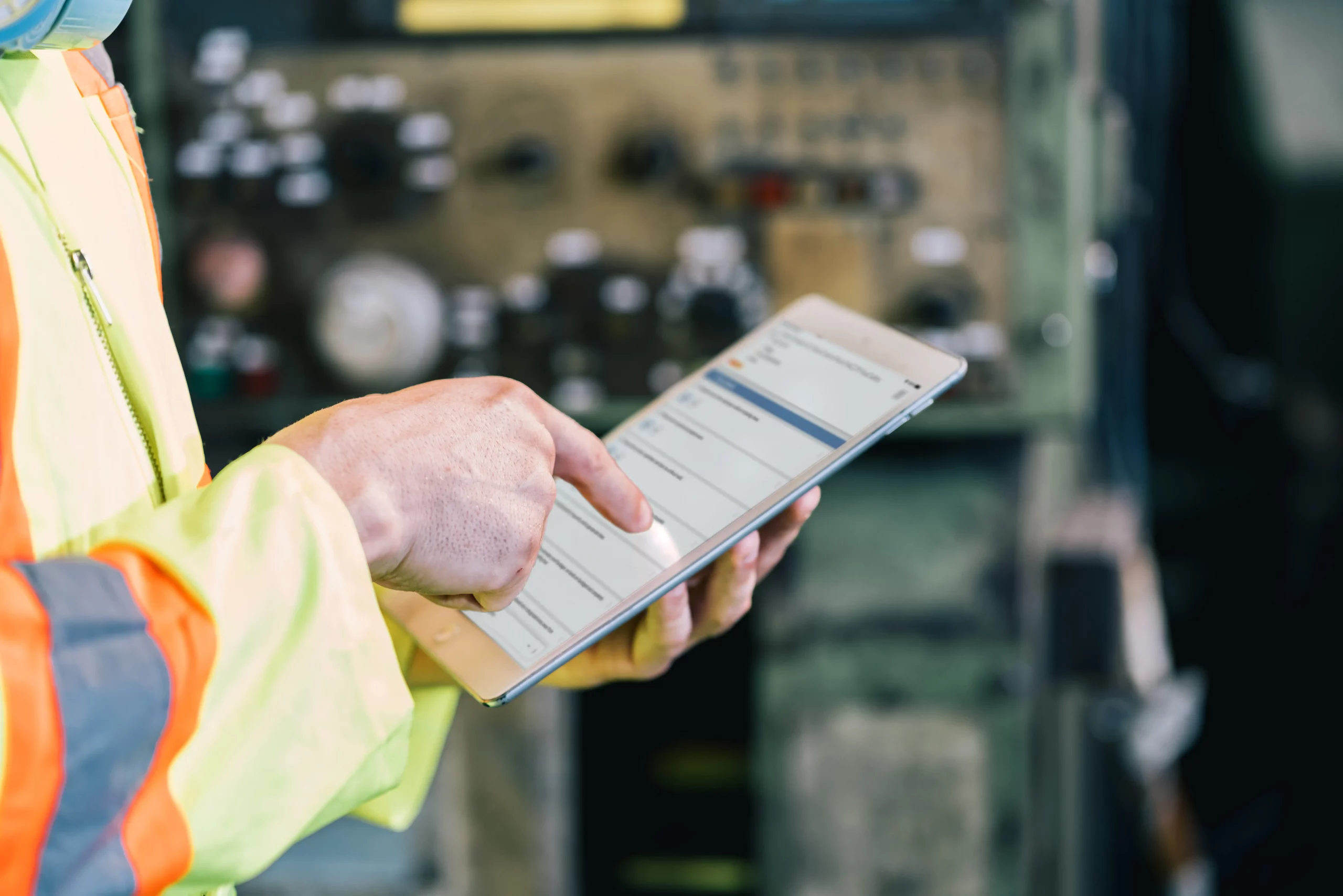
30+ Audit and inspection checklists free for download.
Ultimately, the goal here is reliability: By creating frameworks that target common processes and collected key data in real-time, businesses are better equipped to pinpoint safety issues.
Step 4: Pinpoint Key Areas for Improvement
These issues are the focus of step four. As safety auditors observe team members at work, they need to both pinpoint and prioritize issues they encounter, then review this safety data to determine appropriate corrective actions. Consider the observation of several employees not wearing their high-visibility vests as required on the worksite. While risks of workplace injuries and illness exist here if they can’t be easily seen by other staff operating machinery, the concern can likely be addressed with a reminder at the moment followed up by a quick staff meeting.
Now consider a staff member operating heavy machinery without any of the proper personal protective equipment (PPE). Not only are they putting themselves at risk but could also derail production lines for days or weeks if a serious injury occurs. In this case, addressing the issue is a top priority. Along with taking the specific staff member off the production line for safety training, companies are best served by reinforcing expectations around PPE with policy updates that lay out clear-cut consequences if rules are not followed.
Step 5: Setup a Repeatable Safety Process
In addition to the four processes listed above “when” also forms a part of the safety audit and observation process. Ideally, internal observations should be carried out once per quarter, and it may be worth bringing in an experienced third-party provider to conduct more in-depth annual evaluations and help identify processes that require a complete overhaul.
Ideally, it’s worth creating a repeatable safety process framework that you can modify as needed but retains the critical elements necessary to evaluate the safety of work environments, identify risks and pinpoint potential remediations. Worth noting? This is an ongoing process. While basic functions around observation and reporting will remain largely consistent, the specific processes you’re evaluating and the outcomes you’re looking for will change based on several factors including current legislation, order volumes, and technologies available to help mitigate risk.
Safety First
The safer your workplace, the better — both for staff and for your bottom line. Employees that feel safe at work and feel that their feedback is valued are more likely to keep working with your organization while reducing the risk of hazards means both lower time off volumes and increased productivity since you’ll spend less time managing staff shortages and more time focused on boosting overall output.
You may also be interested in:
The Safety Observation Report: 5 Tips to Help Safety Managers