Workplace safety is critical to ensure both employee protection and productivity — staff missing work because they’ve suffered injuries on the job can negatively impact both staff morale and overall output. As noted by the U.S. Bureau of Labor Statistics, however, workplace safety remains a challenge: In 2019 alone, more than 880,000 workers suffered nonfatal injuries or illnesses that caused them to miss work. Even more worrisome? If these injuries occurred due to non-compliance with OSHA or other standards, companies could face substantial penalties; first violations under OSHA cost more than $13,000 and repeated issues are ten times that amount. The Safety observation Report forms the first line of defense against both worker injury and non-compliance investigations, but many businesses struggle to draft, deploy and deliver on the promise of these reports at scale.
In this piece, we’re tackling the top five challenges of safety reports — and offering actionable insights to help your company solve for safety.
What is a Safety Observation Report?
A safety observation report is a physical or digital document used by safety officers to help identify potential risks and implement corrective action before staff is injured. These reports often take the form of checklists for initial observations followed by more in-depth questions to help safety teams describe specific concerns.
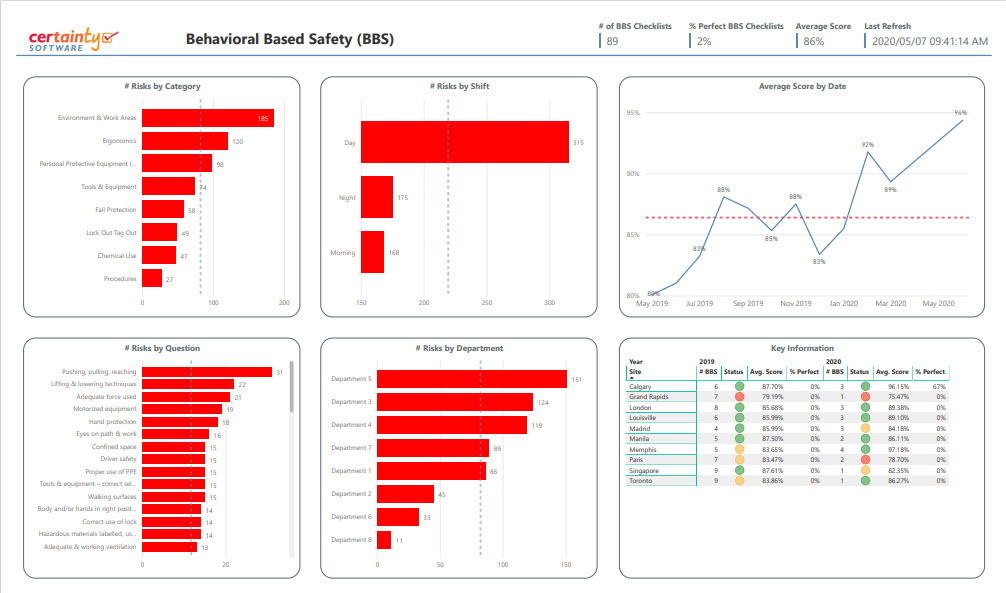
No matter what form your report takes, however, consistency is key: Teams must have access to the most recent version of the report and a shared understanding of what needs to be documented and what action must be taken.
Why Use a Safety Observation Report?
Using a safety observation report offers multiple benefits, such as:
Enhanced compliance
Complete and accurate documentation helps ensure compliance with workplace safety regulations. While OSHA remains the most common legislative obligation, companies may also be responsible for ensuring worker safety under standards issued by other government agencies such as the Federal Aviation Administration, the Department of Energy, or the General Services Administration.
Improved staff morale
According to the CDC, workplace health and safety (EHS) programs that address the “needs, risks and interests of employees can improve the retention of current workers and create long-term employee loyalty to the organization.” It makes sense: If staff feel safe at work, they’re less likely to look for employment elsewhere, especially when safety is part of a larger focus on employee wellness.
Reduced operational risk
Safer worksites mean reduced risk. Comprehensive safety observation reports help identify key concerns in the work environment and address them before they cause harm. For example, if safety procedures aren’t being followed or staff observes and documents a hazard with a specific machine on production lines, team leaders can determine why safety procedures aren’t being followed or target the hazardous machine for proactive repair or replacement — before someone gets hurt.
Increased performance
Proactively documenting and targeting risky behaviors or reduced machine output can help boost overall performance. While companies will lose some production time in addressing and correcting these issues, since staff may need to be retrained and machines may need to be replaced, the long-term benefits substantively outweigh any short-term delays.
Solving the Top Five Safety Observation Report Challenges
Safety observation reports are necessary to ensure compliance, increase staff morale and improve operations over time. But challenges remain, including:
1) Targeting Key Hazards
Different hazards carry different risks. In theory, anything is potentially dangerous — staff could trip and fall anywhere in your facility, making your entire production floor a possible compliance challenge. As a result, many firms feel overwhelmed when it comes to creating safety reports: Where do they start? What do they prioritize?
To solve this challenge, start with a focus on primary operations. Identify areas where workers spend most of their time, what tasks they’re performing in these areas and what protective procedures and equipment are required. The use of mobile app technology for completing observation forms, identifying issues (including photos, documents, etc.), and creating and delegating corrective action in real-time, can significantly reduce this challenge and provides a solid starting point for any safety process.
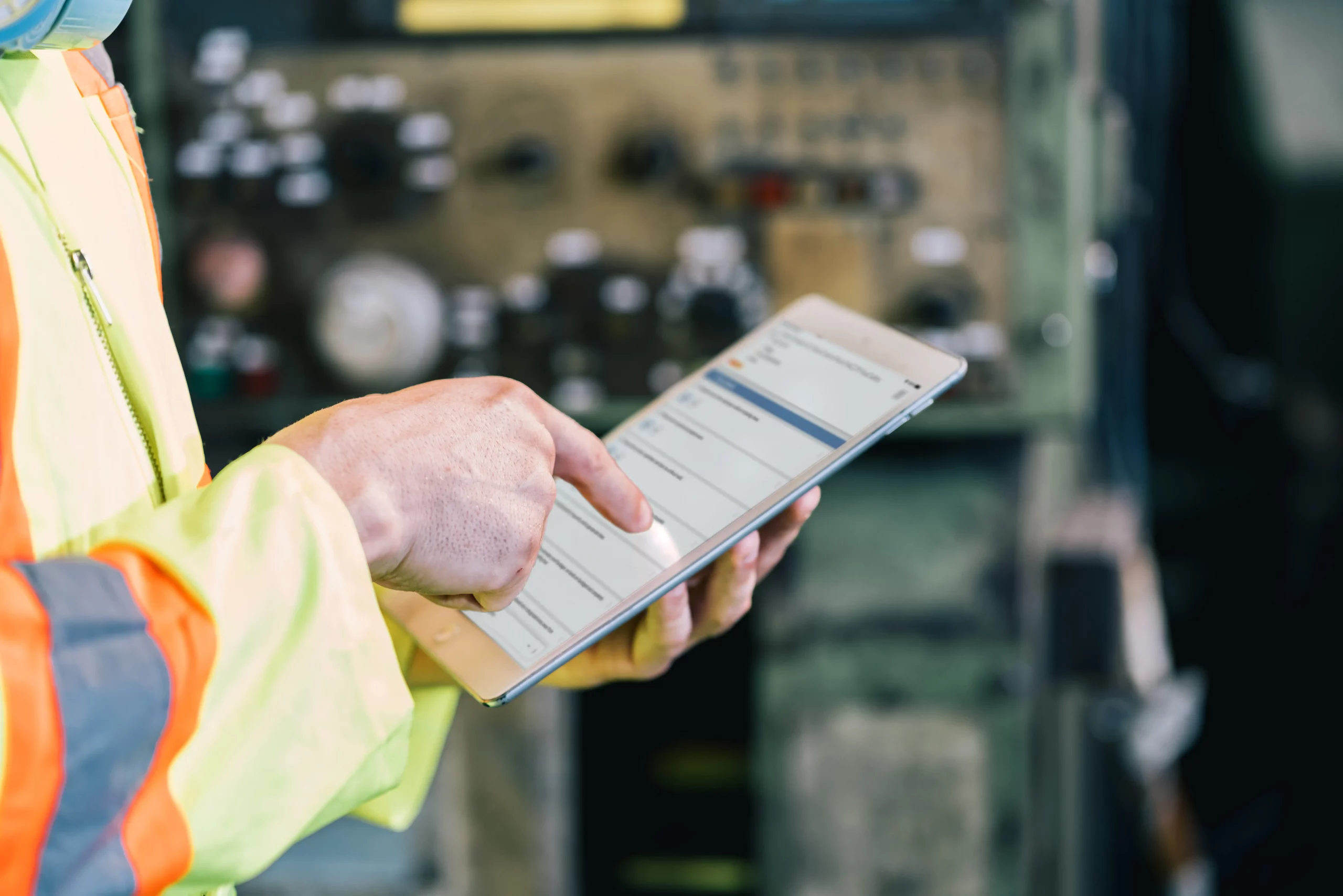
30+ Audit and inspection checklists free for download.
2) Taking Immediate Action
Once you’ve identified unsafe behaviors, working conditions or potential hazards such as the absence of or improper use of personal protective equipment (PPE), the next step is taking action. The challenge? Ensuring this action is timely and appropriate. In this case, it’s critical to define the timeframe of observations — are they current? Historic? Are the same issues recurring? Next, companies need a way to prioritize responses. Here, robust software tools can help close the gap between reporting and response by making data available immediately for review.
3) Integrating Human Behavior
No matter how safe your workplace is, there is one factor you can never fully control: Human behavior. As a result, it’s critical to build a people-based safety program that helps staff understand the impact of their actions on both their own safety and those around them. Not sure how to get your behavioral safety program off the ground? Prioritize positive reinforcement of safe action to help get 100 percent buy-in from staff. Recognize, congratulate (and possibly even reward) safe acts, safe behavior, and safety culture in the workplace!
4) Tracking Critical Concerns
Tracking concerns remain a key challenge for safety reports. As companies expand and staff volumes grow, it’s easy for critical observations to get lost in the weeds. Here, businesses are often best served by software solutions capable of automatically collecting, integrating, and analyzing safety observations, near-miss information, corrective actions, etc. to identify safety priorities.
5) Conducting Regular Assessments
One-off safety inspections may catch critical issues before they occur, but long-term safety requires regular assessment to ensure processes and policies remain in place. To solve this issue, scheduling is key: Regular and repeatable assessments help create a safety-first culture committed to spotting and resolving incidents before they happen — rather than responding after the fact.
Safety observation reports aren’t just about compliance — they are a key resource to help continually improve a safety management program. They boost employee satisfaction and offer a path to improved safety workflows and operations. Not sure where to start? Gain compliance confidence with Certainty Software. Let’s talk.
Readers may also be interested in:
Behavior-Based Safety Observations
Where Do BBS Programs Typically Fail?
What Impact Will Technology Have on Your Behavior Based Safety Program?