Table of contents
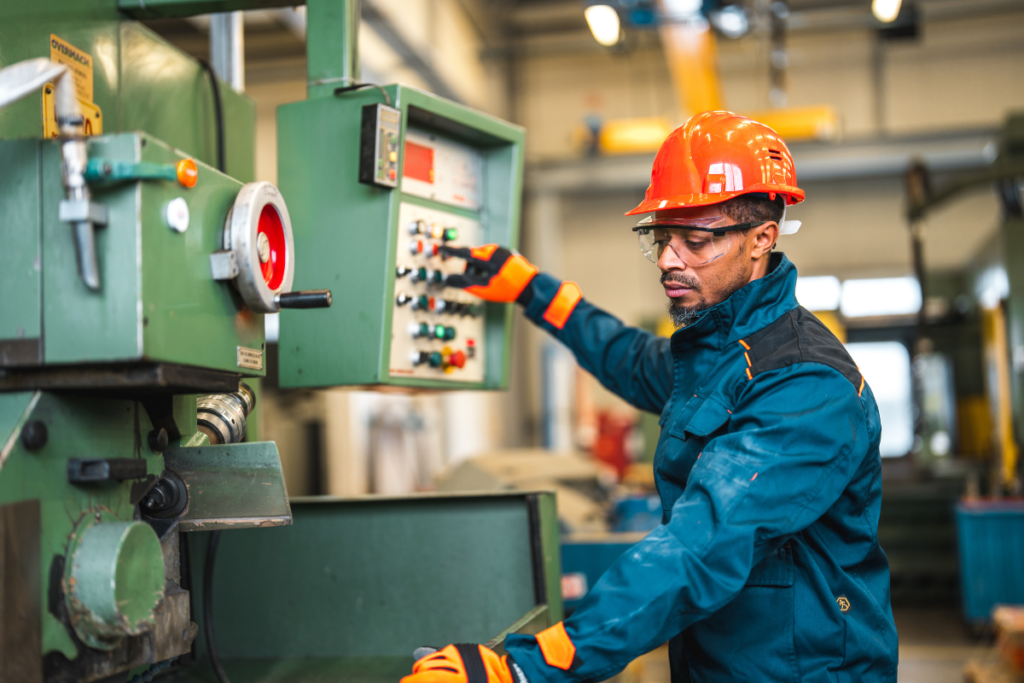
Manufacturing is a dynamic, competitive industry that relies on innovation and continuous development to stay ahead of the competition. How to streamline production procedures and cut waste, particularly when switching out equipment, is one of the major problems that manufacturers must deal with.
The switching of equipment from processing one product to processing another is referred to as equipment changeover. They are required to adapt production schedules and customer demands, but they can also result in significant downtime, inefficiency, and expense.
SMED (Single-Minute Exchange of Dies) is used in situations like these. A lean tool called SMED seeks to cut down equipment changeover time to under 10 minutes (or single-digit minutes). Manufacturers can reduce operational costs, improve productivity, and increase flexibility by applying SMED principles and techniques to their manufacturing processes.
What is SMED?
Single-Minute Exchange of Dies is referred to as SMED. Shigeo Shingo, a Japanese industrial engineer who worked with Toyota in the 1950s and 1960s, created it as a lean manufacturing tool. Shingo noted that the typical setup durations for the equipment changeover procedure were excessively long and had negative effects on output quality, irregular flow, and huge lot sizes.
Shingo suggested a methodical strategy for lowering setup times by getting rid of unnecessary stages, streamlining labor, standardizing processes, and parallelizing jobs. The idea of internal and exterior setup, which we will discuss later, was also introduced by him.
SMED aims to finish as many processes as possible while the machinery is operating (or processing) in order to save time and switch over rapidly to processing the next product. The phrase “single-minute” refers to changeovers that take less than 10 minutes (or one-digit minutes), not that they must all happen in a single minute.
SMED isn’t just for manufacturing processes using dies, which are specialized instruments used to specify a product’s size and shape. It can be used for any kind of process or equipment transition.
Why is SMED Important for Quick Changeover?
SMED is crucial since it aids businesses in enhancing their productivity and competitiveness in the following ways:
- Reduced Downtime: SMED decreases production stoppages and increases equipment utilization by cutting down on the time required for equipment changeovers. The average setup time reduction by using SMED methodologies, according to Shingo, the creator of SMED, is 94% (from 90 minutes to less than 5 minutes) across a variety of enterprises. This frees up more time for creating high-value goods and services for clients.
- Increased Productivity: Manufacturers can produce more items in less time and boost their overall output with reduced setup times. Additionally, it allows them to fulfill consumer requests more quickly and enhance delivery efficiency. Additionally, since smaller lots can be produced more frequently, the quicker setup time might result in lower inventory levels and storage expenses.
- Improved Flexibility: Manufacturers can react swiftly to shifting consumer needs and production schedules thanks to SMED. They can swap from one product to another with little delay or waste by cutting down on setup periods. Additionally, they are able to provide their clients with additional alternatives for customization and variety, which improves their satisfaction and loyalty.
- Cost Savings: In many areas of manufacturing operations, SMED can result in significant cost savings. For instance, quicker setup periods can lower labor costs since changeovers take less time and need fewer resources. They can also lower energy expenses because less electricity is used while people are idle. Additionally, as fewer adjustments and corrections are required during changeovers, reduced setup times can increase quality and decrease faults.
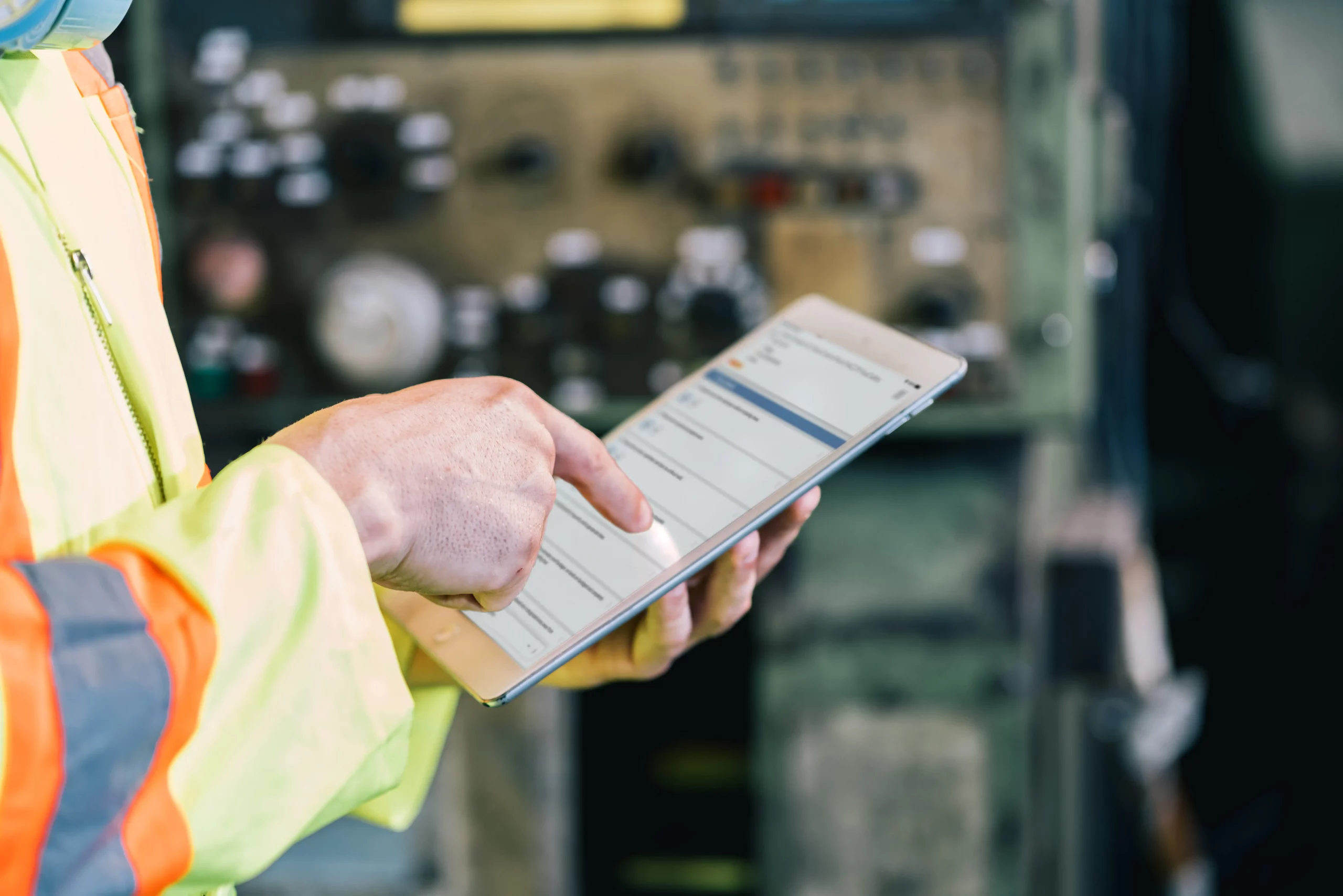
30+ Audit and inspection checklists free for download.
How Does SMED Work?
Applying a set of guidelines and methods with the goal of streamlining setup procedures and getting rid of waste is how SMED operates. SMED’s guiding concepts are:
Internal and External Elements
The actions that can only be completed when the equipment is halted (or not processed) are referred to as internal setup. When we talk about external activities or aspects, we’re talking about the jobs that can be done while the machinery is operating (or processing). The basic goal of SMED is to reduce the amount of time required to stop and start the equipment by converting as many internal setup processes into external setup duties as possible.
Identifying Waste
Any procedure or action that does not enhance the value of the good or service is referred to as waste. In SMED, waste can be found by reviewing the present setup process and looking for phases that can be combined, omitted, moved, or otherwise simplified. Wasteful activities include moving materials, testing things, changing settings, and looking for tools.
Standardization
Creating standardized processes and methodologies for setup chores is referred to as standardization. Standardization helps to assure uniformity and quality while lowering variability and errors. Utilizing uniform tools and equipment, producing standardized work instructions and checklists, and allocating standardized roles and responsibilities are some examples of standardization.
Parallelization
To decrease downtime, parallelization refers to using parallel work. Instead of sequentially or one after the other, parallel labor entails carrying out several tasks simultaneously or concurrently. Cross-functional teams, a large workforce, a large number of people or robots, and task synchronization can all be used to accomplish parallel work.
How to Implement SMED in Your Manufacturing Facility?
The following actions should be taken in a methodical and organized manner in order to adopt SMED in your manufacturing facility:
Conducting a Setup Analysis
The evaluation of the current setup procedure and the identification of potential improvement areas come first. The setup process can be observed and recorded, the setup time and its components measured, the setup tasks classified as internal and external, and the sources of waste and inefficiency found.
Brainstorming and Prioritizing
Involving cross-functional teams in the generation of concepts and options for cutting setup time is the next stage. To accomplish this, brainstorming tools like the 5 Whys, fishbone diagrams, or affinity diagrams can be used. The practicality, impact, cost, and risk of the suggestions and solutions should be considered as well as their order of importance.
Pilot Testing
The proposed enhancements are tested and improved in a controlled environment as the third phase. This can be accomplished by choosing a pilot location or piece of equipment, putting the changes into practice, monitoring the outcomes, gathering feedback, and making adjustments as necessary. Repeat the pilot testing until the desired setup time is attained.
Training and Continuous Improvement
The last step is to teach the staff about the new setup techniques and processes while promoting a culture of ongoing improvement. Clear work instructions and checklists can be provided to do this, along with regular audits and reviews, awarding best practices and accomplishments, and encouraging comments and suggestions
How Can Certainty Software Complement Your SMED Efforts?
A potent tool for managing industrial processes is certainty software. In the following ways, it can support your SMED efforts:
- Data Collection: You can use mobile devices or web browsers to gather audit and inspection data with Certainty Software. To record pertinent information, such as setup time, work classification, waste detection, improvement suggestions, etc., you can utilize editable templates or design your own forms.
- Data Analysis: You can use dashboards and reports provided by Certainty Software to analyze the data from your audit or inspection. To visualize your data and spot trends, patterns, gaps, and opportunities, use a variety of filters, charts, graphs, and tables. Your data can also be exported to Excel or PDF for more analysis.
- Data Sharing: Sharing audit and inspection data with your team and stakeholders is made easier with Certainty Software. To share your data and conclusions, you can use email notifications, alerts, comments, and attachments. Using Certainty Software, you can also delegate duties, keep track of actions, and assess progress.
- Data Security: By utilizing features for encryption, authentication, authorization, backup, and recovery, Certainty Software provides data security. You have control over who has access to and what uses are made of your data. Depending on your preferences, you can also store your data on-premises or in the cloud.
Conclusion
Equipment changeover time can be decreased to under 10 minutes (or single-digit minutes) with the use of SMED, a lean tool that can help you streamline your production processes. You may increase your efficiency, production, flexibility, and cost savings by using SMED ideas and methodologies.
SMED is neither a one-time endeavor nor a fast fix, though. It necessitates close attention to detail, thorough planning, ongoing development, and teamwork. You also need a strong tool, like Certainty Software, to assist you in gathering, analyzing, sharing, and safeguarding your data.
Please get in touch with us right away for a free demo or trial if you’re curious about how Certainty Software may help you enhance your manufacturing processes utilizing SMED or other lean solutions. You can also download some of our free checklists to start improving quality performance right away.
FAQ
Here are some frequently asked questions (FAQ) about SMED that you may find helpful:
What are the challenges or pitfalls of SMED?
- Resistance to change: Some workers could be hesitant or resistant to modify their current setup processes or methods, particularly if they have been using them for a long time or if they are not a part of the improvement process. To combat this, it’s critical to spread awareness of the advantages and objectives of SMED, include staff members in the ideation and testing processes, and offer sufficient training and support.
- Lack of information: Some manufacturers might lack precise or trustworthy information regarding their present setup times, tasks, and waste sources. Due to this, it may be challenging to evaluate and track the effectiveness and outcomes of SMED. Use a data collecting tool, such as Certainty Software, to assist you gather pertinent data, such as setup time, task classification, waste identification, improvement suggestions, etc., to overcome this.
- Lack of resources: Some manufacturers might not have the money, labor, equipment, or other resources to execute SMED successfully. The extent and impact of SMED enhancements may be constrained by this. To address this, it is crucial to set priorities, concentrate on the equipment or procedures that are most crucial or bottlenecked, employ cost-effective or free solutions whenever possible, and make use of cross-functional teams and concurrent work.
How do I measure and monitor my SMED performance?
There are numerous techniques to gauge and keep track of SMED performance, including:
- Setup time: Comparing the setup times before and after adding SMED enhancements is the most straightforward and direct way to gauge SMED performance. Internal setup time, external setup time, and other setup tasks or steps can all be subdivided within the setup time. The setup time should be lowered to around 10 minutes, ideally under one minute.
- OEE: OEE (Overall Equipment Effectiveness) is the gold standard in the industrial sector for gauging the effectiveness and productivity of machinery and production methods. OEE considers three variables: quality (the proportion of good output to total output), performance (the proportion of actual output to the maximum feasible output), and availability (the proportion of time the equipment is available to produce). By decreasing downtime, increasing productivity, and improving quality, the OEE score is to be raised.
- Inventory levels: Since they represent the lot sizes and manufacturing frequency, inventory levels are another technique to evaluate SMED success. Manufacturers can produce smaller lots more frequently by cutting setup times, which helps lower inventory levels and storage expenses. By just creating what is required when it is required, inventory levels are meant to be decreased.
How can I sustain my SMED process results?
In order to maintain SMED outcomes, it is crucial to
- Standardize: Use standardized tools and equipment, give standardized roles and duties, and create explicit work instructions and checklists for the new setup processes and methods.
- Audit: With the use of a data analysis tool like Certainty Software, which can assist you in visualizing your data and helping you uncover trends, patterns, gaps, and possibilities, audit the new setup procedures and methods on a regular basis by conducting inspections and reviews.
- Improve: By soliciting comments and suggestions from staff members and clients, using brainstorming techniques to produce fresh concepts and solutions, testing and fine-tuning improvement proposals in a controlled environment, etc., it is possible to continuously improve the new setup procedures and methods.