Table of contents
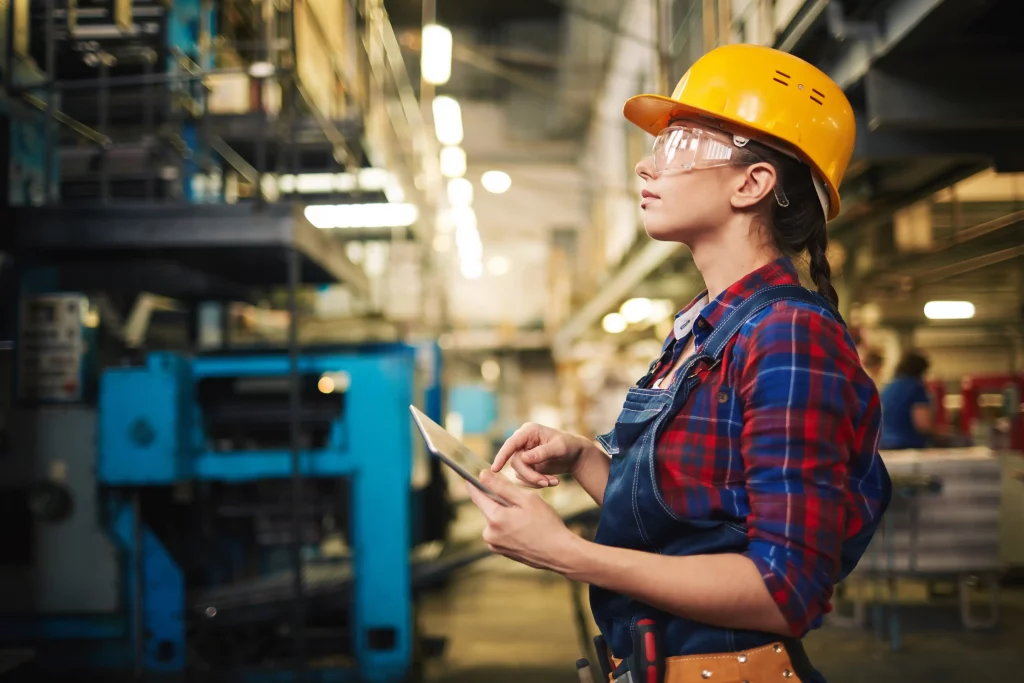
What is CAPA?
CAPA stands for Corrective and Preventative Action (CAPA) and is an assessment tool designed to help companies identify and remediate operational, environmental, as well as safety issues by taking corrective and preventive action.
According to the FDA, CAPA management processes have three key components:
- Corrections
Corrections are actions taken to eliminate a specific non-conformity, such as defects in a product when it comes off production lines.
- Corrective Actions
Corrective actions are taken to eliminate the cause of a problem or non-conformity and prevent a recurrence. These actions go a step further than corrections to provide longer-term solutions.
- Preventative Actions
Finally, preventative actions are taken to eliminate the cause of potential non-conformities identified during a CAPA audit. These actions allow companies to eliminate potential problems prior to their occurrence, in turn saving both time and money.
Why do CAPA Requirements Matter for Quality Management Systems?
Quality management systems (QMS) document all processes and policies required to achieve reliable quality levels in both staff operations and product outputs.
The CAPA system helps companies identify non-conformity issues that negatively impact quality, correct these issues through targeted action, and prevent these issues from recurring. As a result, the corrective action and preventive action model offered by CAPA is a critical component of QMS frameworks because it helps organizations go beyond documentation to take action that improves the overall quality and reduces the risk of non-conformance.
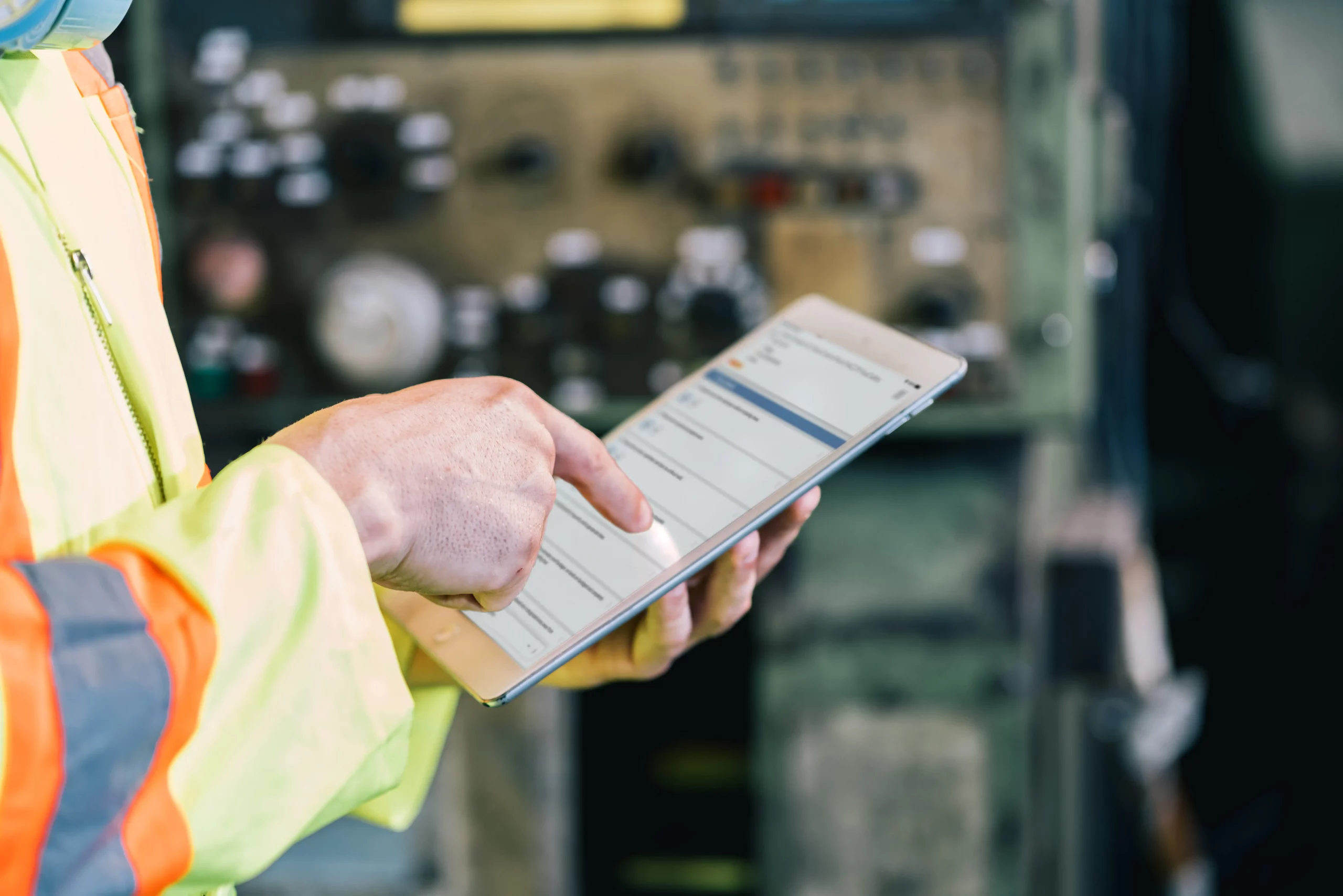
30+ Audit and inspection checklists free for download.
Six Steps for Effective CAPA Efforts
To make the most of this quality management framework, start with six fundamental CAPA process steps:
1) Pinpointing Key Problems
The first step in an effective CAPA assessment is pinpointing problems and describing them in detail. By documenting what’s happening, where, when, and why, companies lay the groundwork for targeted follow-up actions that address root causes rather than symptoms. Here, tools such as a Gemba Walk Checklist can help companies find the cause of the problem rather than simply identifying the symptoms.
2) Assessing Potential Risk
Next is risk assessment: If quality problems are occurring, what’s the risk to the business? Are these issues causing lost revenue? Customer complaints? Are companies at risk of failing to meet regulatory requirements? By considering both the initial and long-term impact of issues as they relate to quality, organizations can quantify the severity of the problem at hand and prioritize remediation efforts.
For example, if a CAPA real-time risk analysis reveals two quality issues that lead to occasional non-conformance, risk assessment can help determine the overall impact on the organization of each issue. This paves the way for prioritization and timelines for remediation that balance cost and conformity.
3) Determining Root Causes
Once a priority issue is identified, the first step is taking action to address the immediate concern. This is followed by root cause analysis to determine the underlying reason for a nonconforming product, in turn allowing companies to implement corrective actions that address specific workflows to prevent problems over the long term. By addressing the cause of nonconformities, businesses are better equipped to improve process outcomes.
4) Implementing Corrective or Preventive Actions
Implementation comes next. Depending on what CAPA audits revealed, this could take the form of a preventative action plan to reduce risk before issues occur, or effective corrective action to prevent problems from reoccurring. Complete documentation of actions taken is critical to ensure that companies know exactly what was done, when, and why.
5) Validating the Impact
Just because CAPA actions and process controls work on paper, this doesn’t guarantee they will have the same effect in practice. As a result, CAPA procedures include action validation after the fact to determine if the solution was effective. Here, metrics matter: If the goal is to reduce non-conformities and deviations from a specific process by a set amount, measurements must be taken before and after actions are taken.
6) Starting the Process Again
Last but not least? Starting over. Here’s why: Since there’s always room for improvement in any production environment, the need for CAPA investigation never really ends. By regularly conducting CAPA process assessments companies can steadily improve quality outputs and eliminate common sources of non-conformity.
Implemented effectively, the CAPA methodology can help your company improve product quality and reduce total risk.
You may also be interested in:
Quality Control Inspections: 5 Common Types to Boost your QMS
Quality Control Inspections: 5 Common Types to Boost your QMS