Table of contents
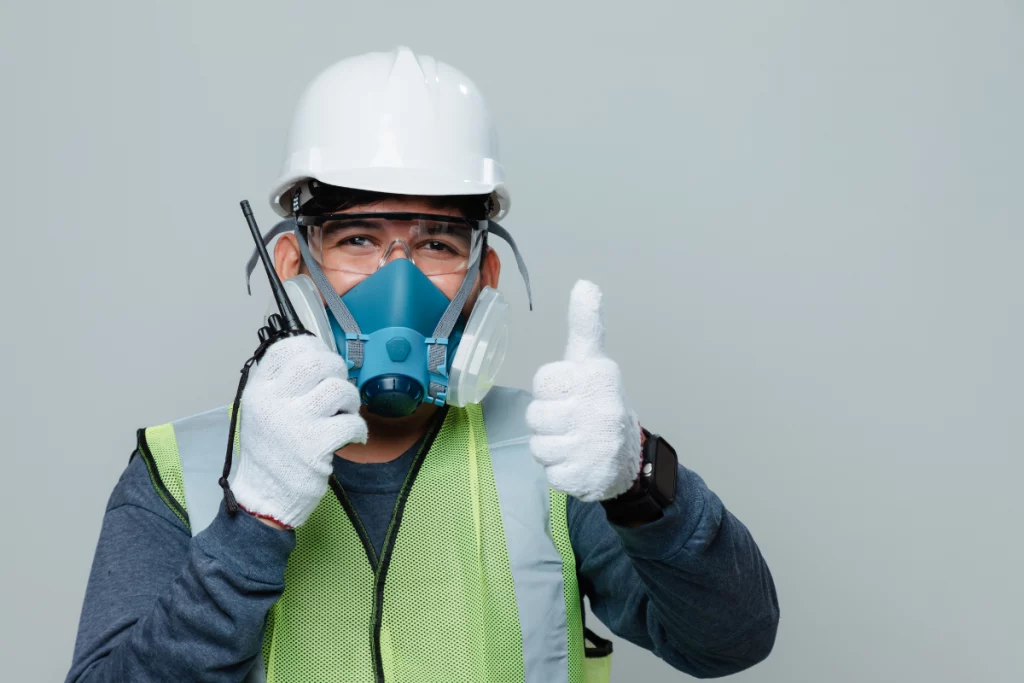
The Control of Substances Hazardous to Health regulations (COSHH) requires employers to monitor and manage the use of any substances that are potentially hazardous to health. According to the UK’s Health and Safety Executive (HSE), these substances may include (but are not limited to) chemicals and products containing hazardous chemicals and corrosive solvents, or biological agents, along with those that release vapors, wood dust, or gases.
To ensure workplace operations align with COSHH objectives, companies must regularly carry out COSHH risk assessments. In this piece, we’ll break down COSHH health risk assessment basics, the preparations needed before the assessment begins, and the steps companies can take to successfully carry out their COSHH assessment.
What is a COSHH Risk Assessment?
Under COSHH, any company that uses or comes in contact with substances that are potential health hazards must identify these substances and create a plan to mitigate their impact.
A COSHH risk assessment helps pinpoint these potential problems. By carrying out a thorough examination of current operations, companies can identify areas, products, processes, or specific situations that may carry a risk of harm. Equipped with this knowledge, organizations are better prepared to develop and implement measures that reduce the total risk of harm.
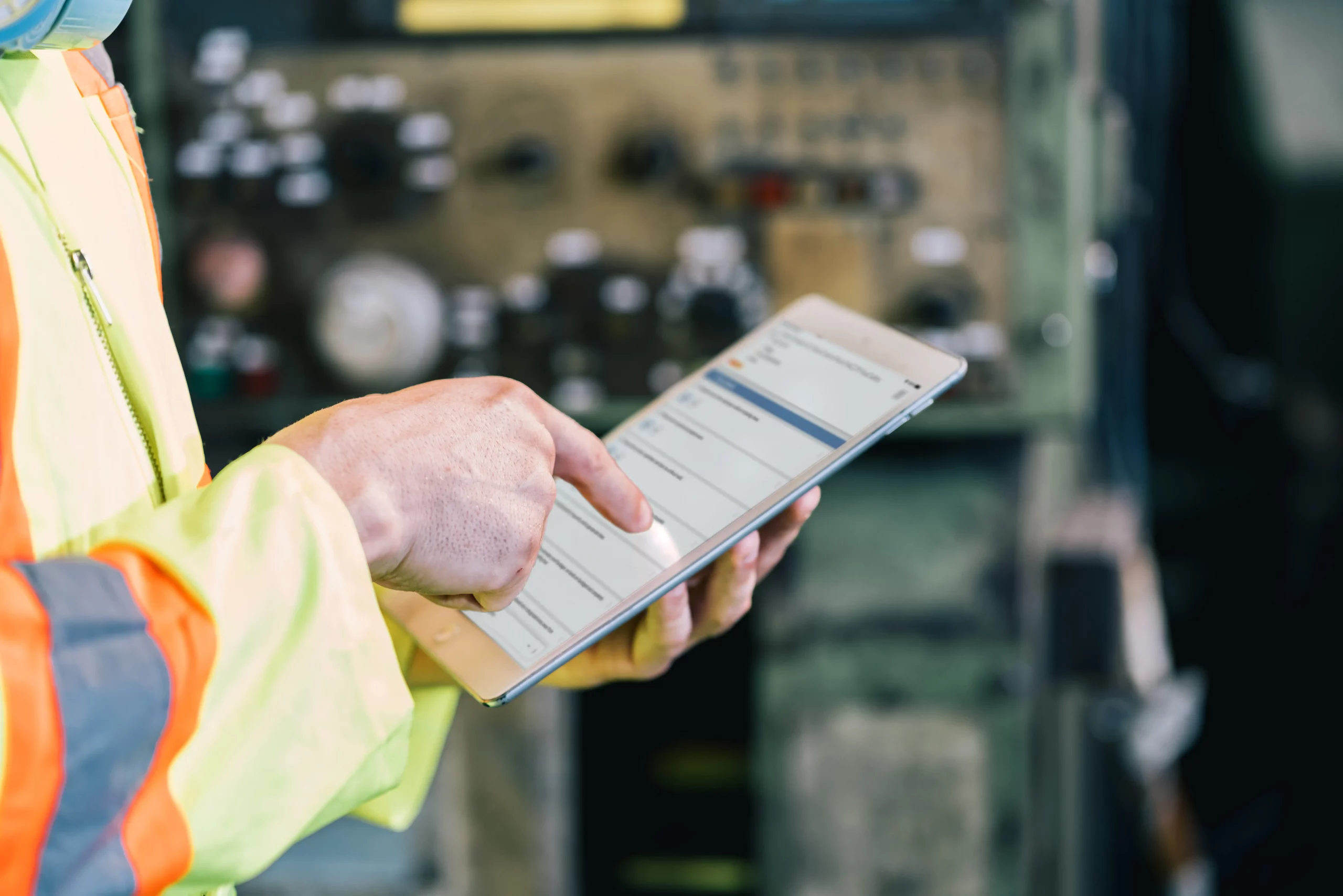
30+ Audit and inspection checklists free for download.
Preparing for a COSHH Risk Assessment
Before carrying out your COSHH risk assessment, it’s worth getting prepared. This starts with an understanding of what is (and isn’t) covered under COSHH.
For example, while harmful substances such as fumes, vapors, mist, dust, and chemical spillage are all covered under COSHH, there are exceptions for substances such as lead, asbestos, and radioactive products. In these three cases, separate legislation governs their use and so they fall outside the purview of COSHH compliance.
Once you know what you’re looking for, it’s worth carrying out a basic safety evaluation to find processes or procedures that may unintentionally pose COSHH risks and that could be addressed before a full assessment. For example, if you regularly use a forklift to move pallets around your warehouse, staff could be exposed to hazardous fumes when the vehicle is first started depending on where it’s parked in the facility. By changing its parking location, you can avoid a possible COSHH headache.
Not sure where to get started? Use our facility safety inspection checklist.
How to Perform a COSHH Risk Assessment
To perform a successful COSHH risk assessment, four steps are critical:
1) Identify risks and hazards
First, identify possible exposure points for employees. The goal here is to be as thorough as possible. The more issues found, the smaller the risks to staff, and the better your COSHH compliance. Sources of risk identification include simply walking around the workspace and observing current processes, examining work activity accident and near-miss records, reading product labels and material safety data sheets (MSDS), and — perhaps most importantly — asking employees.
2) Determine potential harm
Next, determine the potential harm caused if staff is exposed to hazardous materials. This includes the severity of the health effects — will a hazardous substance cause ill health such as headaches or vomiting? Injuries such as burns? Death?
Companies also need to consider who may be harmed. This not only includes employees working with or near hazardous substances but also other staff members such as after-hours cleaners or external maintenance teams. Finally, companies need to assess how long individuals may be exposed to a substance during their work process. This is especially critical since the impact of some chemicals or gases are cumulative over time.
3) Assess risk likelihood
Risks can be classified as low, medium, or high. For example, work practices that see a staff member wearing proper personal protective equipment (PPE) and interacting with a chemical necessary for production processes in a safe working environment could be considered low risk. Disposal of that same chemical, however, may be a higher risk if removal and handling processes aren’t well-defined. These risks must then be considered in light of HSE workplace exposure limits (WELs). The occupational exposure limits are intended to reduce the risk of excess inhalation or ingestion over the short term and ensure control of exposure over the long term.
4) Regularly update your assessment
Finally, it’s worth remembering that risk assessments are not set in stone. A low-risk process one month could become a medium or high-risk process the next depending on factors such as staffing changes, material suppliers, or required maintenance on processing machinery. As a result, risk assessments must be regularly updated to reflect current conditions.
Bottom line? Risk assessments are critical to ensure compliance with COSHH regulations and reduce potential harm.
You may also be interested in:
Considering COSHH — What’s Covered and Who’s Impacted
Incident vs Accident — Understanding the Differences for Improved Safety