Supply chain issues aren’t going anywhere. According to research firm McKinsey, 2022 comes with three key concerns: Labor shortages, equipment availability, and the “ripple effect” of continuing global bottlenecks. For organizations, this landscape creates a dual challenge.
Not only do they need to ensure the reliability and stability of supply chains but must also take steps to measure and evaluate compliance across these chains. And with supply chain security now the watchword to prevent sudden collapses — as seen at the beginning of the pandemic — the complexity of evaluation and compliance has increased significantly.
As a result, it’s now critical for companies to implement supplier compliance audit processes that both establish supply chain standards and effectively measure supplier performance against key metrics.
In this piece, we’ll explore the role of a supplier audit, the common types used, what measurements to include, and how you can prepare for an upcoming audit.
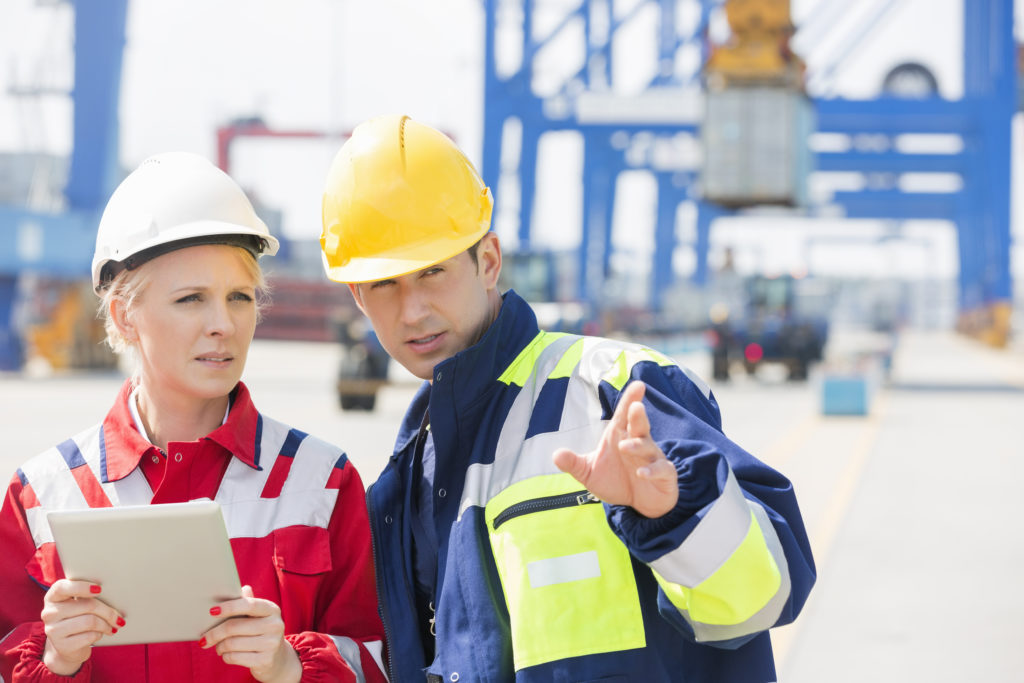
What is a Supplier Compliance Audit?
A supplier compliance audit is an evaluation of suppliers’ adherence to current industry standards. For example, food product suppliers might be evaluated on their ability to ensure that food item production meets federal health protocols. Such would include safe food handling, robust quality control, and specific processes designed to limit the risk of cross-contamination or the introduction of allergens.
Worth noting? There is no single framework for supply chain audit initiatives. Suppliers in different industries, from food processing to raw materials handling to electrical component assembly, each has their own set of industry compliance requirements along with any compliance expectations imposed by your business to ensure you can meet regulatory obligations.
Supply chain audits may be conducted by internal teams or may choose to employ a 3rd party for this purpose. The use of 3rd parties is more common since they may identify issues that internal teams overlook due to familiarity. In addition, the use of 3rd parties better prepares organizations for potential audits by federal, state, or industry regulatory bodies.
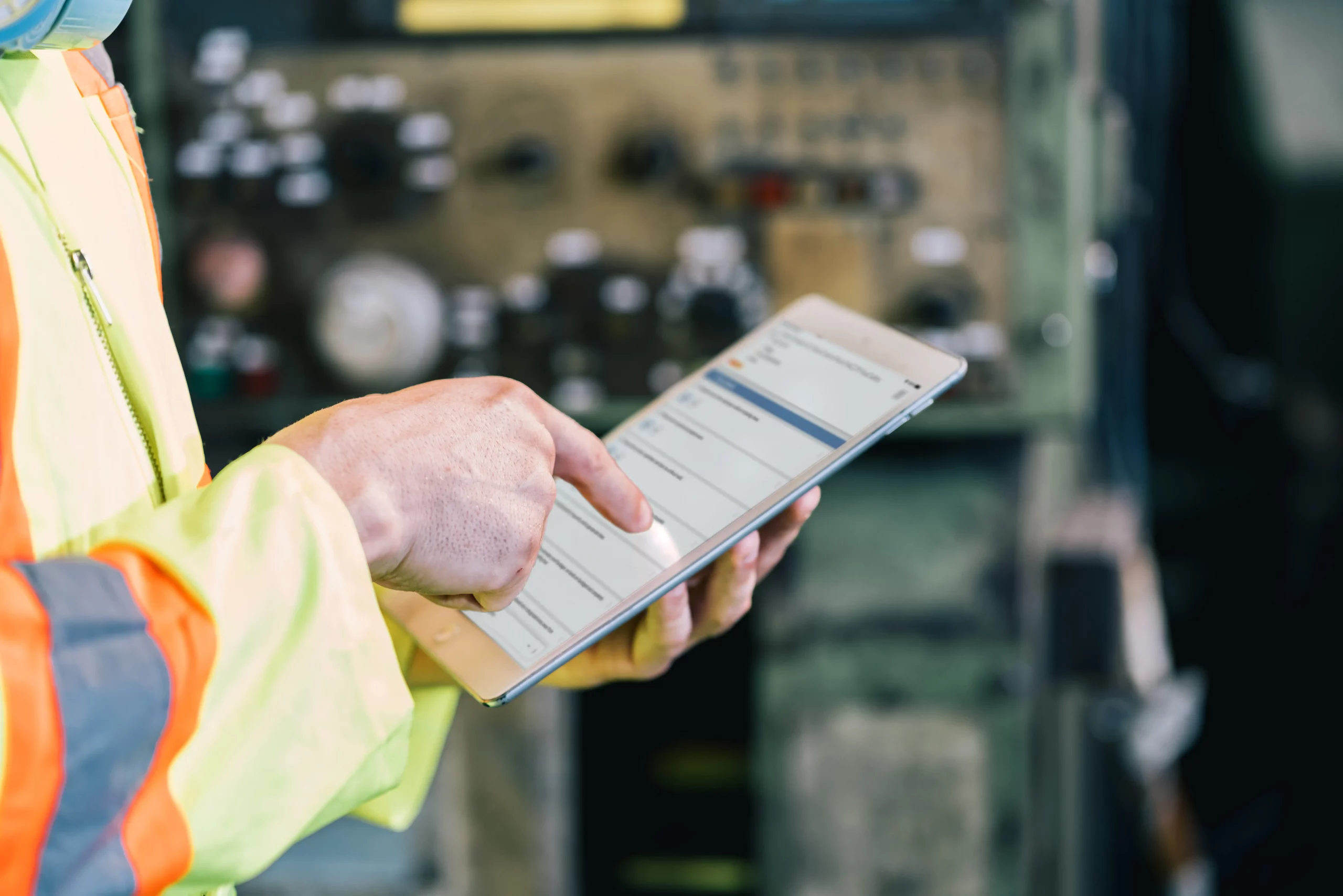
30+ Audit and inspection checklists free for download.
Which Type of Audit Program Should You Choose?
There are three basic types of audit compliance programs: Desktop, announced, and unannounced. Let’s take a look at all three.
- Desktop audits
Desktop audits are exactly what they sound like -audits that don’t require inspectors to attend in person. Instead, they focus on ensuring that key documents and certifications are up-to-date.
- Announced audits
Announced audits give suppliers time to prepare. While this self-assessment approach may prompt suppliers to address potential issues, it can also lead to problems being hidden from view on the audit date.
- Unannounced audits
Unannounced audits occur without warning and give inspectors a more accurate view of how suppliers operate day-to-day.
Examples of Supply Chain Compliance Measurements
For audits to deliver effective risk management, companies must conduct more than a simple surface evaluation. Here’s why: If suppliers meet basic compliance standards but are failing in other areas, they may not be a good fit.
Common supply chain metrics include:
- Cash-to-cash cycle time
This refers to the length of time between your payment of suppliers and the payment of customers for finished goods. The shorter, the better.
- Service rate
Service rate speaks to the percentage of supplier orders that are delivered on time. A low service rate may indicate the need for supplier reassessment.
- Accurately documented orders
Along with items received, are documents accurate? Given the role of complete documentation in compliance, accurate order details are critical.
- Total supply chain management cost (as a percentage of sales)
What are your supply chain management costs for a specific vendor compared to overall sales percentages? If these costs begin to creep up, it could indicate compliance or production issues. Depending on the issues identified across corporate social responsibility, environmental management, sustainability, or social compliance efforts, you may choose to create a corrective action plan to minimize further disruptions or seek out need providers across the global supply chain to help reduce the risk of non-compliance and potential fallout.
How to Prepare for a Supply Chain Compliance Audit
Whether you’re preparing to conduct a supply chain audit, are being audited by another company, or facing the prospect of a federal audit, it’s worth taking the time to prepare.
First, create a framework to measure current compliance. Given the increasingly complex (and changeable) nature of compliance requirements, it’s worth leveraging tools such as ESG checklists. This ensures all critical processes and components are evaluated and audit reports are accurate. On both sides of the audit equation, an ounce of preparation is worth a pound of cure — better to understand what you need to measure, how you need to measure it, and why it matters before audits start, rather than after the fact.
Put simply, supply chain compliance audits help streamline key processes and prepare companies for the possibility of unannounced regulatory evaluation.
You may also be interested in:
What is a Supply Chain Vulnerability Assessment and How to Perform One