More information is always better. The more you know about what’s happening in your organization, the better equipped you are to address and remediate potential safety problems.
Safety metrics make this possible. By measuring and tracking key performance indicators (KPIs), you can identify areas in need of improvement and create plans that help achieve this goal. In this piece, we look at the 5 top safety metrics your business should track to help reduce workplace risk.
Why Safety Metrics Matter
Safety KPI metrics allow companies to understand better what’s happening across operations — and why. For example, you might notice a general trend of incident rates increasing. Without hard data, this is more a feeling than a fact. Ultimately, this means your safety professionals could spend time and energy trying to solve the wrong problems.
By taking the time to measure and analyze specific data related to incident rates, meanwhile, your safety teams can understand both general trends and pinpoint areas that need improvement to enhance overall safety. Put simply, the more data, the better.
The Top 5 Safety Metrics
The nature of business operations means there’s almost an infinite number of metrics you could measure, depending on your current needs and safety objectives. While the top safety KPIs will differ based on your industry and current workforce challenges, there are 5 metrics worth measuring for any business.
1) Total Recordable Incident Rate (TRIR)
The OSHA TRIR Is a measure of the total number of recordable safety incidents and recordable injuries that occur across your business in a given period. Incidents that need to be reported include:
- Loss of consciousness
- Worker activity is restricted to an incident or they must be transferred to a different job
- Staff must take days away from work due to an incident
- Injuries sustained can’t be treated with a first aid kit
- A medical professional diagnoses a work-related health issue
To ensure you’re effectively tracking TRIR, it’s critical to implement safety management systems that prioritize incident reporting. This allows you to conduct comprehensive risk assessments.
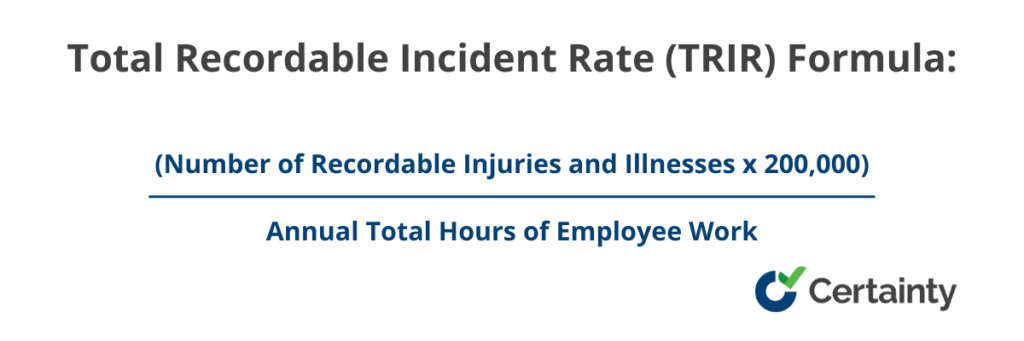
2) Days Away, Restricted or Transferred Rate (DART)
OSHA’s DART rate is a measure of the number of days that an employee is away from their job, on restricted or light duties, or must be transferred temporarily to another part of your organization. The higher your DART rate, the more likely there is a systemic safety issue that must be addressed.
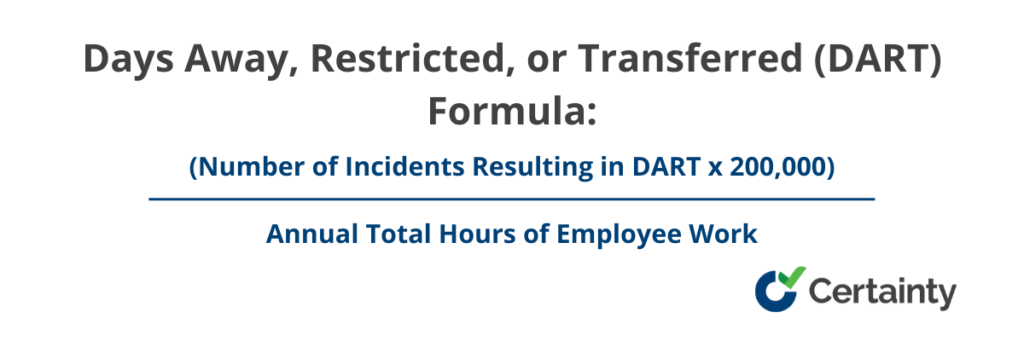
3) Average Time to Resolution of Issues
How long does it take to resolve issues? This metric measures the amount of time your business spends addressing and remediating issues to reduce total risk. The higher this metric, the greater the delay between the detection and the resolution of issues. What results is an increased chance of a reportable incident.
4) Lost Time Injury Frequency Rate (LTIFR)
This metric measures the amount of time lost to injury. Most companies measure the LTIFR per 1,000,000 hours worked. This means that if your team worked 1,500,000 hours over the measurement period and there were 10 incidents, you multiply 1,500,000 by 10 to get 15,000,000, then divide by 1,000,000 to get an LTIFR of 15 for the number of hours worked.
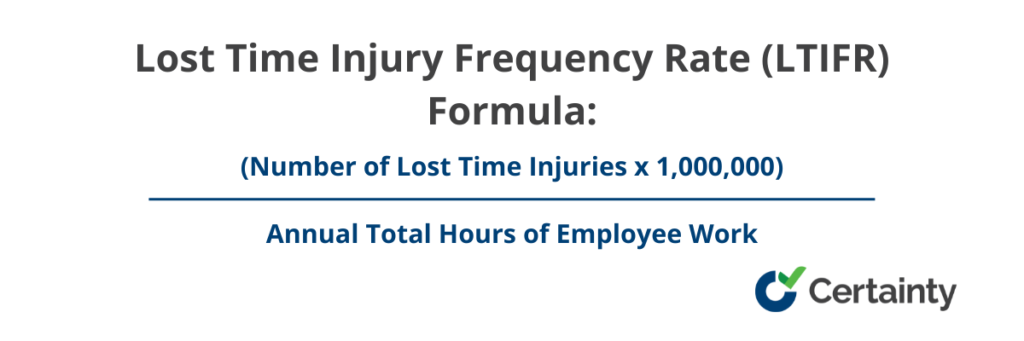
5) Near Miss Rates
Last but never least, it’s always worth tracking near miss rates. This metric measures things that could have happened and didn’t but were close enough to be considered worth recording. For example, a near miss might occur if an employee slips while carrying materials. Even if they don’t fall and injure themselves, the possibility of injury is high enough that it’s worth recording. If other staff slip into the same spot, meanwhile, it may suggest the need for corrective safety action or more in-depth employee training.
Using Metrics to Make Your Business Safer
Effective use of metrics can help make your business safer by creating a safety culture. For example, if you can effectively track the LTIFR across your organization, you can see if you’re making progress or heading in the wrong direction. If the overall rate of lost time due to injury is decreasing, it means that current safety processes are working as intended. If it’s going up, meanwhile, it means there’s more work to do. These metrics form the basis of safety training in your organization that can help lead to corrective actions that effectively reduce the total number of incidents and improve workplace safety.
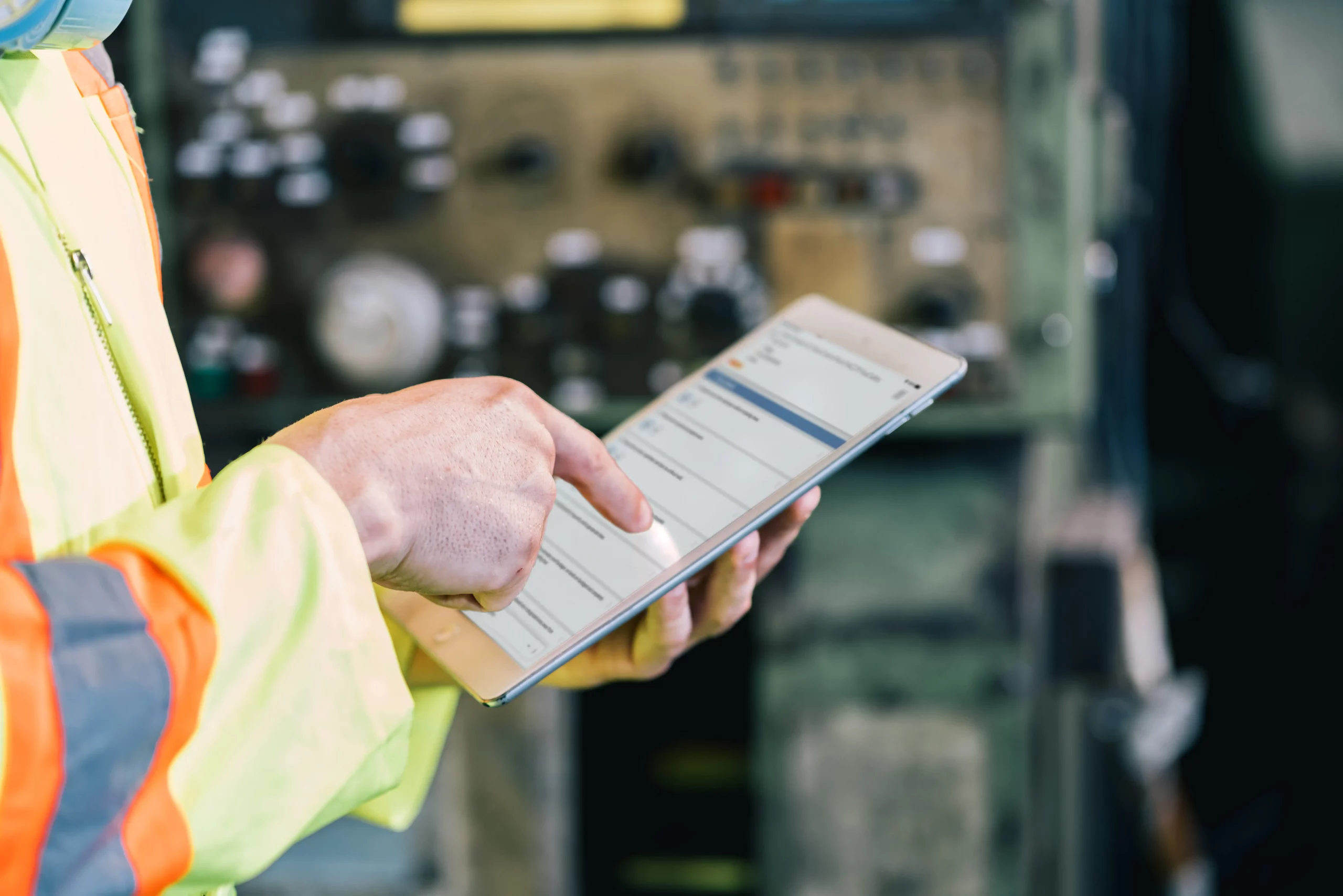
30+ Audit and inspection checklists free for download.
To leverage safety metrics, you need data about the current state of safety in your organization. This starts with data gathering. By using tools such as a behavioral-based safety observation checklist or a facility safety inspection checklist, you can identify potential areas of safety concern that require more in-depth analysis, in turn setting the stage for targeted safety metrics monitoring, targeted training courses, and continuous improvement.
You may also be interested in:
The Difference Between Leading and Lagging Safety Indicators