Table of contents
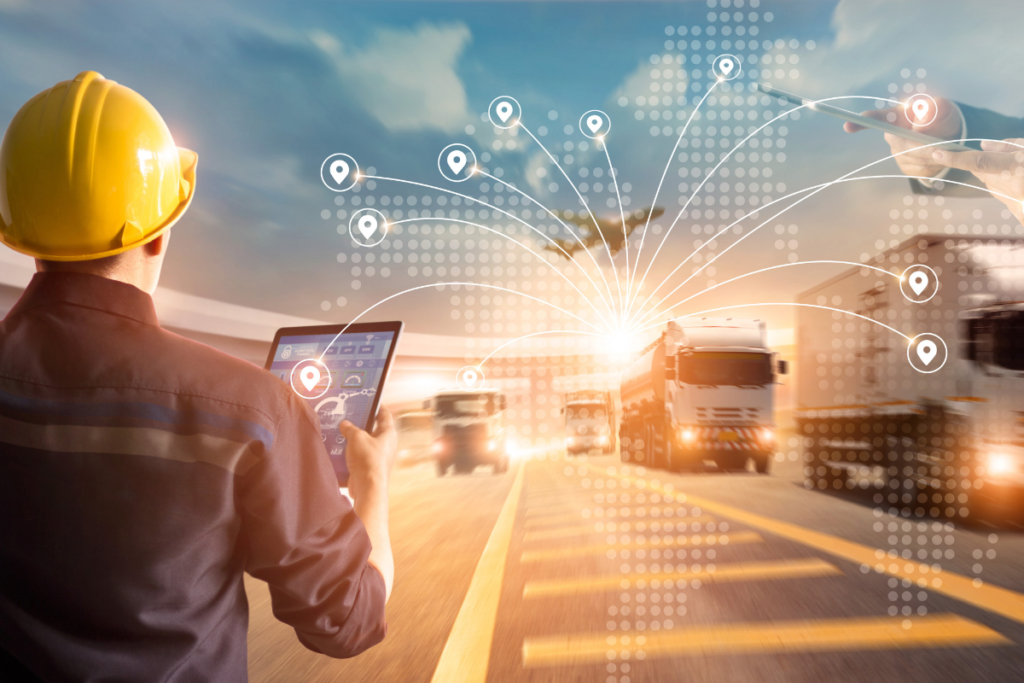
As the manufacturing industry continues to evolve and embrace interconnected global supply chains, effective third-party risk management (TPRM) has become a critical imperative. According to Deloitte, 87% of firms have experienced an incident with a third party that disrupted their operations, and 11% have experienced a complete failure in their vendor relationship. Moreover, only 31% of organizations manage third-party risk and issue tracking through an enterprise-wide tool capable of monitoring critical risk and performance indicators (KRIs, KPIs), according to KPMG.
Effective third-party risk management (TPRM) has emerged as a crucial requirement as the industrial sector continues to develop and use interconnected global supply chains. Deloitte estimates that 87% of businesses have had a third-party incident impair their operations, and 11% have had a vendor relationship completely breakdown. Furthermore, according to KPMG, just 31% of firms track third-party risks and issues using an enterprise-wide solution that can measure key risk and performance indicators (KRIs, KPIs).
These statistics are alarming, considering that the global pandemic has highlighted significant gaps in TPRM programs, as many manufacturers found themselves unable to provide uninterrupted services due to challenges with their suppliers and partners. In fact, the third-party risk management market is expected to grow at a strong CAGR of 14.7% between 2022 and 2032, reaching US$ 19.7 Bn by 2032.
Join us as we discuss TPRM, explore its impact on supply chain integrity, and discover how implementing a robust TPRM program can safeguard your manufacturing operations from severe vulnerabilities.
Understanding TPRM in the Manufacturing Context
The process of discovering, evaluating, monitoring, and reducing possible hazards connected to third-party connections is known as TPRM. Suppliers, distributors, contractors, consultants, service providers, and other organizations that assist or impact manufacturing operations are examples of third parties in the manufacturing sector.
The environment for manufacturing has drastically changed in recent years as a result of firms’ migration to worldwide supply chains and growing reliance on outsourcing. They have been able to do so in order to increase innovation, lower costs, increase efficiency, and enter new markets. However, it has also brought about fresh high-risk challenges and dangers, including:
- Problems with quality: Third-party vendors may not adhere to quality standards or requirements, which can lead to faulty items, recalls, or consumer complaints.
- Delivery snags: Third-party providers may encounter problems with their operations or transportation networks, leading to delivery delays or inventory shortages.
- Regulator non-compliance: Manufacturers may be subject to liability or fines if third-party vendors fail to follow industry regulations or certifications.
- Breach of cybersecurity: Third-party vendors may use insufficient cybersecurity processes or measures, which compromises the data or systems of manufacturers.
- Reputational damage: Third-party vendors may participate in unethical or unlawful activities, harming the reputation of manufacturers and their brands.
According to a report by KPMG International, 78% of global TPRM leaders believe inefficiencies in their TPRM programs are exposing them to reputational risk. Furthermore, the report also found that 85% of global businesses consider TPRM a strategic priority, up from 77% before the outbreak of the pandemic.
These results show that manufacturers must actively manage their third-party risks and make sure they have sufficient controls and oversight over their third-party partnerships.
Key Components of an Effective TPRM Program
A third-party risk management program is an organized and methodical method for controlling and reducing the potential hazards connected to third-party partnerships. Your TPRM program should have a number of connected procedures, such as:
Defining the Scope and Objectives of the TPRM Program
Specifying the goals and scope of a TPRM program is the first step in designing one. This entails responding to inquiries like:
- What kinds of partnerships with third parties are pertinent to industry-standard manufacturing operations?
- What types of risks, such as those related to reputation or quality, delivery or compliance, information security, or cybersecurity, could result from these business relationships?
- What are the TPRM program’s objectives and expectations, such as lowering risk exposure, boosting supply chain efficiency, fostering better vendor cooperation, or achieving regulatory compliance?
- How will the effectiveness and success of the TPRM program be assessed and reported, for example, through dashboards, reports, key performance indicators (KPIs), and key risk indicators (KRIs)?
Establishing a clear direction and focus for their TPRM operations, as well as aligning them with their overall company strategy, risk appetite, and culture, can be facilitated by manufacturers by clearly defining the scope and objectives of the TPRM program.
Establishing Roles and Responsibilities for TPRM Activities
Roles and duties for TPRM activities must be established as the next step in creating a TPRM program. This entails identifying and delegating activities and responsibilities to various organization stakeholders, including:
- The TPRM team: The group of people, such as risk managers, procurement managers, quality managers, or compliance managers, who are in charge of creating, carrying out, and managing the TPRM program.
- The relationship owners: The people in charge of starting, overseeing, and ending connections with third parties, such as project managers, product managers, or operations managers, are known as relationship owners.
- The subject matter experts: The people who are in charge of providing technical or functional expertise on particular facets of third-party interactions, such as legal counsel, security analysts, or quality auditors, are known as subject matter experts.
- Senior management: The individuals, such as executives, directors, or board members, who are in charge of giving strategic leadership, support, and approval for the TPRM program.
Manufacturers can assure accountability, ownership, and collaboration among all stakeholders involved in the TPRM program by establishing roles and responsibilities for TPRM activities.
Developing Policies and Procedures for TPRM Processes
The next stage is to create TPRM process policies and procedures. These are the regulations and industry standards that control how your TPRM activities are carried out, including:
- Supplier selection and due diligence: Conducting rigorous due diligence when choosing a new vendor, including evaluating their financial stability, quality control procedures, adherence to industry regulatory requirements and certifications, and compatibility with the expectations and values of the company.
- Risk assessment and categorization: Conducting risk assessments to identify potential weaknesses and threats posed by third-party relationships, analyzing various factors including the nature and scope of the relationship, its criticality and dependency, its geographic location and political stability, as well as the potential impact and likelihood of a risk occurrence.
- Vendor performance monitoring: Continuous monitoring of vendor performance involves gathering and analyzing data on key performance indicators (KPIs) such as product quality and defect rates, delivery timeliness and accuracy, customer satisfaction and feedback, regulatory compliance status, and issues.
- Supply chain mapping: In order to detect and evaluate potential risks and opportunities throughout the supply chain, a thorough and visual depiction of all the third-party relationships engaged in the manufacturing supply chain must be created.
- Collaboration and transparency: Promoting solid working relationships with outside vendors, open communication, common objectives, and shared commitment to risk management.
- Continuity planning: Planning for continuity means creating thorough business continuity plans that include the steps and materials needed to keep or resume manufacturing activities in the case of an interruption brought on by a third-party failure.
- Audit and review: Perform routine audits or reviews to assess and improve the TPRM program as well as to confirm vendor performance and compliance.
If you’re struggling to decide how to audit your suppliers, try Certainty’s free-to-download Supplier Social & Environmental Compliance Checklist.
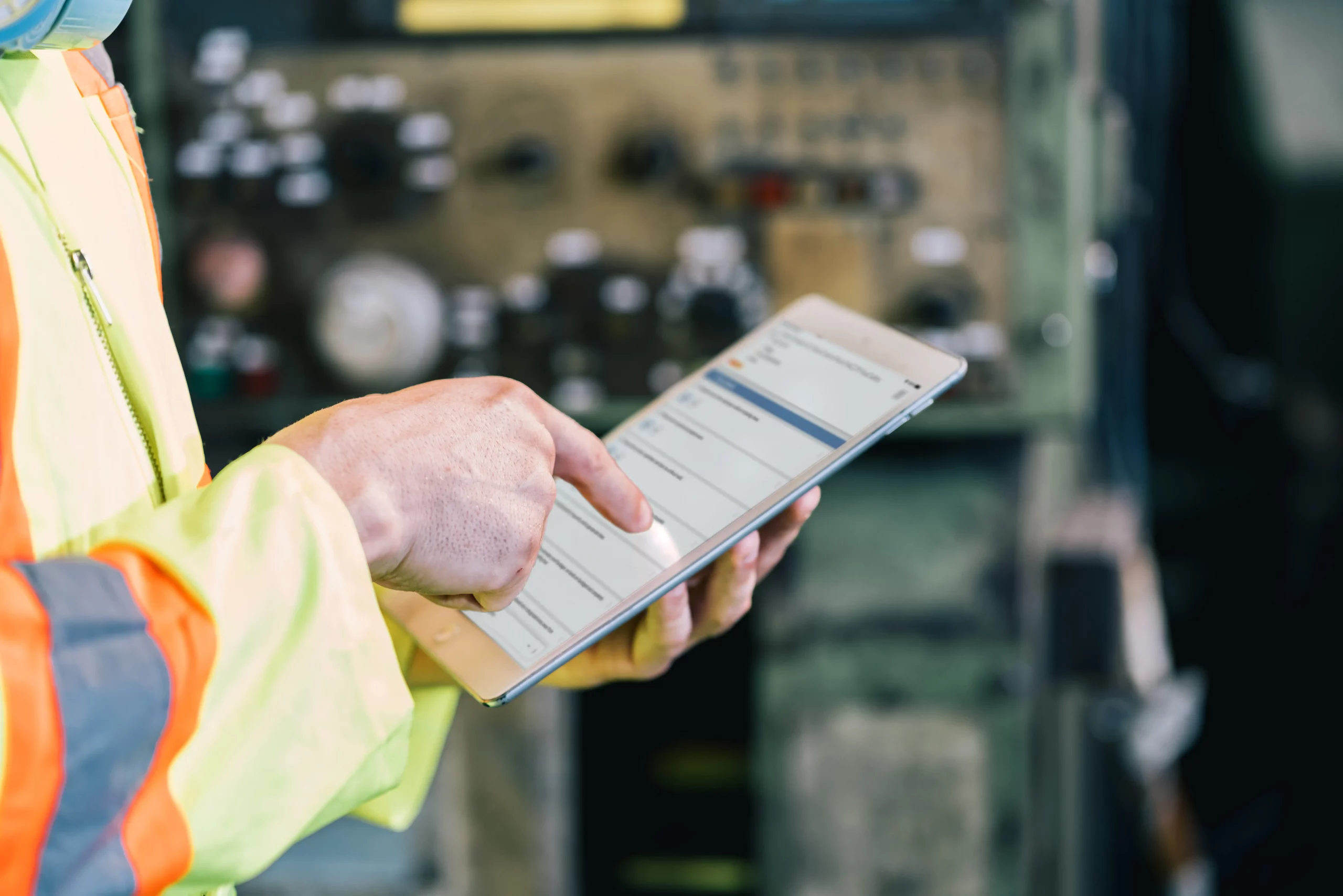
30+ Audit and inspection checklists free for download.
Best Practices for Enhancing Supply Chain Integrity Through TPRM
Manufacturers can improve the integrity and resilience of their supply chains and gain a competitive advantage in the market by putting a strong TPRM program in place. The following are some examples of best practices for improving supply chain integrity with TPRM:
Supply Chain Mapping
The process of developing a thorough and visual depiction of all the third-party links involved in the manufacturing supply chain is known as supply chain mapping. As a result, producers can:
- Determine and evaluate prospective dangers and opportunities within the supply chain
- Enhance the supply chain’s information, material, and product movement.
- Increasing the status and performance of the supply chain’s visibility and transparency
- Create effective supply chain risk mitigation and emergency plans.
Collaboration and Transparency
Building great relationships with third-party providers and developing mutual trust and commitment need collaboration and transparency. This entails:
- Sharing objectives, anticipations, and criticism with suppliers
- Providing assistance and direction to suppliers
- Including vendors in decision-making and problem-solving procedures
- Recognizing and recognizing innovative performance from suppliers
Continuity Planning
Planning for continuity entails creating comprehensive business continuity plans that include the steps and materials needed to keep or resume manufacturing activities in the case of a disruption brought on by a third-party failure. This entails:
- Identifying possible outcomes and how they might affect manufacturing operations
- Creating alternative sourcing plans and backup plans for each eventuality
- Checking and confirming the continuity plans’ efficacy
Audit and Review
To check vendor performance and compliance, as well as to assess and improve the TPRM program, periodic audits or reviews are conducted. As a result, producers can:
- Verify that suppliers follow regulations, dates for delivery, and quality standards.
- Determine and correct any shortcomings or problems with vendor performance or compliance.
- Measure and evaluate the results and effectiveness of the TPRM program.
- Find and implement TPRM program improvement possibilities.
Streamlining TPRM Processes for Efficiency and Effectiveness
Manufacturers should make use of automation and technological solutions that can:
- Automate the collection, analysis, and reporting of data on the performance and hazards of third parties.
- Utilize dashboards, alerts, and notifications to improve risk visibility and response times.
- Enhance teamwork and communication with outside vendors by using online tools or websites
- Integrate TPRM processes with other operational procedures like purchasing, quality control, compliance monitoring, etc.
Additionally, producers must make sure they abide by all pertinent legal requirements, including those governed by industry-specific standards and certifications. For instance, producers in the aerospace sector might be required to follow AS9100, whereas manufacturers in the automotive sector would be required to follow IATF 16949.
Finally, manufacturers should continuously evaluate and refine their TPRM strategies, staying abreast of emerging risks, industry trends, and best practices. This can help them adapt to changing market conditions, customer expectations, and competitive pressures.
The Solution to Thriving Vendor Risk Assessments
TPRM is a crucial element of manufacturing operations because it may assist businesses in reducing potential risks related to their third-party connections, improving the integrity and robustness of their supply chains, and gaining a competitive edge in the market.
TPRM is not a one-time task or a box to be checked, though. For it to remain relevant and effective, it needs constant care, investment, and refinement.
Look no further than Certainty Software if you’re seeking a trustworthy partner to assist you in putting an effective TPRM program tailored to your unique needs into place. Leading supplier of operational risk solutions for businesses in the manufacturing industry, Certainty Software streamlines:
- Audit and inspection management: Manage your audit and inspection processes by automating and streamlining everything from planning and carrying out audits and inspections to documenting and disseminating conclusions and recommendations to validating and concluding corrective actions.
- Reporting: Reporting: Create and access real-time reports and dashboards on the performance and risks of your third parties using templates, filters, and charts that are completely configurable. Analyze patterns, pinpoint problems and opportunities, and assess the efficiency and efficacy of your TPRM program.
- Corrective actions: Organize and keep track of your corrective actions by delegating tasks and setting deadlines, reminding people to do them, keeping an eye on their progress and status, and confirming the consequences. Make sure your corrective actions are carried out promptly and successfully, and stop the recurrence of problems.
Don’t wait until it’s too late. Take proactive steps towards building a robust risk management strategy today. Contact us to book a demo. We look forward to hearing from you.