Table of contents
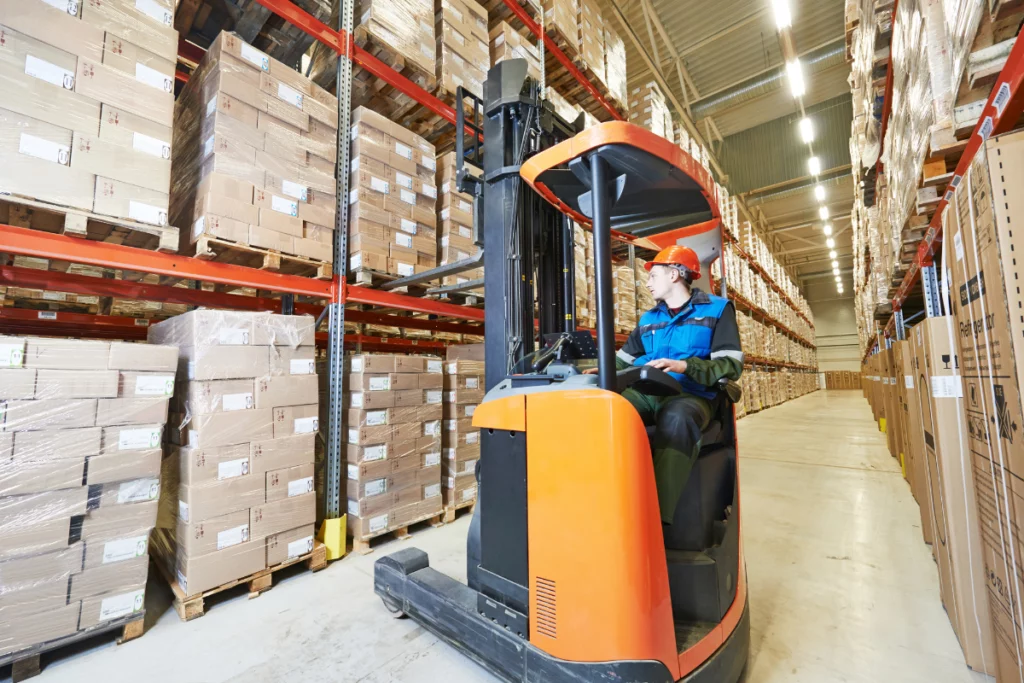
What is Warehouse Safety?
Safety is a vital aspect of any business that operates in a warehouse environment. Warehouse safety refers to the measures and practices that are implemented to protect the health and well-being of warehouse workers, as well as the property and equipment in warehousing. According to the U.S. Bureau of Labor Statistics, fatalities in the warehousing sector are continuing to increase. From 2021 to 2022, fatalities rose from 46 to 50. Warehouse safety continues to be a major problem for organizations and the need for greater risk mitigation is more prevalent than ever.
Why Investing in Warehouse Employee Safety is Important
Investing in warehouse employee safety is essential to ensure compliance with the relevant safety standards and regulations. Investing in warehouse safety not only protects the workers and the business, but also improves efficiency, quality, and reputation. As per The Occupational Safety and Health Administration (OSHA), for every $1 spent on injury prevention, businesses can save $2 to $6 in reduced costs and increased revenues.
The Biggest Safety Issues in Warehouses
Investing in warehouse safety isn’t enough if you do not understand the biggest safety issues and risks inside warehouses. You need to identify and assess the potential hazards and threats that can cause injuries and accidents. Once that is done, then you can implement the appropriate preventive and corrective actions to eliminate or minimize them.
Here are some of the most common causes of workplace injuries in warehouse environments:
Slips and trips:
- Slips and trips are one of the leading causes of warehouse injuries accounting for about 25% of OSHA’s reported injuries.
- Slips and trips can occur due to wet or slippery floors, uneven or damaged surfaces, poor lighting, cluttered or obstructed walkways, loose wires or cords, spilled liquids or materials, etc.
Falling objects:
- Falling objects can cause severe injuries or even death to warehouse workers.
- These hazards occur largely due to improper stacking or storage of goods, overloading or collapsing of racks or shelves, faulty or loose equipment, or strong winds or earthquakes.
Overexertion:
- According to Liberty Mutual Insurance, overexertion with material handling is the leading cost of disabling workplace injuries accounting for over USD 13B annually.
- Lifting, pushing, pulling, or carrying heavy or bulky objects, working in awkward or uncomfortable postures, and working for long hours or without breaks are just some examples of overexertion.
Falls:
- The second leading cost of injuries according to Liberty Mutual Insurance, is same-level falls cost approximately USD 10.58B annually.
Moving parts:
- Moving components are the essential elements of machinery, equipment, or vehicles that undergo movement or rotation.
- This can be conveyor belts, rollers, gears, chains, blades, and more.
- These dynamic components possess the potential to cause injuries or accidents by ensnaring, crushing, slicing, or entangling the limbs, clothing, or hair of workers, or by propelling objects or materials at substantial velocity or force.
Working with and around heavy equipment:
- When discussing heavy equipment, these are the large and powerful machines and vehicles used in warehouse operations.
- These include forklifts, pallet jacks, cranes, trucks, and more.
- Accidents can occur when workers or objects are struck, run over, or trapped. There is also the risk of tipping over or falling, as well as the possibility of malfunctioning or breaking down. Additionally, it is important to consider the noise, vibration, and fumes that they may emit.
Hazardous materials:
- These refer to substances that have the potential to jeopardize the well-being of workers or the environment.
- Hazardous materials include chemicals, gases, liquids, dust, and more.
- Their presence can result in injuries or accidents, including burns, poisoning, suffocation, explosions, or contamination of workers and the warehouse.
Fire:
- Fire poses a grave threat to warehouses, with the potential to cause extensive damage and endanger lives.
- Neglecting fire safety measures can lead to severe injuries including burns, scorching, or even the melting of workers or warehouse infrastructure.
- Additionally, fires can generate smoke, intense heat, and flames, which may destroy warehouse property and inventory.
Ignorance:
- Refers to a lack of knowledge, information, or attention that can result in hazardous behaviors or decisions within the warehouse.
- This lack of awareness can lead to injuries or accidents by disregarding safety rules and procedures, failing to identify or report safety hazards or incidents, mishandling equipment or materials, or causing distractions or disruptions among fellow workers.
Warehouse Safety Tips
Now that you know some of the biggest safety issues and risks that can occur in your warehouse, you may wonder how you can prevent them and ensure a safe and productive warehouse environment. Here are some of the best warehouse safety tips that you can follow and implement in your warehouse:
Properly ventilate work areas
Maintaining a safe and comfortable work environment in your warehouse requires proper ventilation. This means limiting the accumulation of dangerous materials, such as dust, fumes, gases, or vapors. These materials can lead to worker headaches, nausea, or exhaustion can be avoided with proper ventilation. In addition to controlling humidity and temperature, proper ventilation keeps workers and equipment from freezing or overheating in the warehouse.
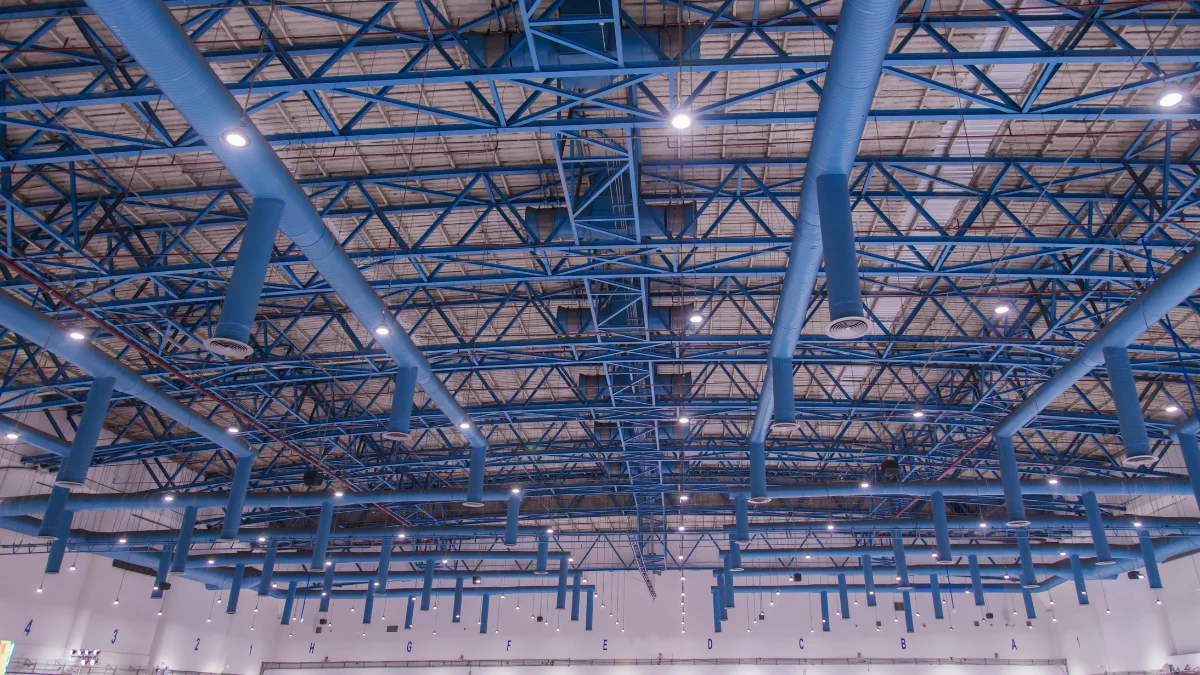
Here are some things to keep in mind in terms of warehouse ventilation:
- Ample ventilation systems that can circulate fresh air and remove contaminated air from the warehouse should be installed and maintained. Examples of these systems are fans, vents, ducts, and exhausts.
- Use alarms or detectors to notify the workers of any unsafe or excessive amounts of toxic chemicals.
- Airflow should not be obstructed or blocked.
- Use masks or filters to keep the workers from breathing in or consuming the dust or other particles.
Assess storage racks
If storage racks are not set up, maintained, or utilized properly, they may collapse, topple over, or drop the goods that are kept on them.
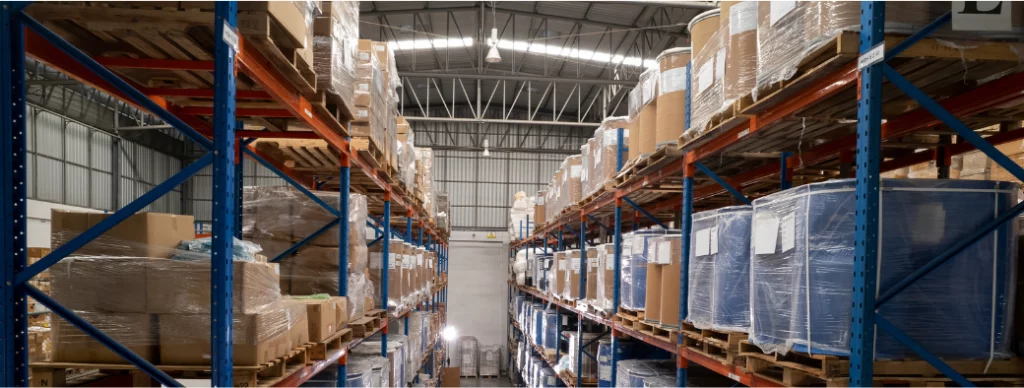
Not just a simple build and leave it be, storage racks require continuous attention and a meticulous eye for detail. Here are some of the essential considerations regarding your warehouse’s storage racks:
- Regularly examine and evaluate the storage racks. Look for indications of deterioration, use, or corrosion, such as cracks, bends, dents, rust, or loose fasteners.
- When installing, maintaining, and using the storage racks, follow the manufacturer’s guidelines and instructions. Pay particular attention to the weight restrictions, load distribution, and clearance criteria.
- To load and unload the goods on the racks, use the proper tools and techniques. Do not overfill, underfill, or unbalance the racks.
- Use guards, barriers, or nets to keep the products from tumbling off the racks after securing and stabilizing the racks to the floor, wall, or ceiling.
Enforce safe vehicle operation
Ensuring vehicle safety is of utmost importance in warehouse operations, where various vehicles like forklifts, pallet jacks, cranes, and trucks are used. This crucial aspect prevents any potential injuries or accidents involving the vehicles, workers, or warehouse property.
Something to consider, OSHA’s most recent estimates state that between 35,000 and 62,000 injuries each year are to forklift incidents.
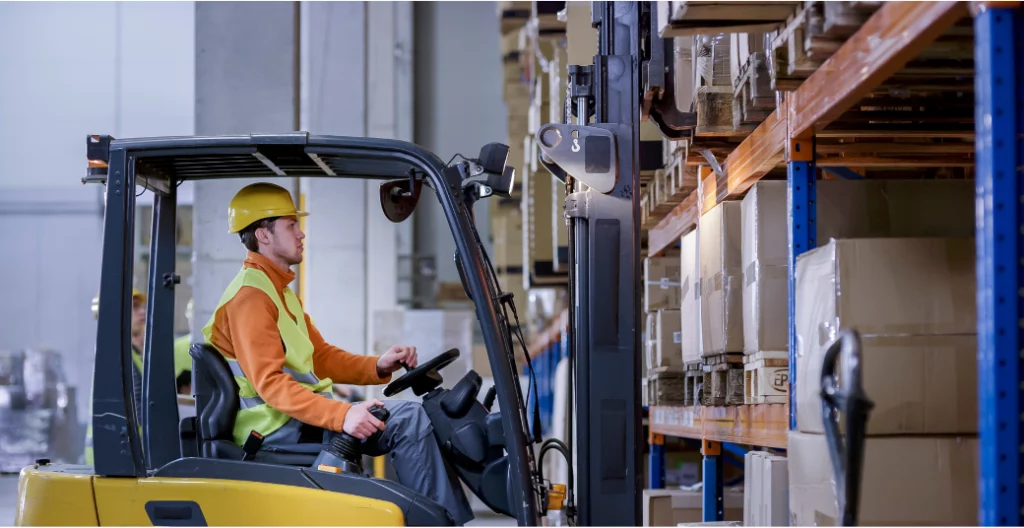
Warehouse operations should at minimum conduct these steps to proactively prevent vehicle-related injuries:
- Employees such as forklift operators should be trained, certified, and equipped with the skills, knowledge, and experience needed to operate them safely and effectively.
- Regularly examine and repair the vehicles. Look for any damage, malfunctions, or flaws like worn brakes, flat tires, faulty lights, or fluid leaks.
- Observe the traffic laws and guidelines when driving through the warehouse. Make use of any available markings, signs, signals, or lights to direct and regulate traffic flow.
- Use horns, sirens, or alarms to alert the workers to the presence or impending approach of the vehicle. Maintain a safe distance and visibility between the vehicles and the workers or other objects
Implement ergonomic-focused working
Working with an ergonomic focus can help avoid overexertion and musculoskeletal disorders, which include sprains, strains, and fractures. These conditions can be brought on by pushing, pulling, lifting, or carrying heavy or bulky objects; working in awkward or uncomfortable postures; working long hours without a break; working in extreme temperatures or humidity; etc.
Some key considerations for making your warehouse work environment more ergonomically safe include:
- Assign the workers the appropriate tools and equipment. This could be carts, lifters, gloves, and scissors. Make sure they are easily accessible and in excellent working order.
- Workstations and chairs should be adjusted to accommodate employees’ weight, height, and posture. They should also be free to move or alter positions as needed.
- Provide workers with proper lighting and ventilation. Also alleviate strain and tension on their feet, legs, and backs by using anti-fatigue mats, cushions, or footrests.
- Schedule regular breaks and rest periods for the workers, and encourage them to stretch, relax, and hydrate during their shifts.
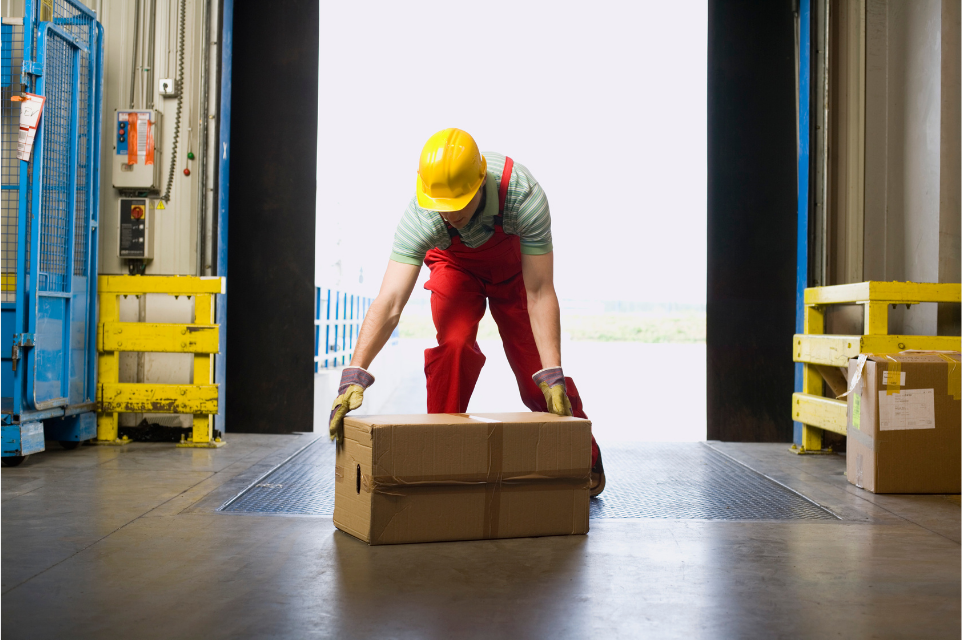
Provide the proper safety training to employees
One of the most crucial and practical strategies to raise warehouse safety and reduce accidents and injuries is via training. Employees who are trained are better equipped to carry out their duties in the warehouse safely, effectively, and with the knowledge and awareness needed to identify and steer clear of any dangers and hazards.
Be sure that your employee warehouse safety training includes these essentials:
- Provide a comprehensive training program. It should cover equipment operation and maintenance, emergency response and evacuation, danger detection and reporting, first aid, and warehouse safety regulations.
- Deliver the training using a variety of techniques and formats. These formats could be lectures, films, role-playing, simulations, and hands-on activities. Try to customize it to the individual requirements and skill levels of the employees.
- Assess the workers’ performance and learning. Also, provide them with comments, and offer coaching so they may advance their knowledge and abilities.
- Regularly update and refresh the training. When this is done, notify the staff of any modifications to the rules, guidelines, or procedures about warehouse safety.
Install warehouse safety signs
Informing employees about potential dangers and hazards reminds them of safety regulations and procedures. Also, it directs them toward safe and proper activities or behaviors, warehouse safety signs can help avoid accidents and injuries.
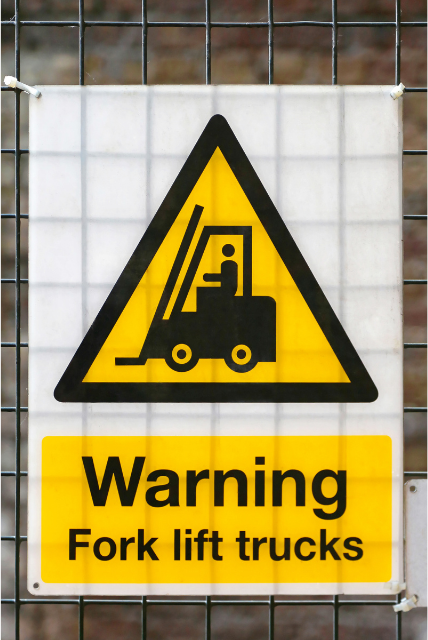
Provide the proper safety equipment
Personal protective equipment (PPE), or safety gear, is what employees wear or use in the warehouse to guard against accidents or injuries. Hard hats, goggles, gloves, masks, earplugs, vests, boots, and other things might be considered safety gear. Workplace dangers and hazards, such as falling items, moving components, toxic chemicals, fire, noise, etc., can be prevented or lessened by the use of safety gear.
Access OSHA’s guidance document on PPE here.
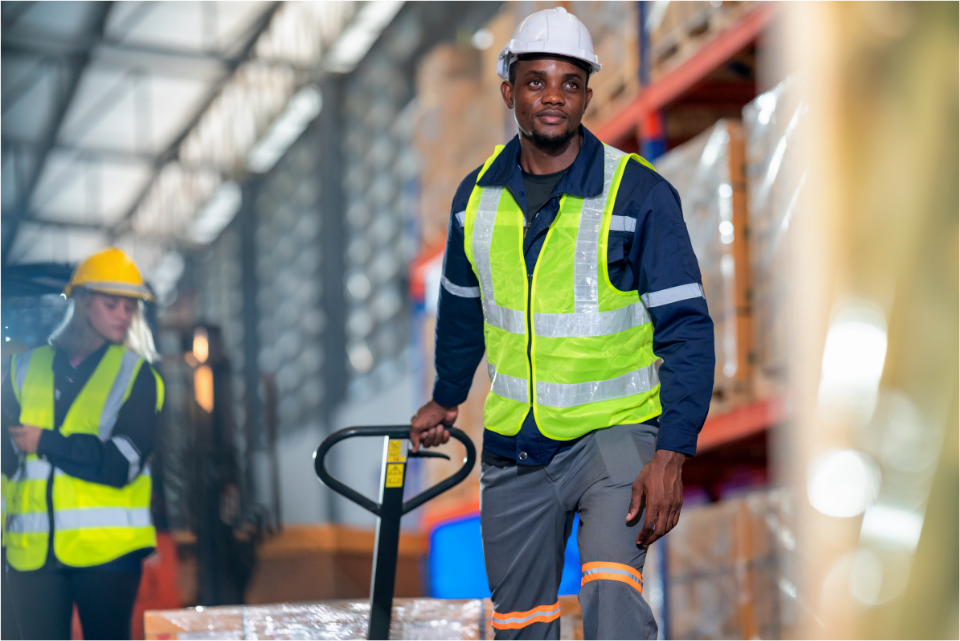
Maintain a clean workspace and emergency exit paths
Keeping the workstation, pathways, and emergency exits tidy is crucial to creating a secure and effective warehouse atmosphere. A neat workplace helps reduce the risk of fire, falling objects, trips and falls, and other dangers that might arise from an untidy or congested warehouse. A clean work environment is a safe work environment.
Build a culture of safety
Encouraging and maintaining a proactive, upbeat attitude and conduct around safety in the warehouse is the process of establishing a culture of safety. In addition to promoting involvement and collaboration in programs and activities aimed at enhancing and improving safety, a culture of safety may assist in avoiding injuries and accidents by instilling in workers and management a feeling of accountability, duty, and dedication.
But what does a warehouse safety culture look like? Here are a few key components:
- A clear and consistent vision and purpose for warehouse safety should be established and communicated, and the safety goals and objectives should be in line with the warehouse’s performance and strategy.
- Encourage employee and management participation and empowerment in the decision-making and problem-solving processes related to safety, and appreciate their input and recommendations for enhancing and improving safety.
- Give employees and management credit for their contributions to and accomplishments in the area of safety, and acknowledge and disseminate best practices and success stories in this area.
Hold safety meetings
The purpose of safety meetings is to go over and talk about various safety-related themes and difficulties in the warehouse. By giving employees and management a greater understanding of safety issues and the chance to share ideas and information, safety meetings may help reduce the number of accidents and injuries that occur. Safety meetings may also contribute to the development of a safety culture by improving management and employee participation in safety matters and by fostering a sense of trust and cooperation in safety among them.
Certainty’s Warehouse Safety Checklist
As you can see, many factors and elements affect warehouse safety, and many tips and practices that can improve warehouse safety. However, managing and overseeing warehouse safety can be a challenging and complex task, especially if you do not have a clear and comprehensive guide or tool to help you.
That is why we have created Certainty’s Warehouse Safety Checklist. This free and easy-to-use resource covers every aspect of general warehouse safety and sets a strong foundation for a proactive and safe warehouse work environment.
Our Warehouse Safety Checklist is more than just a checklist. It is a powerful and practical assessment tool that can help you achieve and maintain a high level of warehouse safety and compliance, and to optimize protecting your workers, your business, and your customers. To get started with Certainty’s Warehouse Safety Checklist, download it from our website, or contact us for a free demo.
You might also be interested in: