Quality is an indispensable factor in the success of any organization. Think about it: as customers, we all want product quality and services that truly meet our needs and expectations. By consistently delivering superior quality, organizations gain a competitive edge in the market, fostering heightened customer satisfaction and unwavering loyalty.
Yet, maintaining steady quality is no small feat. Organizations grapple with a myriad of challenges to ensure their processes operate at optimal effectiveness and efficiency while ensuring their products and services remain untainted by defects and errors. The ramifications of subpar quality are far-reaching, encompassing increased costs, diminished profitability, tarnished reputation, and the potential loss of valued customers.
Enter Layered Process Audits (LPAs), the guardian angels of quality improvement and defect prevention. LPAs offer a meticulously structured and systematic approach to auditing processes and systems where auditors employ standardized checklists to precisely assess compliance with process requirements. Serving as a cornerstone of quality control, LPAs elevate safety, efficiency, and productivity to new heights.
The Need for Layered Process Audits
Quality involves a purposeful strategy that includes planning, execution, monitoring, and continual improvement. It doesn’t happen by accident. By offering a framework to create, implement, control, measure, and improve processes, quality management systems (QMS) serve as the cornerstone for businesses working to attain consistent quality.
The primary role of LPAs is to identify and prevent defects at their source by ensuring that processes are consistently followed and executed correctly.
By doing so, LPAs enable organizations to:
- Reduce costs associated with poor quality
- Enhance customer satisfaction, reduce customer complaints, and foster loyalty
- Improve process efficiency and productivity
- Cultivate employee engagement and accountability
- Nurture a culture of quality and continuous improvement
The functionality of LPAs becomes even more evident for organizations operating in complex, dynamic, or regulated environments where stringent quality standards and the repercussions of errors are substantial. Consider the following examples:
Manufacturing: LPAs empower the manufacturing process by ensuring that their products consistently meet specifications, comply with regulations, and perform reliably.
Healthcare: LPAs play a pivotal role in enabling healthcare providers to safeguard that their services effectively meet patient needs, comply with rigorous standards, and prevent errors.
Construction: LPAs equip construction companies with the means to guarantee that their projects adhere to design requirements, comply with building codes, and prevent defects.
However, relying solely on QMS falls short of ensuring the desired level of quality. QMS heavily depends on product inspections and testing to verify compliance with quality standards. While these methods are undoubtedly crucial, they come with certain limitations:
- They’re reactive, not proactive: Rather than preventing errors at the source, the main goal is to find them after they have already happened.
- They can be expensive: QMS requires sampling, testing, reworking, scrapping, and producing waste, which raises costs and demands more time.
- They are not infallible: Due to human or sampling error, some faults may go undetected, opening the door to possible problems.
- They deal with symptoms, not causes: Quality Management Systems sometimes concentrate on treating the outward signs rather than addressing the issues that are producing the flaws.
Organizations should use Layered Process Audits (LPAs) in addition to their QMS to get around these restrictions. LPAs are an example of a quality technique that focuses on watching and validating how items are manufactured rather than on evaluating finished products. LPAs are distinguished by the fact that all employees participate in the auditing process rather than just the quality department.
The Layered Process Audit Framework
Layered Process Audits (LPAs) operate on a straightforward yet robust framework comprising three essential principles and components:
Layered
LPAs are a multi-tiered endeavor involving various levels within the organization, spanning from the shop floor to senior management. Each layer has a different frequency, scope, and coverage of the audits. The higher the layer, the less frequent but more comprehensive the audits are. The lower the layer, the more frequent but more focused the audits are. This ensures that the processes are audited from multiple perspectives and at multiple levels of detail.
Process
As we’ve discussed, Layered Process Audits are focused on the processes rather than the products or outcomes. Their primary objective is to verify that processes are being diligently and consistently followed under established standards and procedures. LPAs also identify any deviations, nonconformities, or opportunities for improvement within the processes themselves.
Audit
Trained auditors spearhead LPAs, utilizing standardized checklists to assess compliance with process requirements. Instead of inspecting products or services after completion, auditors observe and validate how products are made or services are delivered. They meticulously document and report their findings, along with recommendations for corrective and preventive actions. Their primary objective is to verify that processes are being diligently and consistently followed under established standards and procedures. LPAs also identify any deviations, nonconformities, or opportunities for improvement within the processes themselves.
Dissecting the 3 Layers of Layered Process Audits
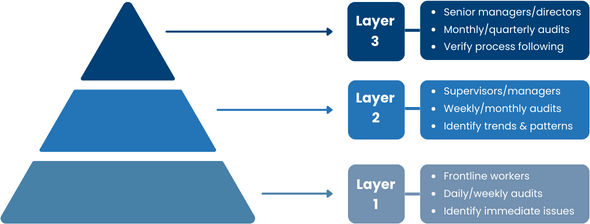
Layer 1
This foundational layer consists of operators, technicians, or frontline workers directly involved in the processes. They carry out daily or weekly audits of their own processes, using a simple checklist that covers the critical steps or control points. Their focus is to ensure adherence to standard work instructions or procedures while meeting quality requirements. Layer 1 audits swiftly identify and address any immediate problems or issues.
Layer 2
The intermediate layer comprises supervisors, managers, or team leaders responsible for overseeing the processes. They conduct weekly or monthly audits within their specific area or department, utilizing a more comprehensive checklist that encompasses various aspects of the processes. They aim to validate that their subordinates are following the prescribed work instructions or procedures, meeting quality requirements, and identifying any emerging trends or patterns that warrant further analysis.
Layer 3
At the uppermost level of the organization, senior managers, directors, or executives possess a broad perspective of the entire process landscape. They conduct monthly or quarterly audits across multiple areas or departments, employing a comprehensive checklist that covers all facets of the processes. Layer 3 audits verify that subordinates are following the necessary processes, promoting an effective overall production system
4 Steps of Layered Process Audits
Building upon the foundation of a well-designed LPA program, the process of conducting LPAs involves a series of key activities aimed at validating processes, implementing corrective actions, and evaluating performance. In this section, we will delve into these activities to provide a comprehensive understanding of how to conduct LPAs effectively.
The duration of an LPA can vary depending on several factors, including the complexity and size of the organization, the number of processes being audited, and the depth of the audit itself. On average, an LPA can range from a few minutes to several days, depending on the scope and coverage. It is essential to allocate sufficient time for each audit to ensure a thorough assessment of the processes and identify any potential areas for improvement.
If you’d like to continue learning about Layered Process Audits, please download our LPA Whitepaper resource.
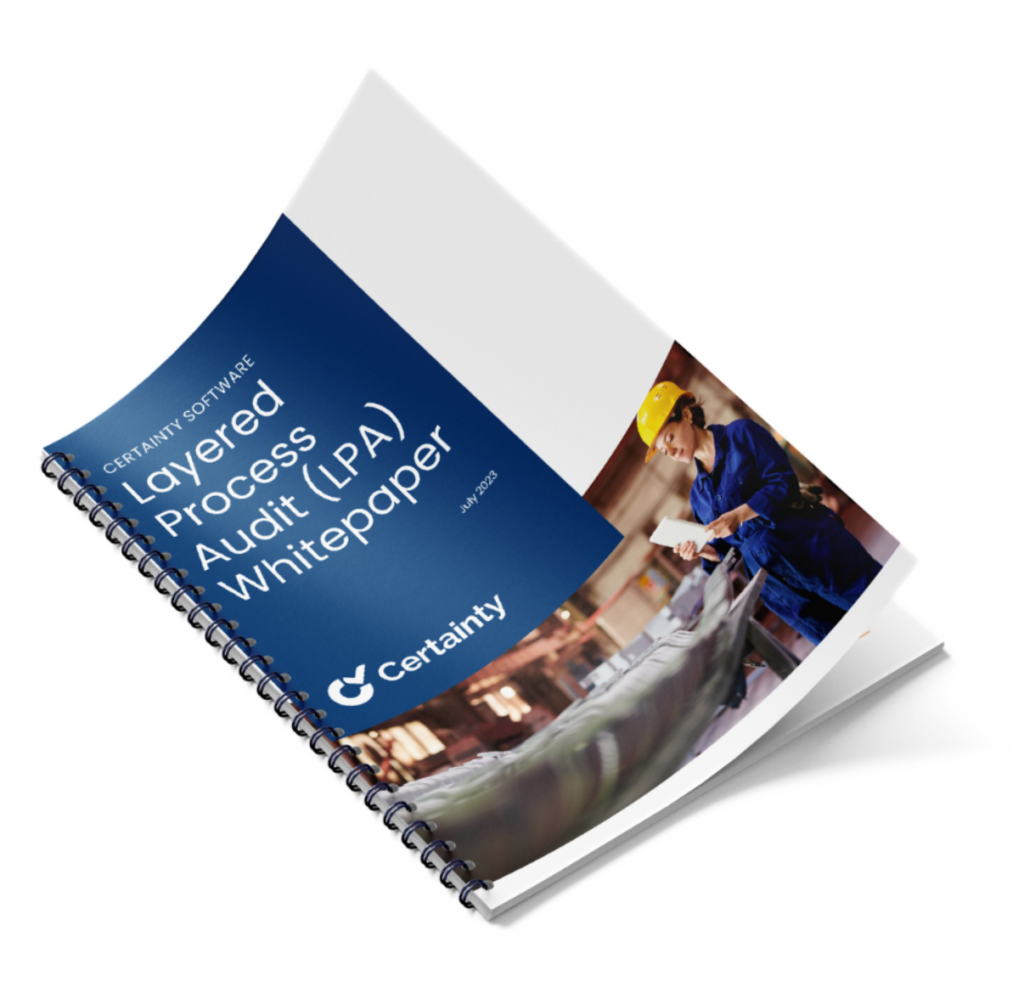
In addition to what we’ve already covered, our LPA Whitepaper dives deeper into topics such as:
- A full breakdown of all 4 steps to a Layered Process Audit
- The 3 key elements of LPA and how they work cohesively
- How performance metrics and data analysis take Layered Process Audit management to the next level
- Integrating a Layered Process Audit Plan with your QMS (ISO, Lean, Sigma, etc.)
- The biggest challenges of LPA implementation and tips for your LPA team to surpass these hurdles
- Our thoughts on future trends and innovation of the LPA system
We also offer free-to-download process audit checklist templates to help you track your compliance immediately. Check out our checklist library here.
Complete the form below to download our Layered Process Audit Whitepaper.